Control System Upgrades
Cross Company Control System Upgrades
If your facility has an aging control system, then it is time to start planning for an upgrade or migration before it becomes obsolete. Once a control system becomes obsolete, the costs of maintaining can triple or more. Cross Company is readily available to provide partial or turnkey services as needed for software and hardware upgrades. If unsure about possible options as related to cost, Cross technical advisors can prepare a comparative analysis so that you can make the best decision for your facility. After the upgrade is complete, Cross Company has dedicated services to maintain and keep your systems up to date with full control system lifecycle support.
For many control system end-users, one of the most pressing questions is when to upgrade an outdated or legacy control system. While the current system may be working as intended, if you’re using a control system that hasn’t been touched in a decade, an upgrade may be overdue.
Interested in learning more about how Cross company can help your operation? Contact us today to discuss your project or application with a Cross team member.
The Price of Not Upgrading
In industrial production with timelines, price is an important consideration. Common concerns are the downtime associated with implementing a control system update. As well as the extra time required to update procedures with both operators and operations.
But how will these costs compare to the costs associated with a critical security failure? Or a control system that becomes completely obsolete?
Everything comes with a price. Don’t let your control system become so outdated that you have to pay a significantly higher one.
Work stoppage
Unplanned downtime
Increased maintenance costs
Safety risks
Risks of Not Upgrading
Though an existing, older control system may not be obsolete, it may be out of date. Outdated systems pose risks of their own, including end of life vulnerabilities, future obsolescence, and increased downtime.
End Of Life
End of life control system software poses an increased risk for critical security failures. Obsolete software with otherwise functional hardware creates the greatest risk for these failures. Some plants will maintain older DCS systems in an attempt to mitigate cyber threats. However, end of life software is only becoming more and more vulnerable in terms of cybersecurity. Don’t wait until it’s too late.
Obsolescence
As control systems become older, it becomes more difficult to source parts and maintenance. By waiting to upgrade an existing control system, a plant may save money in the short term, but is setting itself up to ultimately pay more in the long term. Obsolescence concerns also create the possibility that in the future, an HMI or other existing control system won’t have the capabilities to upgrade.
Downtime
Maximizing uptime is an ever present concern for process manufacturers. Outdated control systems may take longer to start and restart while also operating slower when operational. This extra downtime spent waiting is time that could be spent in production. Over time, this downtime adds up. Are you wasting time that could otherwise be spent focusing on quality and efficiency of production?
Control Upgrade vs. Full Replacement
Often, an older control system may just need an upgrade to perform like a newer one. However, when obsolescence concerns begin creeping up, an upgrade may not be all that’s required. At what point does a control system replacement become necessary?
With many older DCS or PLC systems, an upgrade can be almost indistinguishable from a new system install. If your hardware is sound, it may just be your software that needs an overhaul. Or maybe you have a model from a trusted brand, it’s just not the most recent model.
The first step in the process of optimizing your control systems is to determine what your needs are and how your control system isn’t meeting them. And often the best option is the system upgrade.
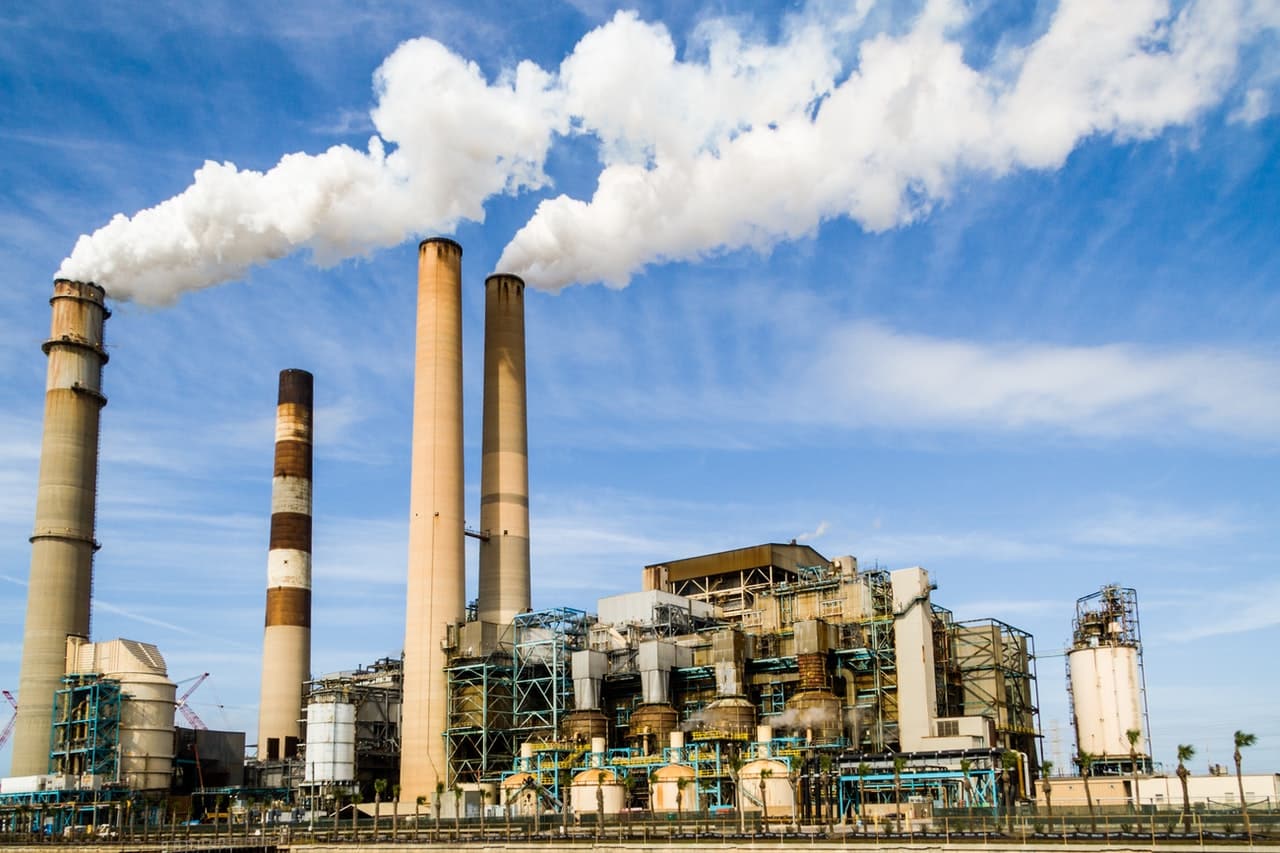
Certifications
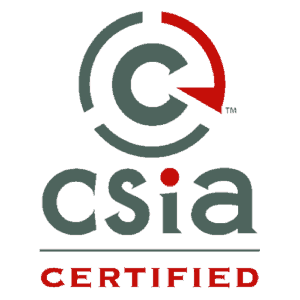
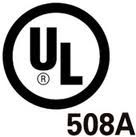
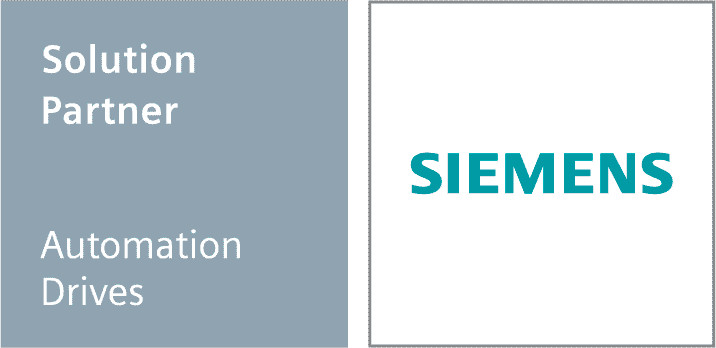
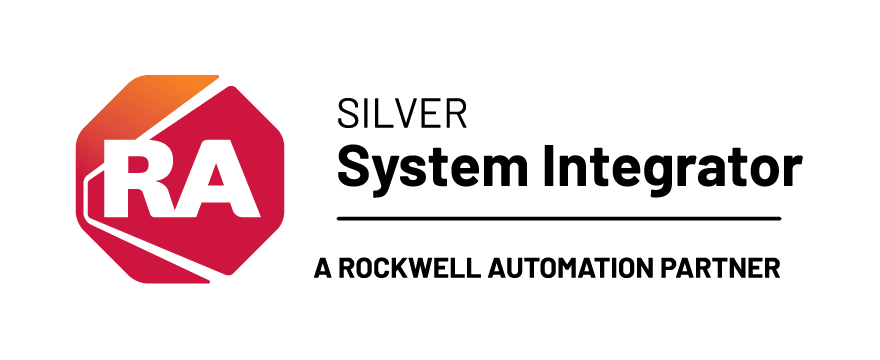
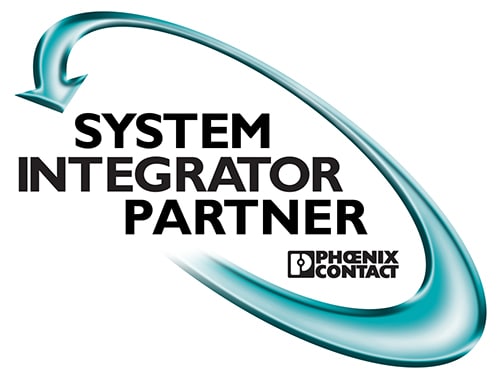
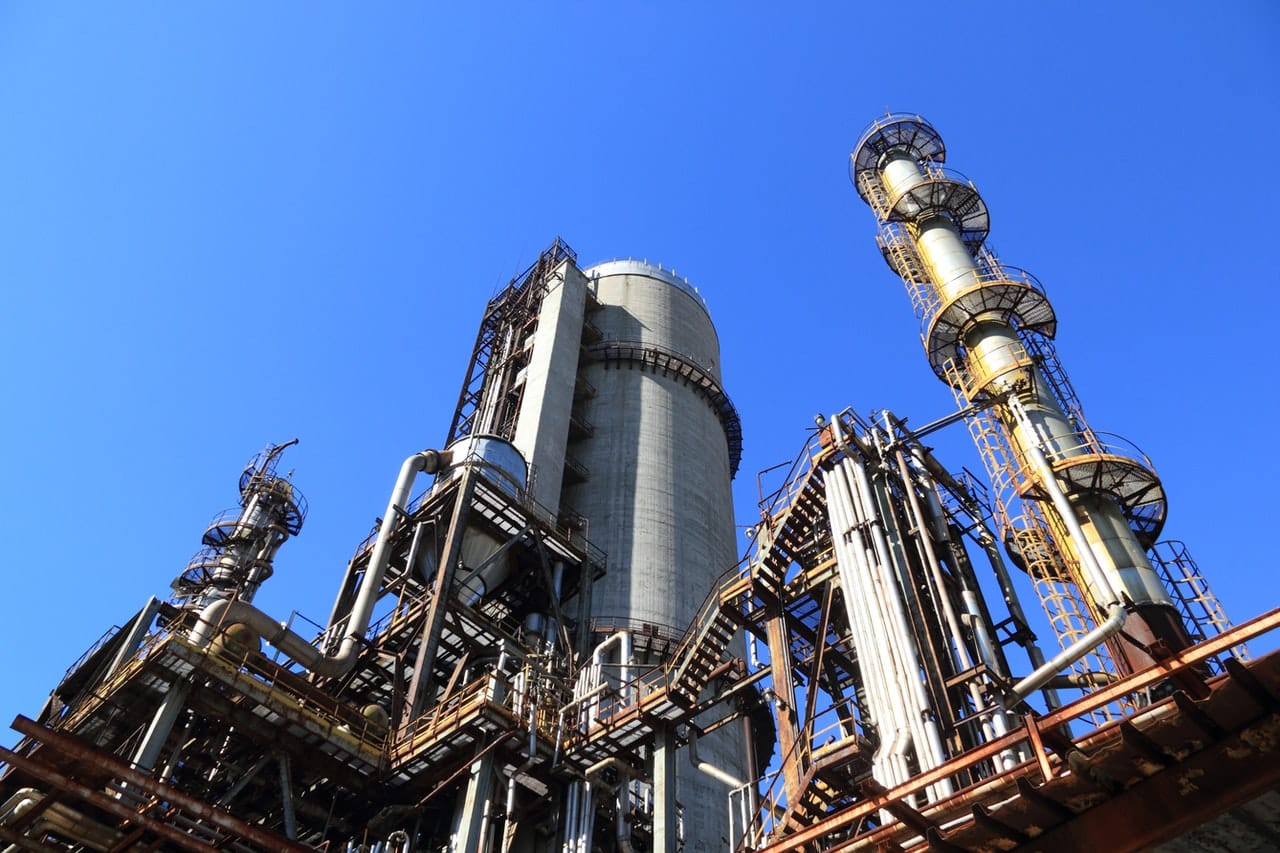
Why Upgrade Your Control System Now?
As industrial manufacturing continues to evolve, process plants are having to make changes to keep up with the demanding climate. Plants that are operating with decades-old technology or poorly performing systems are getting left behind.
There’s also the question of what opportunities have been missed or problems glanced over due to an outdated control system. Not utilizing the latest control system technology can prevent improvements in process performance and lead to declines in operator effectiveness.
An expert control systems upgrade is not only good for reliability and quality, but also for increasing plant flexibility. Being able to meet (or exceed) the needs of today’s consumers is a valuable asset for any process plant.
Why Cross Control System Upgrades?
At Cross Company Process Solutions, we consistently provide world-class support for process manufacturers and applications across various sectors, including industrial, commercial, and municipal. Our commitment to excellence is underpinned by a wealth of experience that spans decades, allowing us to navigate the intricacies of even the most complex projects and provide comprehensive solutions designed specifically for them.
Our industry-leading technical knowledge sets Cross apart in the field, enabling us to craft solutions that aren’t just cutting edge, but also tailored to the unique needs of each customer. This, coupled with our world-class customer support, is what truly sets Cross apart.
When you work with Cross Company, you’re not just getting a comprehensive solution for your process application. We aim to build lasting partnerships, working by your side as an extension of your own team. When you choose Cross Company Process Solutions, you’re not just choosing a service provider; you’re choosing a trusted ally on your journey to process excellence.
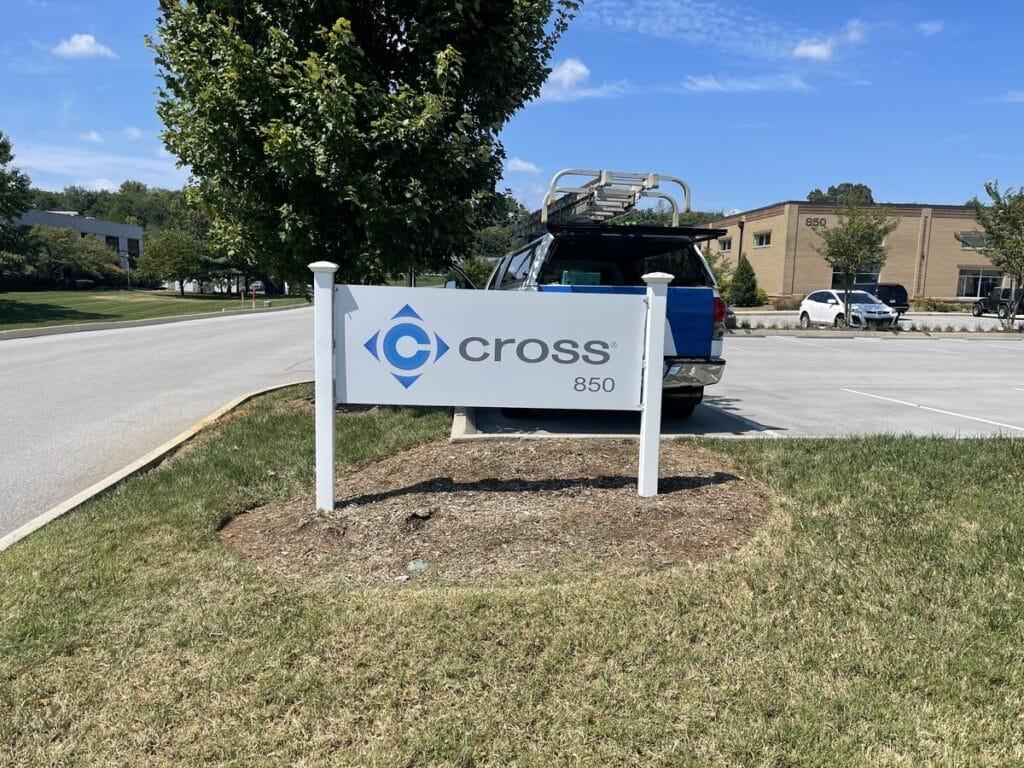
Related Solutions for Process Applications
At Cross, we offer much more than just control system upgrades. We can also provide the solutions our process manufacturing partners need to succeed. Check out our other process solutions equipment and see for yourself.