Offering a range of automation solutions for the industrial world.
Automating Manual Processes
Whether you are dealing with staffing shortages or simply want to utilize your human labor for higher value tasks elsewhere in your facility, automation is a great solution. Our specialties include packaging and material handling, machine tending, testing and quality, and automated measurement.
Automation for Machine Builders
As a machine builder you are constantly working to improve your product. Our team of experts can help you with the automation components and sub assemblies. We offer a wide range of automation components including actuators, servo and stepper motors, gantries, pneumatic valves, end of arm tools, HMIs, and more.
Service and Support
Maximize your investment with our service and support services. Our team of experts can help with Custom Automation Solutions and Sub Assemblies, Cable Management, Repair and Refurbishment, Training, and more. See how our expertise can add value to your operation.
Resources from Our Automation Experts
Our automation experts make us more than just a distributor of automation solutions. At Cross, our automation team works on a range of projects and have accumulated a wealth of knowledge from real world experience, knowledge to help our customers succeed. Take a look at the latest articles, technical guides, and case studies from our automation team.
The reasons for automating manual processes are well known at this point. For tasks that are the 4D’s – dull, dirty, dangerous or difficult to fill – a robot or...
Why choose Cross Automation as your Integration Partner? When looking for a manufacturing automation integration partner, we know you have a lot of choices. So why partner with Cross? Speed...
Manufacturing automation experts partnering with you to develop innovative solutions backed by world-class customer service.
What Customers Are Saying
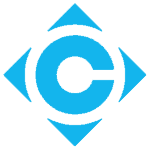

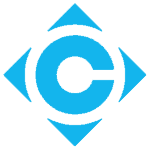

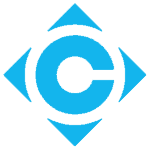

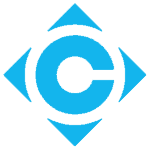

A3 Member Since 2010
Cross Company is a member of A3, North America’s largest automation trade association. A3 represents more than 1,300 organizations involved in robotics, artificial intelligence, machine vision & imaging, motion control & motors and related automation technologies. Learn more about A3.
News, Events, Supplier Updates
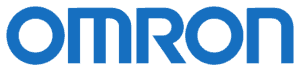
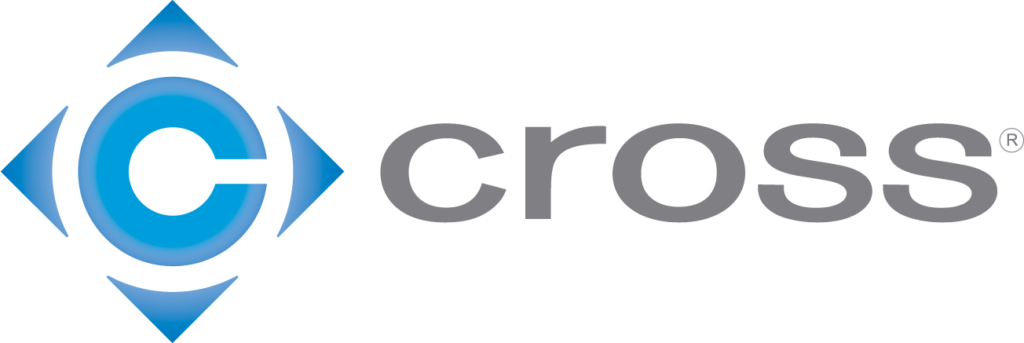
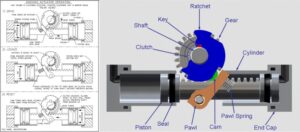
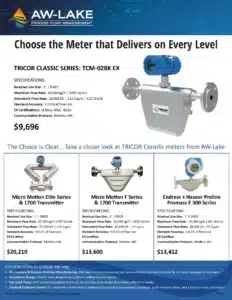
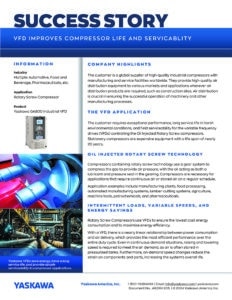
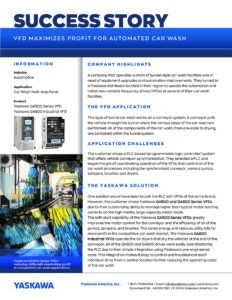
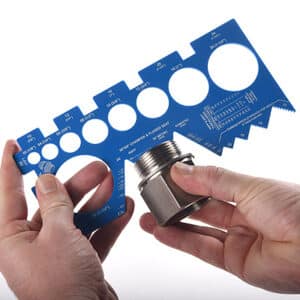
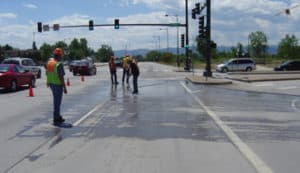
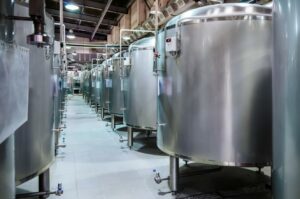
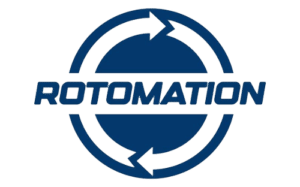
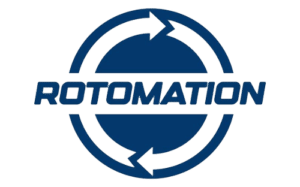
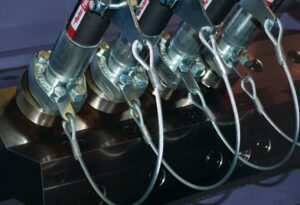
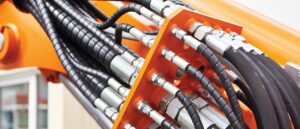
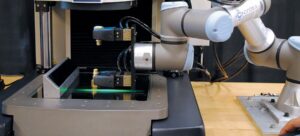
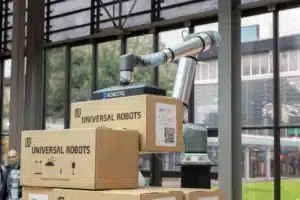
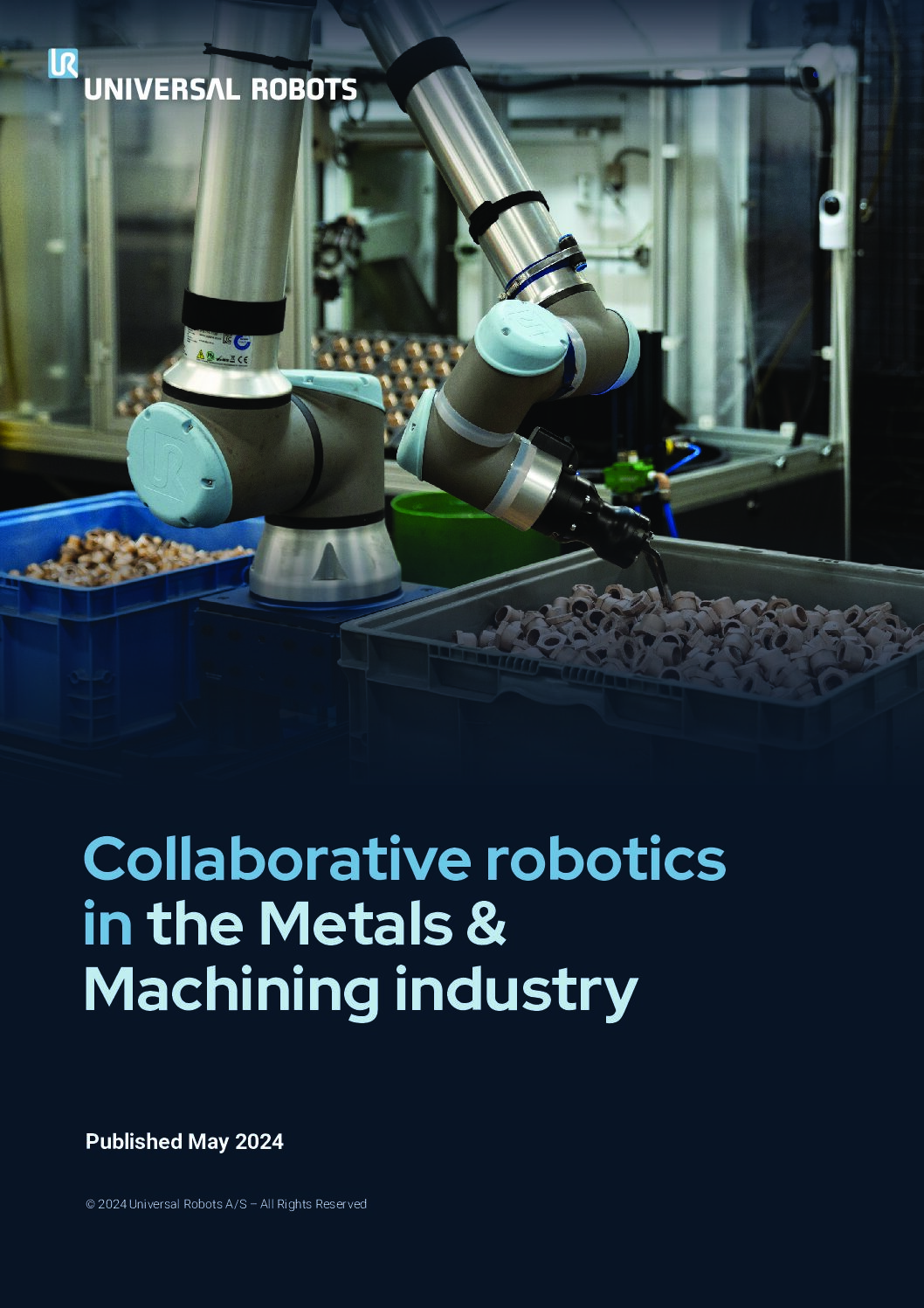
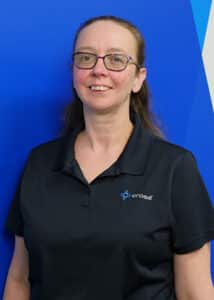
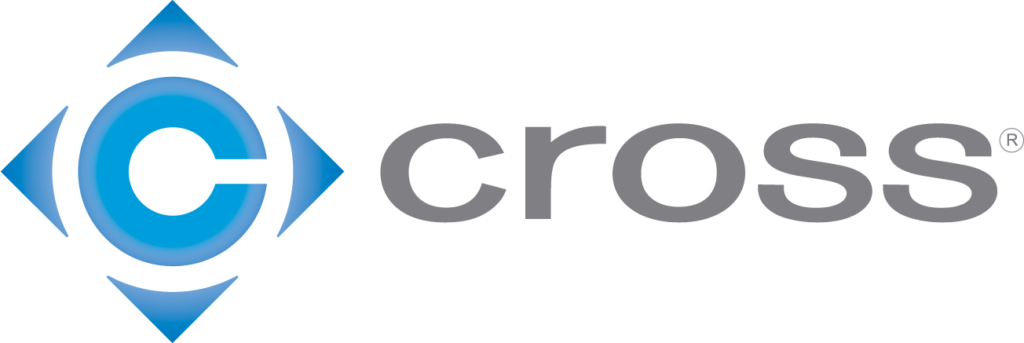
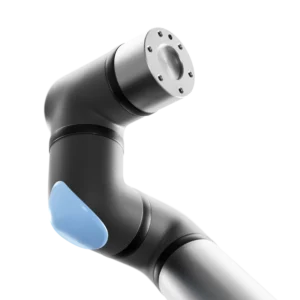
Is Automation Right for Your Process?
Answer a few simple questions and find out! We’ll send a copy of your inputs to help build the case for automation, and determine ROI for automating parts of your operation.
Integrating Solutions from Industry Leading Brands
Our team works with an industry leading number of suppliers when developing solutions for our customers, so we can integrate the right components every time. Our expertise, paired with access to a wider range of materials, means we can build the best solution for your process.