Universal Robots
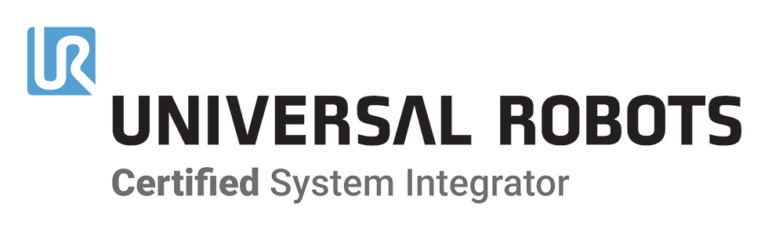
Universal Robots is the leading manufacturer of collaborative robots, providing thousands of robots throughout many industries worldwide. As a certified systems integrator for Universal Robots, our automation team works with customers in a range of industries, creating customized solutions that utilize Universal Robots products.
Featured Universal Robots Products
Certified System Integrator
The automation group at Cross Company is a certified system integrator for Universal Robots. Our automation team works with a variety of customers in a range of industries to develop automated solutions with the latest Universal Robots equipment.
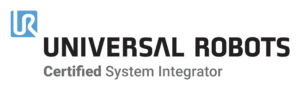
Available In The Following Areas
Our automation team is based in North Carolina, but our physical footprint includes locations and team members in the following areas, so we’re always close!
Industries
Fiber Optic Cable Manufacturing
Textiles
Resources
Downloads
Videos
Additional Materials
More information From Universal Robots
Interested in learning more? Contact a Cross team member today to discuss your application and see how we can help your operation!
Latest Universal Robots Resources, News, and Events
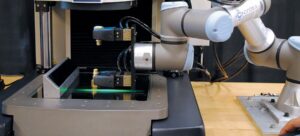
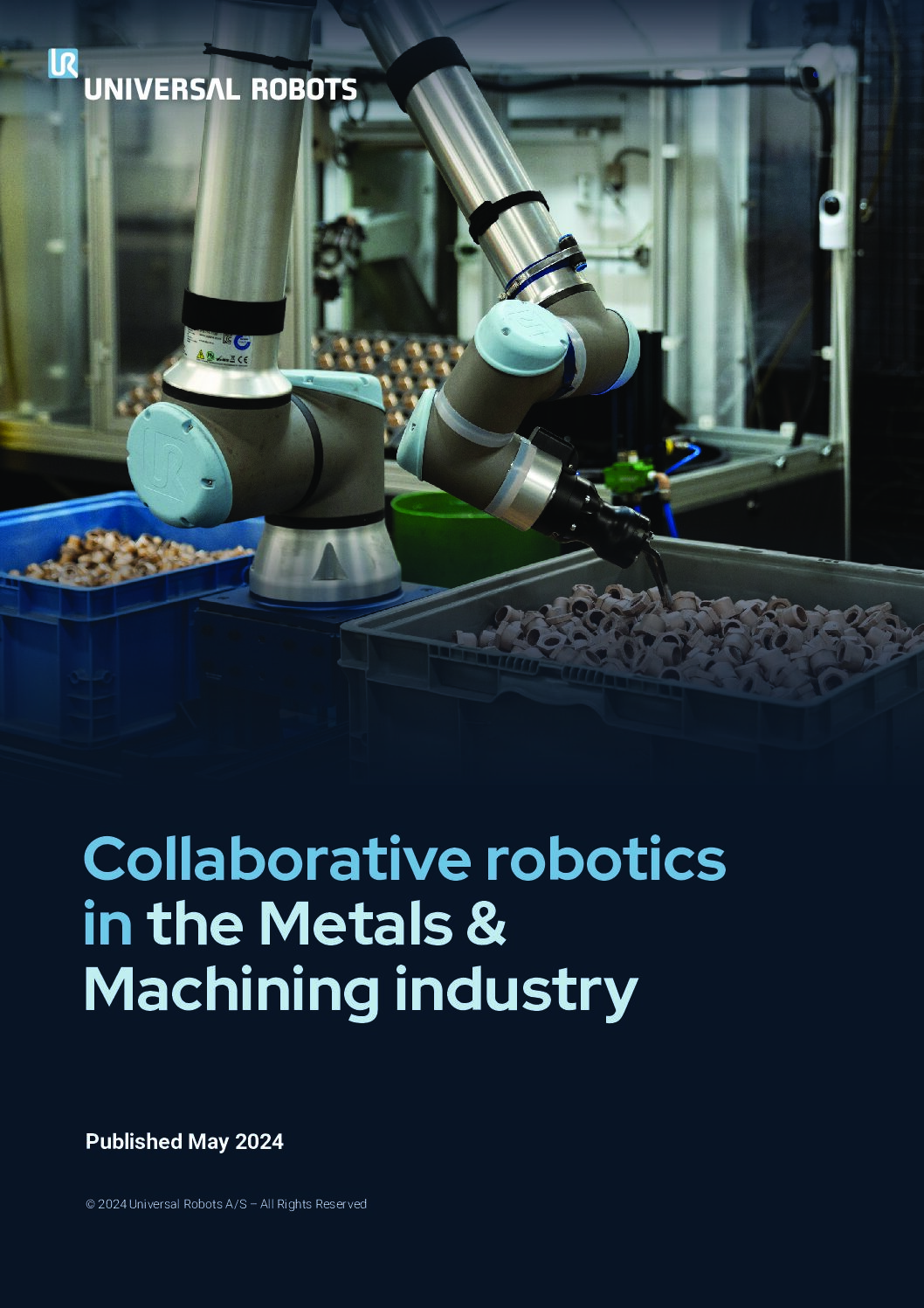