Case Study: Cross Helps Kemira Convert Reactors to New Product Line
Cross Helps Kemira Convert Reactors to New Product Line
Cross Process Solutions concluded a seven year project with the Kemira plant in Columbus, GA to upgrade their legacy APACS system to Siemens PCS7 with Simatic Batch in the summer of 2023. To minimize downtime, the migration was executed in twelve phases to allow Kemira to fulfill customer orders. In addition to migration from a legacy system Cross also implemented Simatic Batch to allow for overall batch management tools such as recipe, production scheduling, and raw material management. The execution process was honed to perfection and Kemira was able to meet all production obligations during the entire migration process.
In the fall of 2023, Kemira decided to convert two of their six PA/PAE reactors to EPAM in order to better align with market demand. Mark Francois, Production Supervisor and lead for the facility’s distributed control system, said choosing Cross for this conversion was an easy decision because of “the overall success of the APACS to PCS7 conversion project”. He went on to say “we wanted to stick with the people (Cross) who had been there since the beginning and always had great results.”
The conversion from PA/PAE to EPAM was complex because Kemira wanted to retain the ability to run both products in the reactor. This required a sophisticated system of interlocks as the two processes required different raw materials and have very different reaction characteristics. In order to maintain the dual use capability, the interlocks around the PA/PAE tanks had to be masked so they wouldn’t interact when processing the EPAM materials. Masking process interlocks plays a crucial role in ensuring the safe and efficient operations of the automation system by controlling the timing, sequencing, and conditions under which the various processes can occur. The software tools inside of Simatic PCS7 Advanced Process Library (APL) provided standard functions that allowed for this configuration without having to customize a solution.
Process interlocks can consist of various forms. In this case, they were designed to not only prevent hazardous situations, by ensuring that safety conditions are met before proceeding, but also control the product quality. These functions were implemented through software logic to enforce specific process constraints without impacting the batch cycle time.
Kemira requested to expedite the project in order to meet strategic objectives for the company, with a goal to complete the conversion by the end of 2023. Due to the complexity, Cross’s original proposal projected completion in April 2024. In order to meet Kemira’s time requirements, the team at Cross added an additional engineer to the project team and put in extensive overtime to complete the conversion three months faster, finishing at the end of January 2024.
Cross was able to help Kemira to improve efficiency by maintaining the dual use capability of their process and completing the project quickly. Additionally, by configuring the complex system of interlocks needed to keep the products separate, Cross reduced the risk of cross contamination and wasted raw materials.
When asked about his experience working with Cross on this project, Mark said, “As always, it’s a walk in the park. They help us make the right choices and give us options we might not even be aware of. They are always there for us when needed. There is no time of day or night that they aren’t available to help.” He went on to say that he would recommend Cross to a friend or colleague commenting, “our experience is everything. They’ve always made it easy and helped us through a lot of decision making. They’ve guided us down the right path time and time again. Cross delivers and they deliver consistently.”
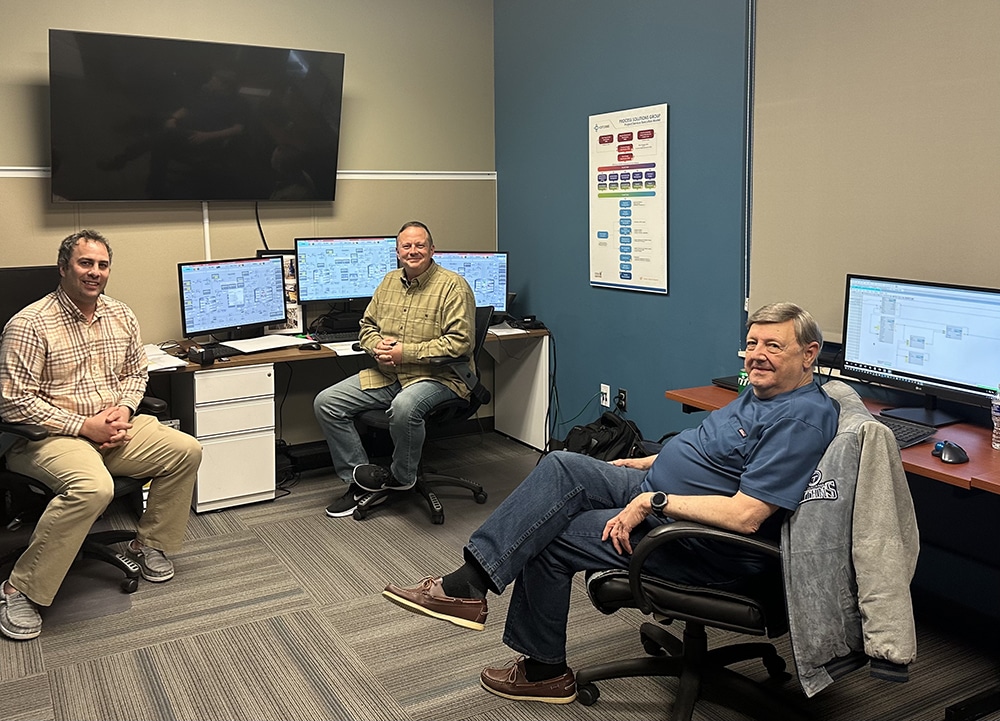
See how our process solutions team can help improve quality, increase efficiency, and reduce risk.
Latest Case Studies And Application Notes
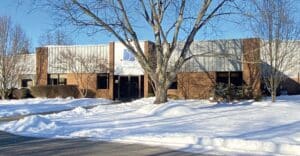
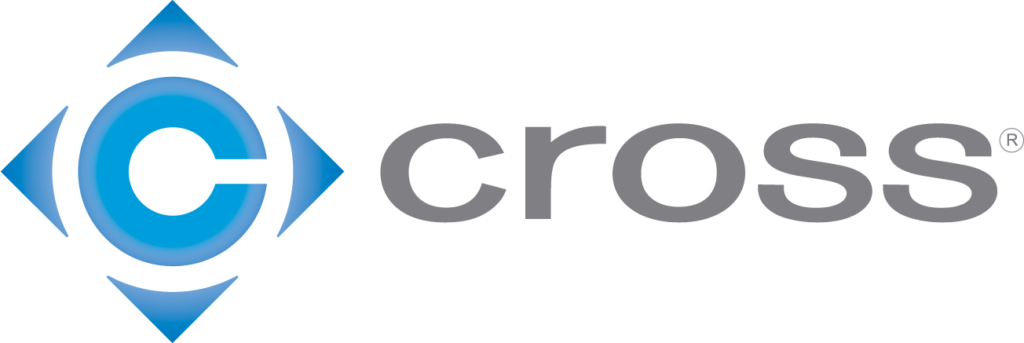
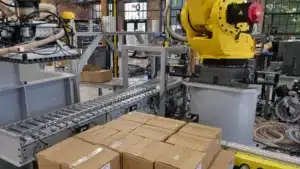
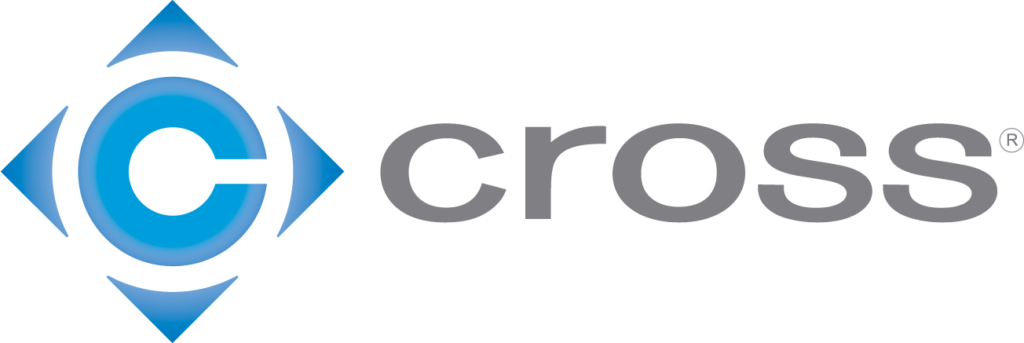
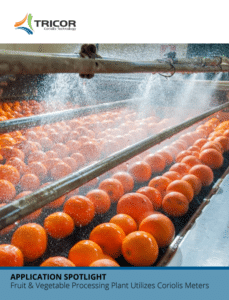
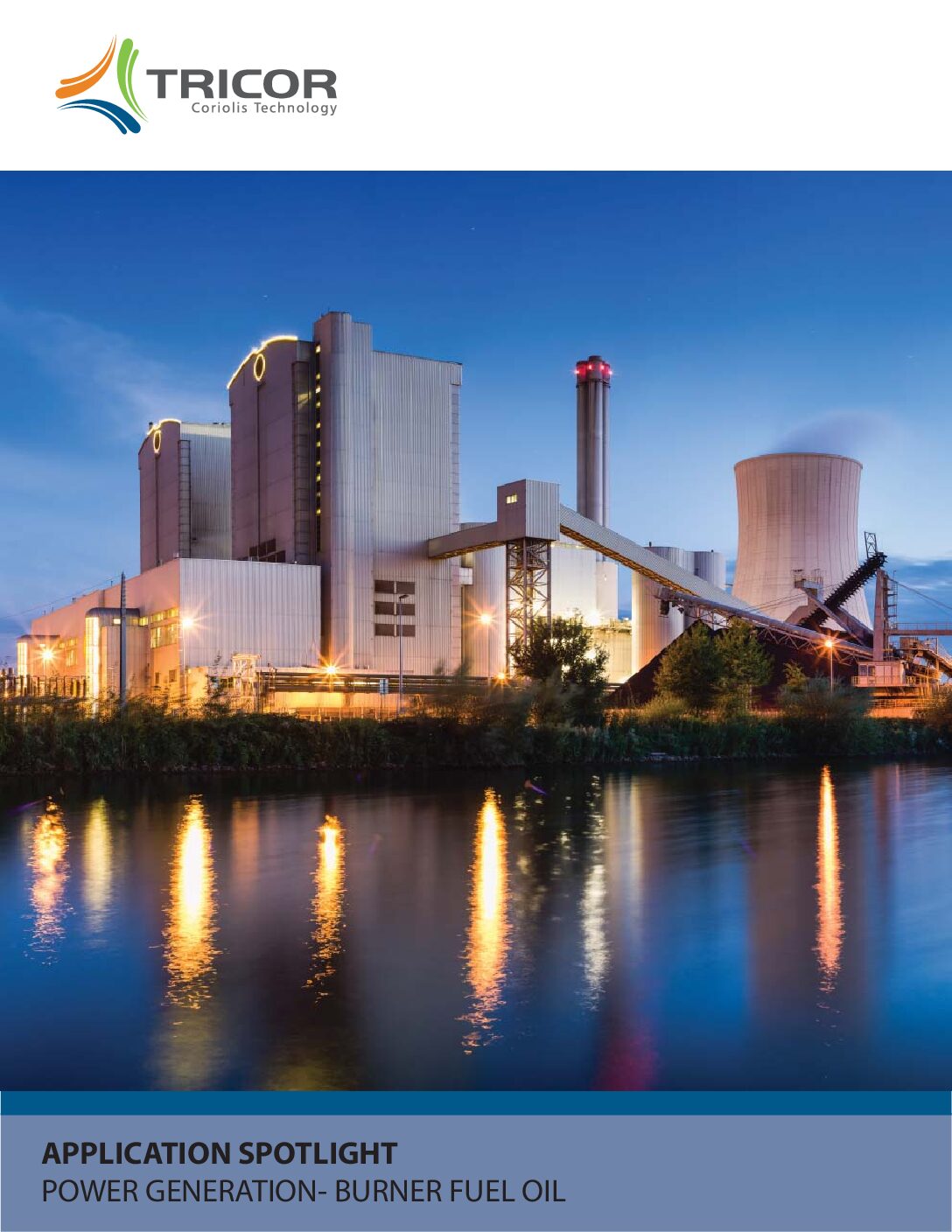
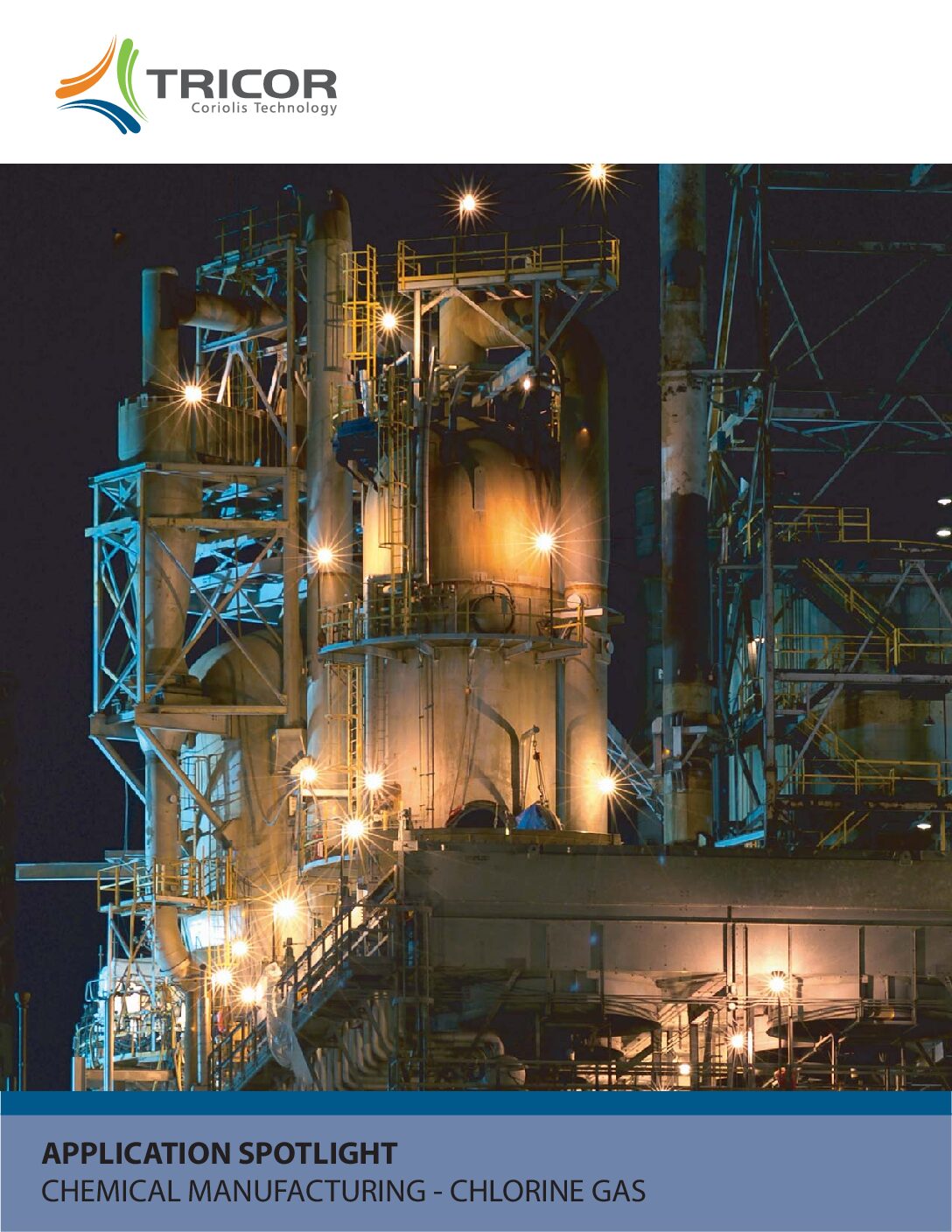
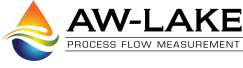