Industrial robotics typically come in four main types: Delta, SCARA, Cartesian, and robotic arms with 3-7 joints. These have become the standard for the industrial robot market because almost every application can be solved with one of these types.
As the demand for industrial robots grows, the type and complexity of applications being solved also grows. The question is, what happens when an application calls for features or abilities that standard off-the-shelf industrial robots can’t tackle, thus requiring a custom robotic solution?
Because robotic software and controls tend to be the most complicated part of a custom robotic solution, this used to mean finding a resource with a Ph.D. in robotics to design a new robot for the application, but this no longer holds true. As an example, take an application that calls for a 3-armed Delta robot requiring a reach longer than anything available commercially. Here is how a custom solution can be built without having a deep knowledge of kinematics or robotics.
Step 1 – Selecting the Omron NJ501-4XXX Robotic Control Technology
The Omron NJ CPU unit is the latest in a long line of multi-generation control platforms from Omron. The NJ501-4XXX introduces the addition of Robot Control Technology. This technology, coupled with the Omron G5 or 1S servomotors and drives, creates the ability to build robots without having to program all of the low-level details and kinematics.
For this application, arms large enough to cover the desired work area, along with motors sized large enough to handle the desired load, are specified and selected from the Omron 1S family of servomotors and as well as the associated 1S drive, brake, and absolute encoder.
An Omron NJ501-4500 CPU unit is selected, allowing for the control of 64 motion axes and up to 8 robots.
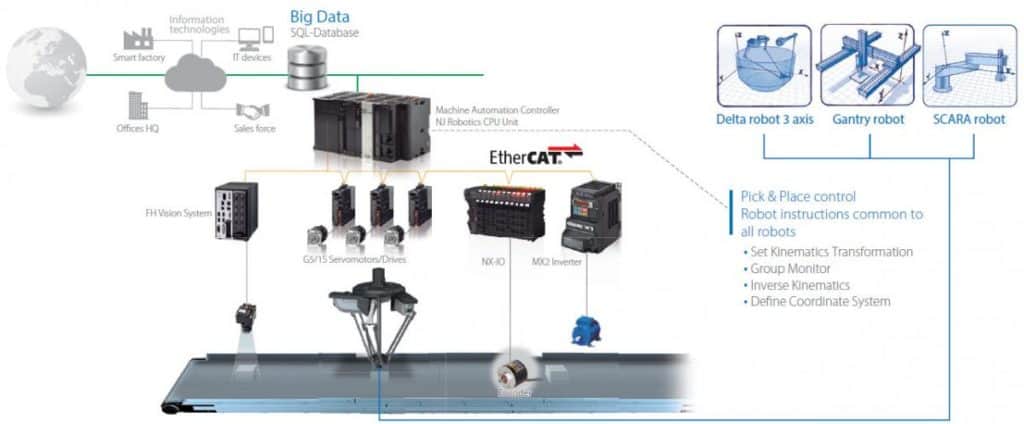
Step 2 – Programming the NJ501
With robotics, programming is typically the challenging part, requiring a unique set of skills and knowledge of robotics. Coordinating the motion of a Delta robot requires a deep understanding of kinematics and how the various parts must move together to achieve the desired motion at the tool or end effector.
The NJ Robotics CPU comes standard with the ability to do the low-level controls and will control the following instructions:
- Kinematics Transformation
- Inverse Kinematics
- Coordinate System Definition
- Group Monitor
(Communication cycle for robot control is 1 ms or less over EtherCAT)
All of this is programmed and integrated into the same environment and same language that current PLC programmers are used to working in. The same Sysmac Studio software used for sensors and motion control is used for the robotics and IEC 61131-3 instructions. The same instructions that can be used for motion control are also used for the robotic control.
All of the specifications of the robot are entered In Sysmac Studio. This includes arm length, the distance between motors, the configuration of motors, workspace coordinates etc. There is even a section for conveyer tracking if the application calls for multi-axes coordinated control.
Then the standard IEC-61131-3 language is used to program the moves and functions the robot is going to perform. The specific robot moves are achieved through robot control function blocks.
Step 3 – Testing and Simulation
Now that the robot has been programmed in Sysmac Studio, it is usually a good idea to simulate the moves before using actual hardware. These methods can also be used to accelerate development time:
- A single window to adjust motor parameters and view how it affects other axes.
- Synchronization between robots.
- Visualization and data tracking of machine motion data.
- Simulated movements of the Delta 3 and 3R can be done based on real vision data.
- Simultaneous tuning when using the 1S drives and motors.
- The 5-step process to incorporate vision into the robot, including simulation.
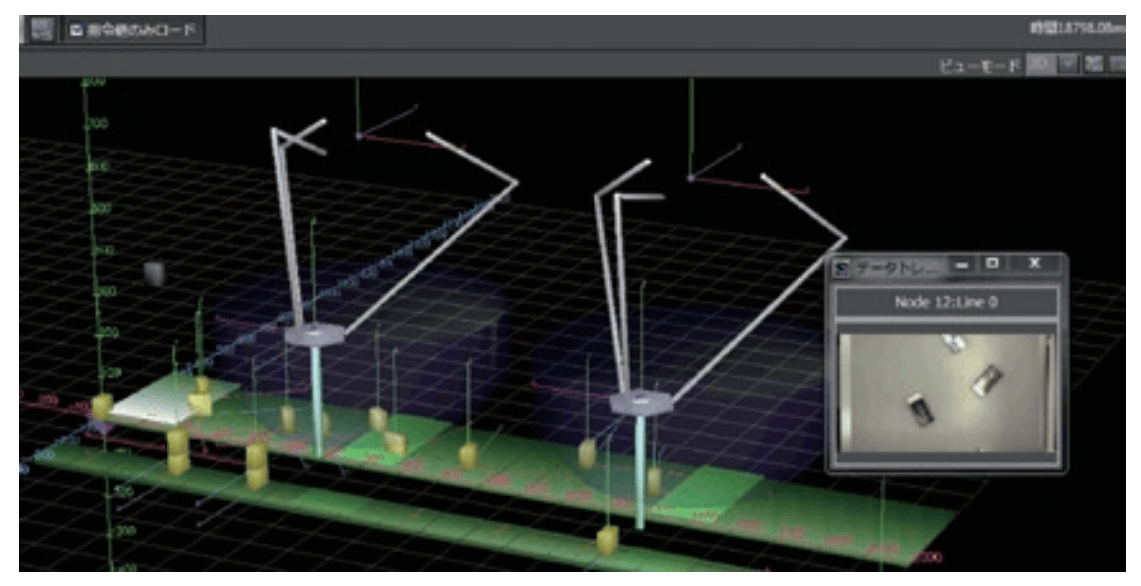
Machine movement can be simulated based on measurement results of vision systems.
By using the integrated simulation, it is possible to visually see how the robot will move and act without having any hardware. This makes it much easier to test and troubleshoot code as well as get started with development before the actual robot has been built.
Step 4 – Integration with the Rest of the World
A lot of industrial robotic applications still use other items such as safety I/O, motion, and various types of sensors. The NJ501-4XXX is capable of integrating all of these other items (including vision) along with the robotics into one system controlled using an EtherCAT network. A single controller can connect up to 64 axes of motion, up to 8 robots, and up to 2,560 points of I/O.
Omron also has a wide range of features to bring a vision system into Sysmac Studio and robotics. These include:
- Simulating inspection and measurement.
- Import pictures into Sysmac Studio Wizard.
- Easy tuning to calibrate the simulated robot to the real world robot to minimize any error between the two.
In four easy steps, it was possible to create and program a custom robotic solution without any prior knowledge of low-level kinematics by handling all of this in the Omron software. Omron Adept has a wide range of industrial robot offerings including SCARA and 3 or 4-arm Delta robots. Anytime one of these robots will meet application needs, the cost of integration and time to market is almost always much lower with an off the shelf solution. However, when an off the shelf solution doesn’t get the job done, the Robot Controller from Omron has the horsepower and features to simplify custom robot system design, programming, and implementation.