Application Note: Cross Air Flow Monitor
Automotive parts manufacturer finds quick ROI with Cross Air Flow Monitor
Actively monitoring compressed air consumption can have benefits for your bottom line. One of our customers, a manufacturer of automotive parts, found significant savings after just a few months. They used the Cross Compressed Air Flow Monitor to record the amount of air being used by their cabinet cooler. This device utilizes compressed air to cool an electronics cabinet. Because it is exhausting to the atmosphere to cool the cabinet, any extra air used in the process is wasted. For this reason, they wanted to see if they could accomplish the same task while using less air.
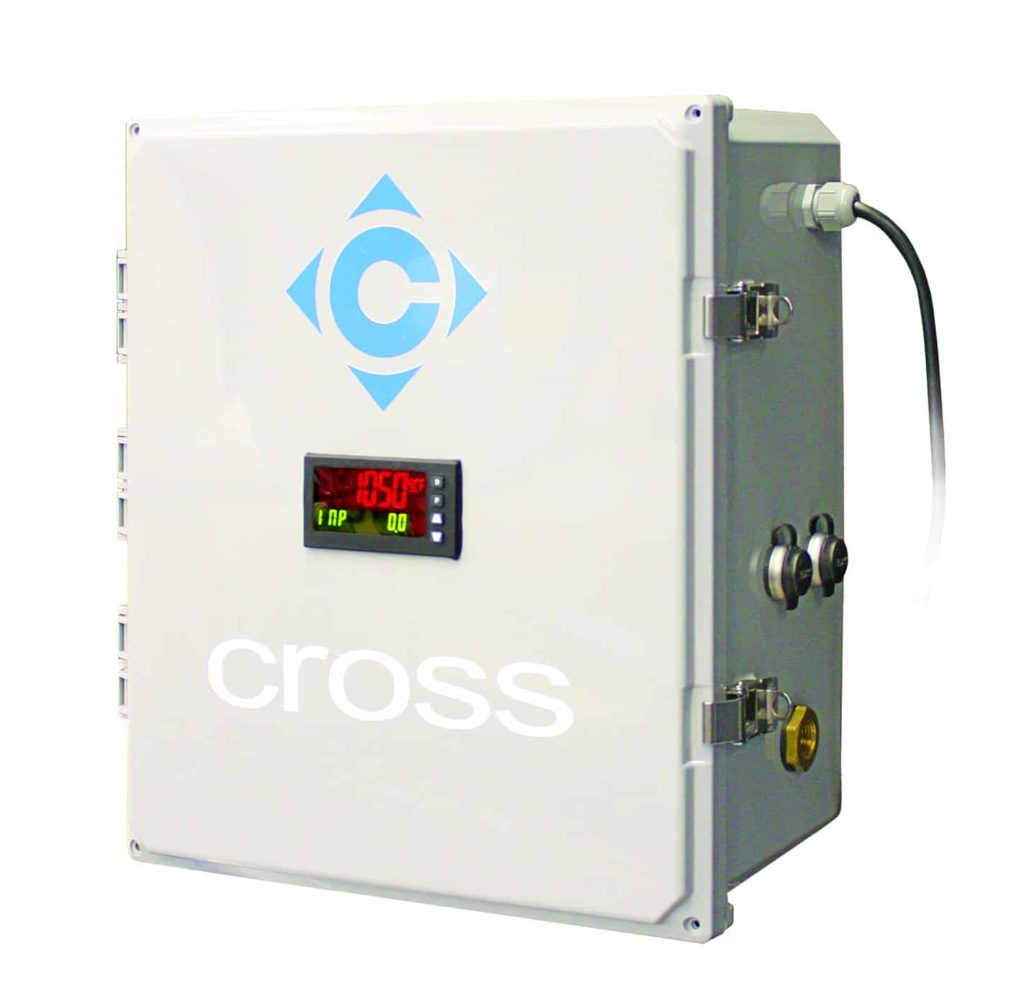
To begin, they measured their baseline air consumption which was found to be 33 SCFM at 90 PSI. Because they are using the air to control temperature, they monitored the temperature while reducing the PSI. The customer found that by using only 20 PSI they could maintain 10 SCFM which still keep the cabinet at an acceptable temperature. For this particular customer, it costs around $0.28 to produce 1000 cubic feet of air. They found that over the course of a year utilizing the Cross Air Flow Monitor will save them nearly $4,000 on this single piece of equipment. Other customers have reported prices ranging from $0.25 to $0.50 per 1000 cubic feet, so it is easy to see how the cost savings can quickly add up.
Are you Interested in discussing your project? Learn more about our Compressed Air flow Monitor and contact a Cross team member to discuss implementing a solution like this for your operation!