How Wireless Data Collection Works in Measurement Tools
The need to get information around an obstacle has been ever-present in our lives. Think about times of trying to have a private conversation with your high school sweetheart away from your nosey siblings, only to be shackled by a corded phone. At some point, a person was so desperate that they tied a message to a pigeon and threw both to the sky, along with a prayer that it would reach its recipient. Technology has evolved continuously and rapidly to alleviate the pain of this persistent problem.
In manufacturing, it is as important as ever to ensure that data is sent safely, accurately, and efficiently. Despite this need, manual and physical data entry is still a common pain point in operations around the world. While some hardwired solutions are effective, many inhibit mobility, and they can be costly, complex, and fragile. So many applications desperately need the benefit of wireless data transfer, and we are the people to help with that need.
How it works:
A long list of our customers, when asked about wireless data, challenge the idea with “I need it to go into my software,” or “I’ve looked at it before, but it was expensive and complex.” We often greet that challenge the following: “Let’s address how your data can be sent wirelessly and perhaps you’ll see that it’s easier to implement and utilize while being less expensive than you thought!” To address specific needs, we break the solution down into the following:
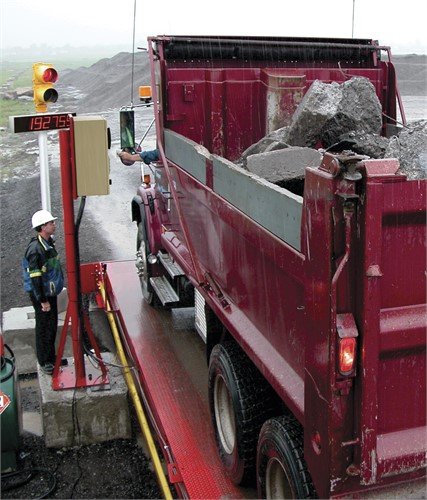
Transmission:
Communication from an instrument to a PC, PLC, or other device requires some form of transmitter and receiver. The type of transmitter and receiver are dependent upon the data format needed, range, and environment. For example, if you were looking to setup a gaging station in a lean manufacturing cell, you would not need the data to transfer far. However, transmission would need to occur in real time and not risk accidentally connecting to other devices in the area. In this instance, technologies such as Bluetooth and ANT + are excellent options. They are easy to setup, low cost, and compatible with virtually any PC or tablet. Conversely, an operator using a torque wrench to perform an audit in an automotive assembly plant or a truck driver on a scale would need more range. In these instances, Radio Frequency (RF) or WiFi are better suited.
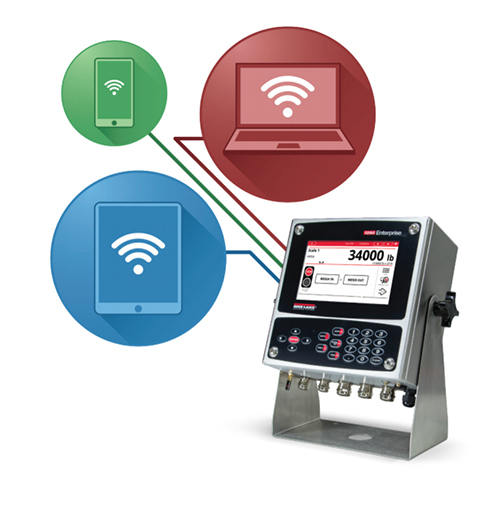
Rice Lake’s 1280 Indicator
Drilling down to the instrument itself, the transmitter must be compatible with the unit’s data output port. Many dimensional gages have a “data port” which is intended to be mated with a manufacturer supplied cable. These ensure the appropriate stream of data to the type of measurement that the gage must take. Other instruments have generic serial ports, like RS232 or RS485 output, for peripheral communication to devices like PCs or Printers. The list goes on with protocols such as Ethernet, Analog Output, I/O, and USB. Some manufacturers offer wireless data transmitters readily compatible for these instruments. For example, MSI Rice Lake’s TranSend™ readily plugs into theirs and others’ load cells and indicators to facility wireless weighing.
In other instances where the OEM does not have a ready solution, third party companies offer wireless capability for your beloved measurement device. MicroRidge, for example, offers solutions for thousands of different metrology instruments regardless of type, brand, or data output.
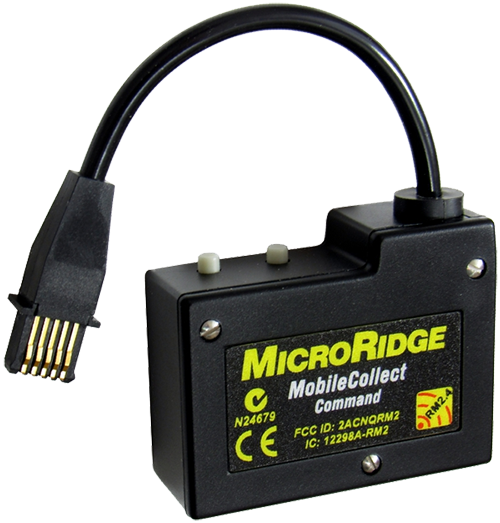
MicroRidge Transmitter
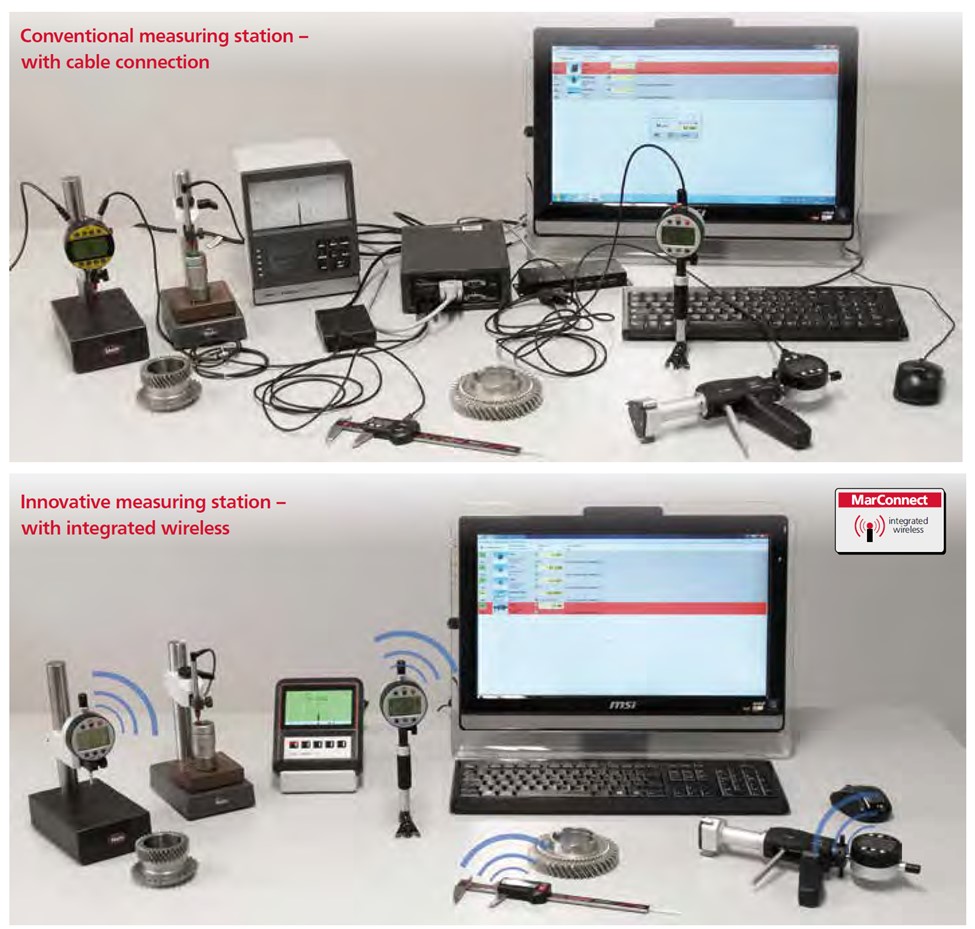
Mahr’s integrated wireless technology
Mahr’s integrated wireless technology
Going further, metrology manufacturers are developing instruments with wireless data transmission built into the device. Mahr’s integrated wireless product line is designed to specifically provide reliable, real-time data transfer while being cost effective and eliminating disruption to the operator’s use of the gage via bypassing an external transmitter. This is not limited to dimensional gages; Starrett handheld force gages come standard with Bluetooth and Tohnichi offers a comprehensive line of wrenches with BlueTooth, RF, and WiFi. These are only a small sample of a large line of options based on customers’ applications.
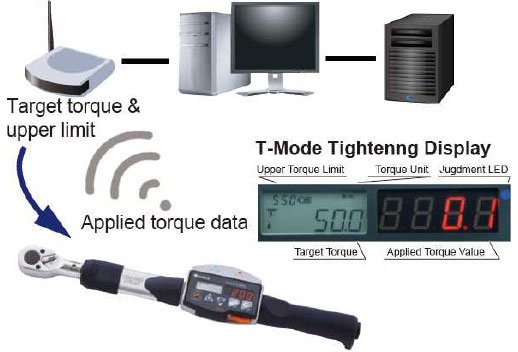
Tohnichi CEM-WF Torque Wrench
Receiver:
Now that your measurement device has a transmitter and sends data out, it needs to be directed to its destination. The first thing to consider is the following: where is the data going into? Are you sending data into a PC, a PLC, another measurement instrument, etc.? This determines not only the type of receiver, but also its configuration.
On the one hand, if you are using an instrument with Bluetooth and are sending data to a PC, you can likely get by with a simple dongle or even use the PC’s Bluetooth feature in some instances. On the other hand, if you are sending something via Ethernet, you may need a bridge setup and the transmitter and receiver with a clear line of sight.
Finally, once the data is received into the hardware, it must be formatted and directed into its desired destination and outline. This can be achieved through numerous methods including software and drivers. For many applications, a simple keyboard input, where the value from the instrument is input directly to where the cursor is active in a PC, will suffice. Other instances can be more complex. For example, you may want to record the time and date of the measurement or record a stream of measurements at a specified frequency. Many users will want to ensure that only specific instruments at a gaging station are used for specific features. In this scenario, setups like a Virtual Com Port allow instruments to be assigned identifiers or channels so that they only send their data to certain fields.
Data Collection to Data Analysis:
While the topic of Data Analysis is another topic within itself, it is important to discuss the hand off between data collection by an instrument and data analysis at a higher level.
The process for product inspection or data entry has to follow a specific flow in order to provide logical data for it to provide meaningful information to someone that is not at the point of entry. For example, if an operator is measuring a part with dimensional gages, the feature being measured, nominal, and tolerance must be known for the data to indicate whether or not the part is in spec. Furthermore, if routine inspections are scheduled (as they often are), information such as time, date, operator name or ID, drawing number, or tool number may be required to provide relevance and keep track of the work flow.
Depending on the level of complexity needed and scale of your application, a simple Microsoft Excel template with macros may be the solution or a full-blown software package may be required. Off the shelf solutions, like Prolink’s QC-Gage, offer an interface that is fast and easy to setup while providing powerful reporting tools, analysis, and visibility. These packages are vetted, scalable, and cost effective ways of providing valuable insight into your inspection data.
Specific applications, however, require a step further. Earlier, we gave an example of an inspector in a gaging cell of a manufacturing facility. Let’s consider another very common example of a truck driver pulling a shipment of materials across a truck scale. Where before we were looking for an increase in efficiency and a reduction of error, now we are looking for not only those factors, but most importantly prioritizing safety. Drivers leaving their vehicles to input data creates the risk of injury or death. By providing a kiosk interface, the driver can quickly and easily input the data for his delivery or pickup without leaving the vehicle. The challenge is how can this data be recorded where there is both manual input of information relevant to the weight of the goods, along with the weight itself. Along with that challenge, in this instance it is likely that the scale is located far from a PC and the data will need to be transmitted via an indicator with a program. In this instance, custom programming at both the instrument and the receiving PC is likely the best solution.
Benefit:
Now that we’ve covered how wireless data transmission works, let’s review how it can benefit your process. By eliminating the need to input data manually, we have reduced risk to operators in certain instances, boosted proficiency through time saving, and eliminated error from mistakenly inputting incorrect information. Streamlining the data collection process also facilitates large-scale data collection and analysis. From manually combing through hand written reports to seeing data real time at a plant level, the ability to respond more quickly is immediate. Whatever your reason for moving to wireless data transfer, we have an immense range of options available, coupled with over 80 years of industry experience. How can we help?
Want to share or download this article for later reading? Here’s a downloadable PDF copy: Wireless Data Collection – Taking Data Further is Closer Than Ever