Fixed Gas Detection
Cross Company Fixed Gas Detection
Gas detection systems are dedicated to detecting dangerous gas concentrations, triggering alarms and (as far as possible) activating counter-measures before the situation can become a hazard to employees, assets and the environment.
As opposed to portable detection devices, fixed gas detection systems operate continuously 24/7/365 to be ready for any accidental gas release. Their measuring performance cannot be affected by extreme conditions including heat, humidity, electromagnetic disturbances or strong vibration.
At Cross Company Process solution, we can provide you with the fixed gas detection equipment you need for your process facility or other application. Contact one of our experts today to learn more.
Safety In Industrial and Process Applications
The evolving landscape of industries requires proactive means of safeguarding people, equipment, and the environment. For many operations, fixed gas detection equipment are essential tools to achieve that safety. They are able to offer continuous monitoring as well as provide early warnings against hazardous gases.
These systems are designed to consistently monitor the air for the presence of harmful gases that may pose health risks or jeopardize the integrity of facilities. By deploying sensors strategically throughout a facility, these systems provide real-time data about gas concentrations, ensuring prompt response in case of leaks, spills, or other gas-related incidents.
At Cross Company, we strongly believe in the importance of reliable, durable safety systems for process facilities or field applications. That’s why we collaborate with industry-leading manufacturers to always be able to provide the safety equipment our customers need.
Continuous Monitoring
Instant Alerts
Process Optimization
Regulatory Compliance
Asset Preservation
Components Of A Fixed Gas Detection System
Some of the components of a fixed gas detection system include
- Controllers
- Sensors
- Flame detectors
- Toxic gas and oxygen detectors
- Flammable gas detectors
- Ultrasonic leak detectors
Cross is proud to be a platinum channel partner for RKI Instruments. RKI manufactures their own sensors and controllers, so they can tightly control the quality, reliability and accuracy of their product. They are designed for the harshest environments to protect employees, assets and the environment.
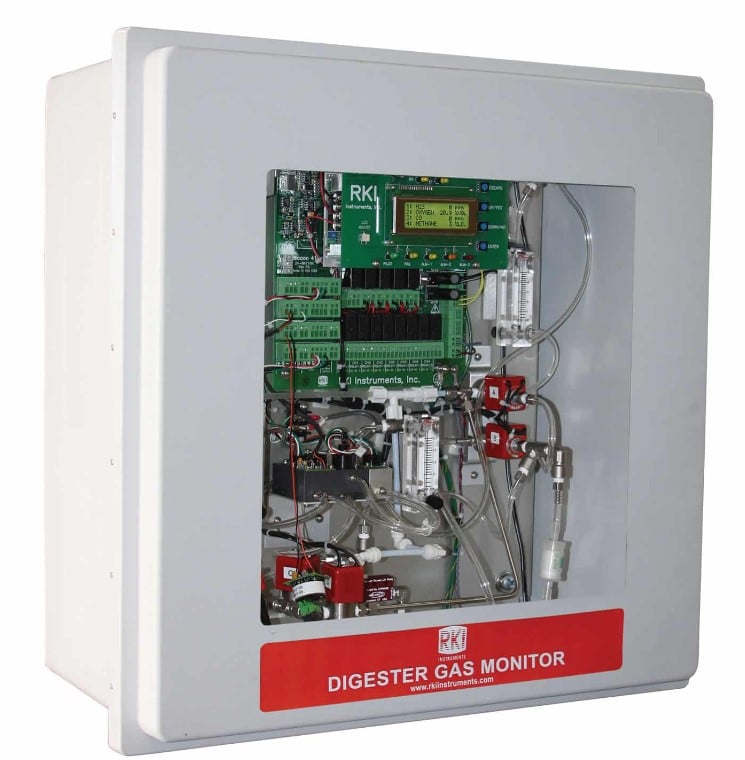
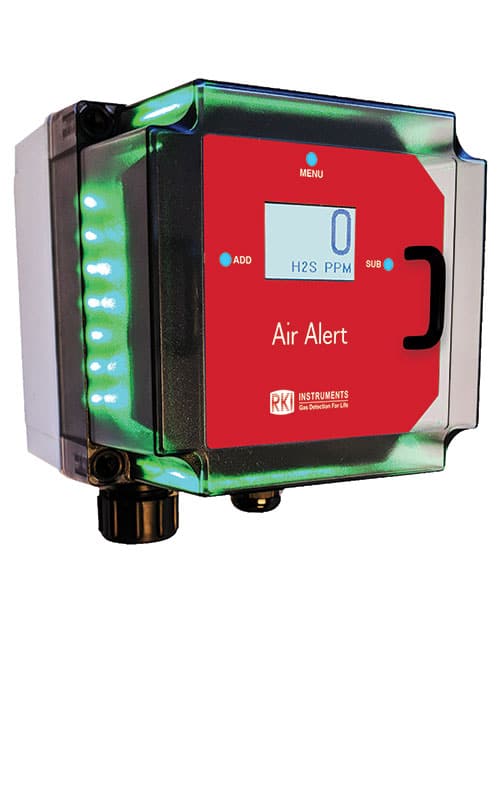
Fixed Gas Detection Features
- Always on and available 24/7/365: May be connected to plant-wide communication (DCS/SCADA) for the fastest response
- No Batteries: Power supply is usually wired and often powered via UPS systems (can be solar powered with battery for remote sites).
- Usually one detector is used for a single gas or gas type (e.g. combustible or chloride);multiple gas hazards usually require multiple gas detectors.
- Calibration is much less frequent than with portable units.
- Only one detector may be necessary in the area of hazardous gas (more units may be required depending on the size of the area, the possible failure mechanisms that could release gas, the gas(es) of interest, etc.)
- A fixed detector can trigger alarms or mitigating actions through discrete or common relays, either locally or plant wide.
- A fixed monitor is useful for detecting combustible gases since it can operate continuously near potential leak sources and the potential ignition sources. A portable unit may not be in the right position or not present when a combustible gas leak occurs.
- Fixed units are also useful in checking for upset conditions releasing toxic gases thus allowing immediate corrective action. With a portable sensor a leak condition could persist indefinitely until an operator arrived in the area wearing the detector.
Why Cross Fixed Gas Detection Devices?
In the world of process facilities and process control applications, safety is a critical consideration. Operations of this nature come with inherent risks and ensuring the well-being of personnel, protection of assets, and ensuring compliance with standards are of utmost importance.
Cross Company Process Solutions is a reliable partner for many operations seeking comprehensive and effective industrial safety solutions. Through strategic partnerships with industry-leading manufacturers, Cross Company provides access to cutting-edge safety technologies that align with the evolving demands of modern industrial operations.
Our combination of industry-leading safety products, exceptional customer service, and technical expertise positions Cross Company as a trusted partner of industrial safety. By working with Cross, you can work to prioritize safety, promote compliance, and provide tangible value to your operation.
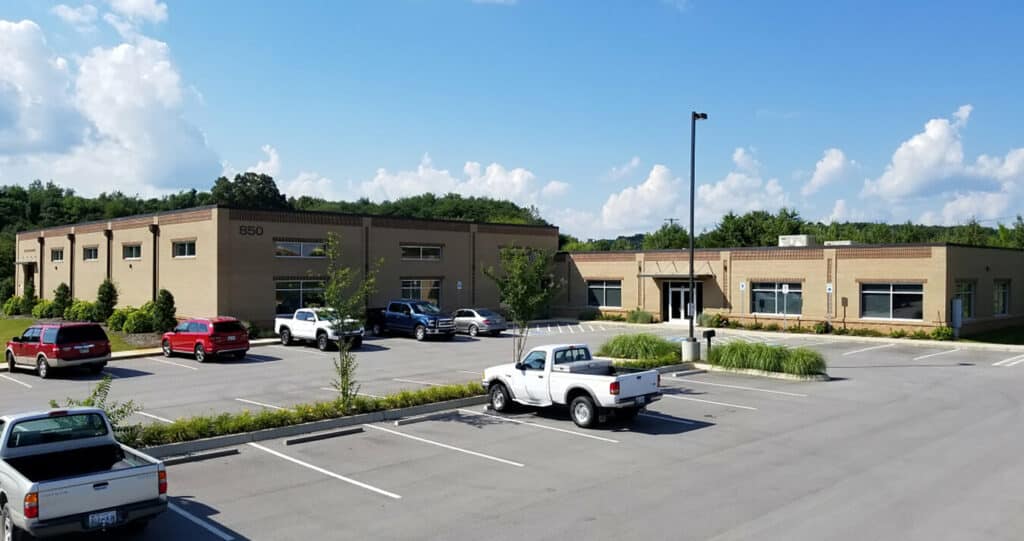
Related Gas Detection Equipment
At Cross, we offer much more than just fixed gas detection devices. We can also provide the solutions our process manufacturing partners need to succeed. Check out our other process solutions equipment and see for yourself.