The Right Tools are Not Enough – Why Gunsmiths Need to Regularly Calibrate Their Measurement Tools
For any gunsmith, whether amateur or professional, having the right measurement tools is critical. Firearms are designed to exacting tolerances and precise measurements. In order to meet the tight specifications, your machining must be skilled and accurate. To verify this, a range of precision measurement equipment can be used.
The equipment you need obviously varies depending on the work you’re doing. For simple modifications, a precision micrometer and dial calipers may be enough. For full scale design and fabrication, additional equipment like hardness testers, bore gages and torque wrenches may be required. Reloaders and ammunition manufacturers will need linear measuring tools, balances and possibly chronographs.
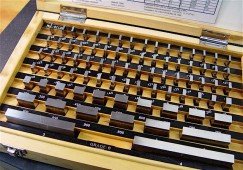
However, the right instrumentation is only half of the story. Ensuring that your measurement equipment is calibrated and working perfectly is also vital. If you are measuring with a gage that is out of tolerance, it will not give you the precise data that you require to confirm that production meets specification. There is so much time, labor and materials wrapped up in producing a firearm. If only one piece is not correct, the entire weapon may not function correctly. And worse, it could create a potentially harmful situation for either the gunsmith or the shooter.
Proper calibration quantifies and improves the measurement performance of an instrument. It will reduce errors in measurement and ensure consistency between the measurements you take. Too often, calibration is neglected because of cost or a lack of time. However, the improved results, and therefore better-quality product, make it worth the time and money.
Simple day-to-day use is enough to put a tool out of calibration. Metal measurement surfaces, like on calipers or micrometers, can build up debris over time, particularly if used in a less than spotless environment. If oil gets onto the tool, carbon dust can stick to it and interrupt the correct function of any gears it may have. When you think of all the human factors, like employees who don’t treat tools with the same care as their own or worse, customers who touch and don’t respect, you can easily see why regular calibration is necessary.
Headspace and timing gages are particularly important to have tested regularly. Because of the way they’re used, they wear even faster than many other gages. In fact, the US Army, in their Technical Bulletin 43-180, requires all headspacing and timing gages to be calibrated every 360 days, regardless of how much the gage is used. Failure to calibrate could result in serious injury. For all gages, unsurprisingly, dropping them can necessitate a calibration. The jostling that comes with moving (think gun manufacturers moving from the Northeast to more gun-friendly states) can also make them deficient. If you’re using gunsmithing screws, it’s likely you have thread gages to check the quality of the threads you’ve tapped. It’s tempting to use just a little extra force to make it pass, but each time slightly distorts the threads on the gage. Overtime this can result in an inaccurate piece of equipment.
For spring testers, make sure you’re using them in a clean environment away from other equipment. Something slightly leaning on the top plate over time can affect measurement. Lean hard enough and you completely blow out the load cells, making the device useless. Hint: If you can’t zero your spring tester, your load cells are probably blown.
To get the right amount of torque on your rings and bases, you’re probably using a torque wrench. However, the delicate adjustable wrenches for gunsmithing are very easy to over torque. If you’ve got a wrench that goes up to 80 inch pounds and you give it an extra hard twist, it will go out of tolerance. Dropping it can also make it deficient. The Army specifies that any torque wrench dropped farther than three feet must be recalibrated.
One common mistake people often make with torque wrenches is to store them loaded. For example, you’ve got an adjustable wrench which goes from 40-80 in/lbs. You torque a bolt down to 75 in/lbs and then put your wrench away. This leaves the load on the spring which wears it out prematurely, so always zero the wrench and clean it before putting it away.
If you are taking linear measurements down to or less than 0.001″, it’s advisable to have a surface plate, a solid, flat plate used as a horizontal reference plane. Most are made with black or pink granite, with the quartz content of the plate determining its wearability. Pink wears better than black, but it’s also more expensive. Whichever you use will ensure you have a baseline that is perfectly horizontal.
However, like your gages, surface plates can go out of tolerance even with proper care. Use it only for measurement, not for a table or a workbench. Also, be aware of how you are using your surface plate. If you have a height gage on it and use it repeatedly, the surface will wear unevenly, resulting in inaccurate measurements. Make sure you clean it, with either specially designed surface plate cleaner (Starrett makes a good one) or denatured alcohol. Note, never use isopropyl alcohol to clean any of your instruments or gages. It leaves a film which can build up over time and affect your measurements.
Enough of the negatives. What can a gunsmith do to calibrate their measurement tools?
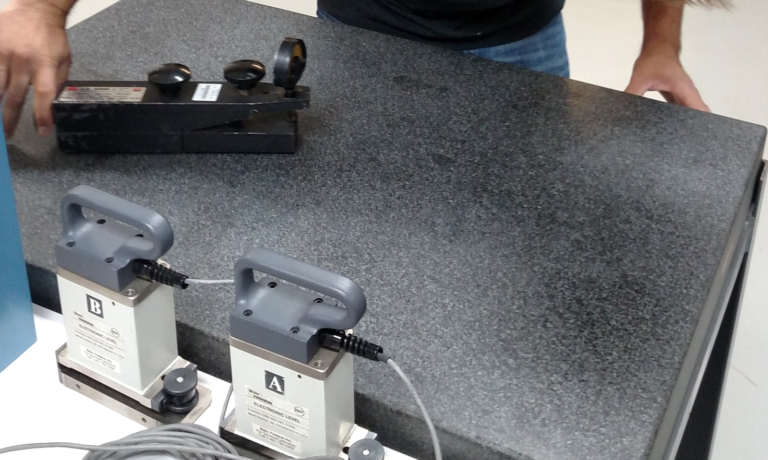
Make sure the environment where you use your gage blocks doesn’t change much in temperature, as they will expand and contract, giving you variable results. Don’t drop or bang your blocks together. This can change the molecules in the steel and alter the size of the block, sometimes significantly. Like other measurement equipment, however, repeated use over time will slightly alter the gage blocks, no matter how carefully they are handled. This means they’ll need to be calibrated and this is where the measurement professional comes in.
Precision measurement companies are in all of the 50 states and most can verify or calibrate all of a gunsmith’s measuring tools. It is surprisingly affordable if you do not require NIST traceable or ISO 17025 accredited calibration.
However, if you are manufacturing for sale, it is recommended that you choose a calibration company who can provide 17025 certifications. This means the laboratory and/or the technician has been found competent and proficient to perform specific calibrations by an international regulatory body. Not only is the lab accredited to perform the work, but they will have a robust system to ensure the quality of their laboratory processes and measurements.
Many large customers require their suppliers to have ISO certified calibrations. A precision measurement company such as Cross (www.crossco.com) can help handle such calibrations.
To wrap up, proper handling of your measurement tools can help ensure they continue to give accurate results. It is important to realize that overtime and through repeated use, even the best-kept tools need to be calibrated. With regular calibration, gunsmiths can ensure they produce the most accurate parts which meet spec and combine to create a high-quality firearm.
Take a look at the article in American Gunsmith Magazine.