The new wave of collaborative robotics is here! Mobile robots and Automated Guided Vehicles (AGVs) are a way to autonomously transport a load over long distances. The load can be whatever you want it to be: parts, other robots, cameras, mail and more.
Modern work environments are constantly changing as tasks become more variable based on any number of criteria. AGVs have been the traditional method for autonomous transport, but mobile robots have adapted to provide the support demanded by today’s end user, such as less predictable floor layouts and workstation use. The revolution in the autonomous vehicle world is not the autonomous vehicle itself, but HOW the vehicle goes about achieving its goals and how it has become a flexible platform.
Defining Mobile Robots and AGVs
There is no solid definition of what mobile robot means, but it is most often taken to mean a device that can move autonomously from place to place to achieve a set of goals. Mobile robots have been around for some time. If we think about it on the most basic level, the small vacuum cleaner that runs along your floor is a mobile robot. Since then, the technology has advanced significantly. Today, they are used in factories, for military operations, in healthcare, for search and rescue, as security guards, and in homes.
Two really cool, advanced applications of mobile robots are in mining and military. You know those huge dump trucks at mining sites, the ones with wheels the size of your car? Those are mobile robots. Furthermore, detection and removal of landmines is an important worldwide problem, and the military uses mobile robots to detect them. You also may be thinking, what about Google car? Yep, that is a mobile robot as well.
The next thought that might be popping in your head is, ‘Hold on, we’ve had automated vehicles in our plants for years’, and this could be true. AGVs were invented in the ‘50s and have been operating effectively in factories for decades. So we have mobile robots and AGVs? What is the difference?
Automated Guided Vehicles
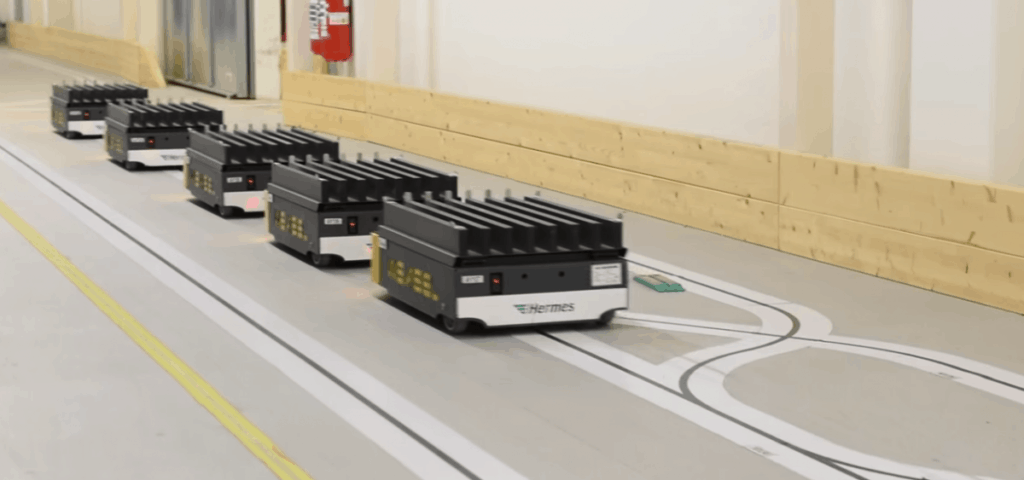
An AGV does exactly what the name says that it does. It is automatically guided. But what is it guided by? There are three main types of guidance systems used to ‘tell’ the robot where it needs to go.
- Wire guidance uses wires embedded in the plant floor that are sensed inductively by the vehicle in order to determine its lateral position.
- Inertial guidance uses gyroscopes and tracks the position of the wheel to find its position. Magnets are then placed in strategic locations to reset the system. This is key because it helps deal with the inevitable drift of the system.
- Laser guidance uses a laser emitter-receiver. It senses retroreflective landmarks strategically placed throughout the plant. By sensing the landmarks, the vehicle can then triangulate its position.
AGVs can be very impressive. I have seen cases where the entire plant floor is mapped out by embedded wires in the ground. When the machine is ready to be unloaded, a truck-sized AGV goes and picks up all of the parts at once and drives itself back to home.
Mobile Robots
A mobile robot’s task is very similar to that of an AGV’s: get my stuff from point A to point B. However, the way it goes about it is completely different. Instead of using an infrastructure (wires, reflective markers, etc.), all of the sensing and path planning is done onboard by the robot. A mobile robot uses sensing components that are built onboard the machine in order to detect the environment. Commonly used sensors are area scanners, diffuse laser sensors, and cameras.
Typically, when a mobile robot is first installed, the robot is jogged around the plant while the sensors are running. After collecting all of the data from the plant floor, it then creates a virtual map of the entire plant floor. This is extremely useful because it gives the robot the ability to know where it is going without the use of a sensory infrastructure, while also allowing it to be taught a different map very easily. With an internal map and live sensor collection, the robot can navigate through an environment on its own, creating its own paths and sensing an ever changing plant floor.
Furthermore, the robot will use different algorithms to accomplish localization and navigation. These systems are usually referred to as SLAM algorithms: Simultaneous Localization And Mapping. The software can recognize key features in the environment to help localize itself. For example, if there is an oddly curved wall, the robot will use that feature to localize itself and ‘double check’ where it is on its map. This technique reduces the amount of drift in the system.
AGV | Mobile Robot | |
---|---|---|
Navigation | Infrastructure: wire guidance, reflective markers, Radio Frequency ID, etc. | Trackless navigation. All sensing is done onboard. Senses the environment in a live fashion |
Obstacles | Obstacles stop an AGV | Goes around obstacles and finds what the best path is according to its internal map |
Flexibility | New tracks and infrastructure to be installed | Easily be remapped and taught new destinations and goals |
Expandability | Possible to add new tracks and new units to it | Everything is managed on a fleet software package |
Charging | Docking Station | Docking Station |
Which is best depends on your situation
It is becoming necessary for humans and robots to share the same workspace. This has led to the need for robots to be able to communicate and sense when objects and humans are around them. AGVs and Mobile Robots have been around for some time. However, mobile robots are just now emerging in the industrial plant environment. The two biggest differences between an AGV and a mobile robot is that the mobile robot does not use an infrastructure to navigate and it can find new paths on its own.
If you find yourself in need of robotic assistance in your workplace, Cross has many resources available to help you select, program, and support your new addition.