Supplier Resource
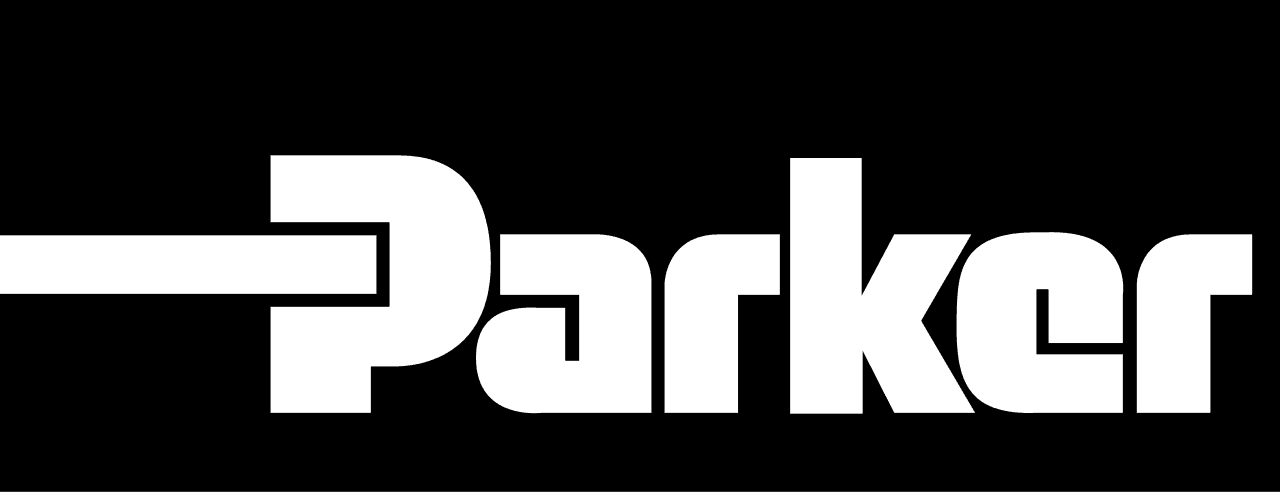
Parker ToughShield Plus
Have you ever tried to disassemble a hose from a piece of equipment, only to find that the rusted adapter won’t allow you to break the connection? Then you know about rust and the problems that can come with it! And it isn’t just connection problems…you can have system contamination, leaks, migrating rust to other components, maintenance issues, and it just looks terrible. Who wants rust on that beautiful piece of hydraulic equipment?
Red Rust Deterioration of Fittings can cause:
- system contamination
- potential leaks
- fitting connection problems
- aesthetic quality concerns from end-user
- maintenance difficulty
- improper function of adjacent components (valves, pumps, cylinders)
- accelerated corrosion of adjacent components
This is why Parker has developed ToughShield Plus – The next level in corrosion protection. ToughShield™ Plus is Parker’s new patent-pending standard zinc-nickel plating on all steel tube fittings and adapters worldwide. It provides significant improvement to corrosion resistance versus other available plating technologies. This means end users benefit from less frequent and easier maintenance, extended fitting service life, and increased resistance to the migration of rust to adjacent components. For manufacturers, it means a decrease in warranty claims and aesthetic quality concerns due to corrosion.
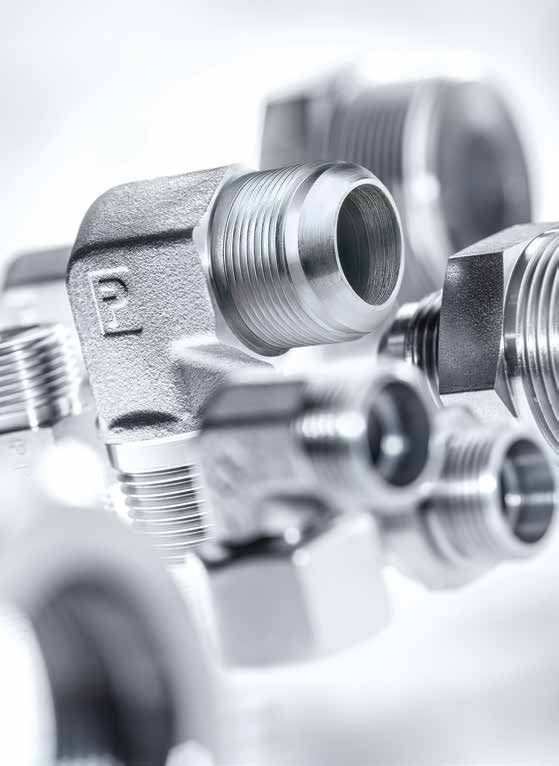
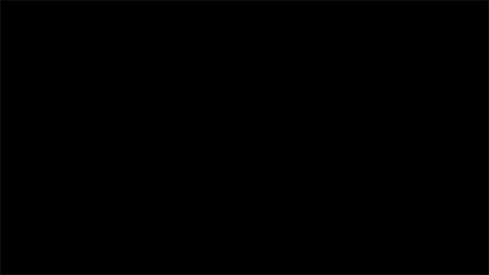
Fittings with Superior Plating
Prevent the ravages of red rust longer – tube fittings with Parker Superior Plating have unrivaled corrosion and rust protection. Prevent the ravages of red rust longer – tube fittings with Parker Superior Plating have unrivaled corrosion and rust protection. The superior corrosion resistance of Parker’s latest plating technology is validated through ASTM B117 / ISO 9227 neutral Salt Spray Testing (SST), as well as two Cyclical Corrosion Tests (CCT) – ISO 16701 and SAE J2334. CCT is widely considered to provide a closer correlation to field corrosion conditions. ToughShield Plus is the first standard plating system in the fluid power industry proven to offer this exceptional level of resistance to red rust. Learn more about salt spray testing.
Stop by one of our Cross Hose & Fitting stores to talk to a specialist and see how you can prevent red rust in your application. We stock a wide selection of sizes and thread styles of Parker adapters protected with durable, high-quality TS1000 plating, to help you reduce replacement costs and downtime. If you want to extend the life of your fittings further, ask our associates about stainless steel fittings.
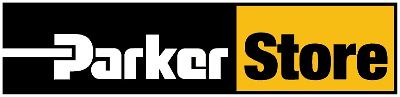
Advantages of Toughshield Plus
The advantages of Toughshield Plus and the true cost of corrosion goes beyond just replacing a tube fitting or adapter. Since corrosion can affect every aspect of your system, the advantages of using ToughShield Plus are far reaching:
Extended Fitting Adapter Life
ToughShield Plus provides significantly longer corrosion resistance which means extended service life for your equipment's systems, higher productivity for your personnel, and ultimately more revenue for your operation.
Easier / Less Frequent Maintenance
Rusted tube fittings and adapters, as well as adjacent components, are more difficult to disassemble and replace when "rusted" together and wrenching surfaces are compromised. ToughShield Plus prevents rust and its migration longer than the industry standard, making routine maintenance easier.
Increased Resistance to Corrosion Migration
Once corrosion consumes the fitting/adapter surface, it can accelerate by migrating to other components such as a cylinder boss or valve. This leads to the need for earlier, more frequent, and more costly repairs. ToughShield Plus fights corrosion longer, providing critical defense for your system.
Increased Equipment Uptime
When equipment and the personnel who operate them aren't working due to maintenance from corrosion, this downtime can lead to loss of revenue and reputation, as well as the total cost of ownership (TCO) of the equipment. ToughShield Plus plating fights corrosion longer, ensuring more uptime.
Prevents Aesthetic Quality Concerns
Rusted components on equipment affect the overall aesthetics leading to a lack of confidence in the equipment and a hit to the manufacturer's reputation. ToughShield Plus plating fights corrosion, and the migration of corrosion, longer protecting the integrity of the equipment and operation.
Saves Warranty Cost
For equipment manufacturers, tube fittings and adapters that corrode quickly can lead to warranty claims and loss of reputation. ToughShield Plus helps prevent corrosion longer in systems, preventing costly hits to the bottom line.
Resources
Videos
More information From Parker
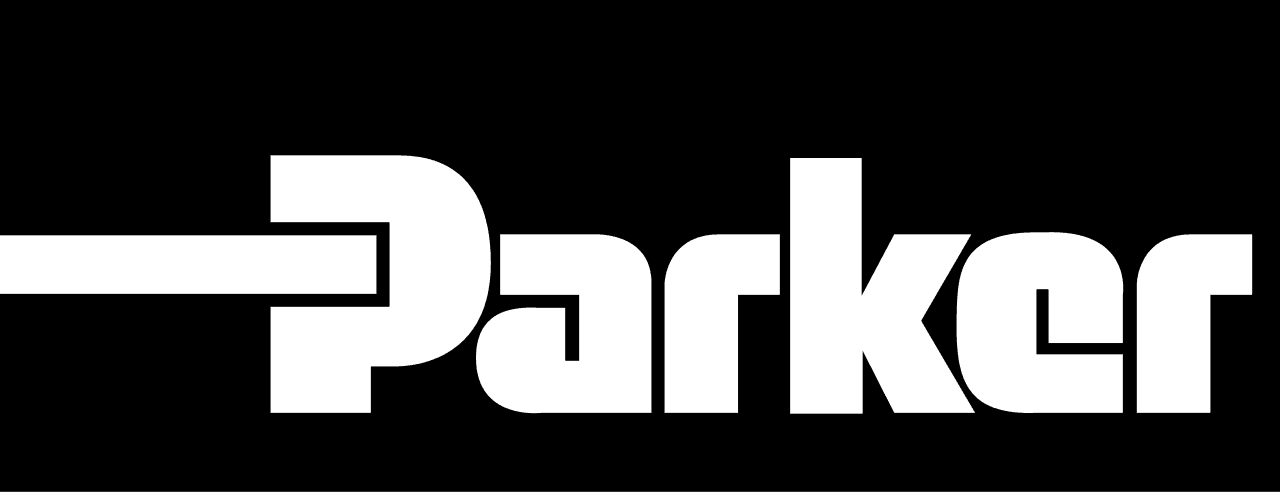
Interested in learning more? Contact a Cross team member today to discuss your application and see how we can help your operation!