Once you’ve decided that an Oval Gear Meter is the best flow meter for your specific application, there are a few key things you will need to know to narrow your selection down to a single oval gear flow meter.
What is the Flow Rate (max and min)?
The maximum and minimum flow rates of the liquid measurement system are one the most important parameters for proper selection of a flowmeter. Referred to as “sizing the meter”, we typically begin by determining your normal flow rate, along with a preferred line size (if any).
Using your flow rate as a guide, a preferred line size is determined by finding a meter size where your normal flow rate is approximately 60% of the max flow rate. For instance, let’s say your application has a minimum flow of 5 GPM and a maximum flow of 35 and a normal operating rate of 25 GPM. Start by dividing 25 by 0.6 to find 60% of 25. In this example, that’s 41.7 GPM.
Next, check out the available flow ranges on each of the available meter sizes to find one with maximum flow that’s close to 41.7 GPM. The OM025 is a 1 inch meter with a range of 2.6 to 40 gpm which makes it a good match for the 60% test. Next determine if the min and max flows will work. In this instance the application range is 5-35 GPM and the meter is capable of measuring from 2.6 to 40 gpm, so we’re good! Assuming you can work with that one inch line size, the OM025 is a good match!
What fluid are you measuring?
Ensuring the compatibility between the liquid to be measured and the materials of construction of the flowmeter is critical. Be sure to check the compatibility of all body, rotor, and elastomer materials with the fluids you are measuring. Choosing the wrong materials can shorten the life of your oval gear flow meter, affect the accuracy of your process, and worse yet, create a safety hazard.
When choosing compatible materials for an Oval Gear meter, you need to consider more than just the body material. Other wetted parts that must be compatible with the process fluid include the rotors and elastomers. For example, most petroleum products are well suited for an Oval Gear meter with an aluminum body and PPS Rotors. But what about the O-Rings? Choose the wrong O-Ring material and they may soften, harden or even swell to a point where your meter may be damaged and/or your readings become inaccurate.
Choosing the Best Rotor Material for Your Application:
PPS vs. Aluminum or Stainless Steel
When your process fluids are compatible with all three materials, why choose PPS over Stainless or Aluminum? Consider the following:
- Reduced weight of PPS compared to Aluminum; leading to a slight reduction in pressure losses, and improved accuracy at start-up as there is less mass to move when the liquid starts to flow.
- Reduced manufacturing costs which translates to lower purchase costs.
- Reduced manufacturing costs also lead to lower maintenance/repair costs.
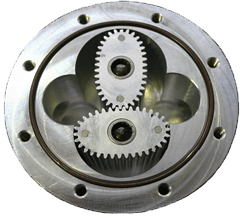
- PPS is immune to galling (adhesive wear) that will occur between aluminum components; this means that when an aluminum flowmeter with PPS rotors suffers severe damage (from incorrect installation, incorrect use, catastrophic damage of upstream equipment, dirty liquids) in most cases the aluminum measuring chamber will remain undamaged meaning the flowmeter can be repaired with a replacement set of rotors. With meters containing aluminum rotors there will often be damage to the measuring chamber from contact with the aluminum rotors and the subsequent galling; this will often lead to a meter that is not repairable.
- PPS is immune to many more liquids/chemicals than aluminum
- PPS bearings are very resistant to wear, due to their high content of glass fibers. This gives a bearing that is significantly less sensitive to lubrication quality than the roller bearings used in aluminum rotors
- PPS rotors produce significantly less operating noise than do metal rotors – often 10-15dB less at maximum speed. This can be very significant for indoor installations, especially when multiple flowmeters are installed in a single building.
- For many applications where a stainless steel flowmeter is required PPS rotors can still be used in place of stainless steel rotors for a significant cost saving without any reduction in meter performance or life span
Chemical compatibility considerations for the major components used to build an Oval Gear Flow Meter are not the end of the story. When considering which rotor material will work best, you should also give some consideration to the materials used for the rotor bearings.
Rotors have a very small (~0.1 mm) thrust bearing that allows the rotor to spin without rubbing on the meter cap or body.
- Stainless steel meters use a carbon ceramic bearing that is self-lubricating but consequently may wear faster.
- Aluminum rotors use hardened steel roller bearings – making them unsuitable for water applications or liquids with viscosity like water where no lubrication is available.
- PPS rotors are self-lubricating; requiring no other bearing material and the best choice when no lubrication is available from the liquid.
Your choice of rotor material and consequently, the respective bearing type is crucial to the trouble free operation and long life of your oval gear flow meter.
How does viscosity affect flow meter choices?
Oval gear meters have the advantage of being relatively immune to changes in viscosity. This is as opposed to turbine meters where changing process conditions can affect the fluid’s viscosity and ultimately its accuracy.
For liquids with viscosity in the range of 3-1,000cP, you typically don’t need to consider the effect of the fluid viscosity on an oval gear flowmeter. For liquids below 3cP, like water (1cP), you need to allow for a slightly higher minimum flow rate to maintain the standard accuracy of your flowmeter due to slippage of the fluid between and around the rotors. For liquids with a viscosity above 1,000 cP, the pressure drop across the meter must be considered. High viscosity (Keishi Cut) rotors can reduce pressure drop without affecting accuracy.
Keishi Cut is a Japanese term for high viscosity rotors. Keishi Cut rotor’s have every other gear tooth machined on the flat side of the gear, to provide pressure relief between the gear teeth. In most instances, this special machining can reduce the maximum pressure drop across the meter by approximately 50%. High viscosity (or Keishi Cut) rotors are normally used for fluids with a viscosity above 1000cP.
How does viscosity affect flow meter choices?
Oval gear meters have the advantage of being relatively immune to changes in viscosity. This is as opposed to turbine meters where changing process conditions can affect the fluid’s viscosity and ultimately its accuracy.
For liquids with viscosity in the range of 3-1,000cP, you typically don’t need to consider the effect of the fluid viscosity on an oval gear flowmeter. For liquids below 3cP, like water (1cP), you need to allow for a slightly higher minimum flow rate to maintain the standard accuracy of your flowmeter due to slippage of the fluid between and around the rotors. For liquids with a viscosity above 1,000 cP, the pressure drop across the meter must be considered. High viscosity (Keishi Cut) rotors can reduce pressure drop without affecting accuracy.
Keishi Cut is a Japanese term for high viscosity rotors. Keishi Cut rotor’s have every other gear tooth machined on the flat side of the gear, to provide pressure relief between the gear teeth. In most instances, this special machining can reduce the maximum pressure drop across the meter by approximately 50%. High viscosity (or Keishi Cut) rotors are normally used for fluids with a viscosity above 1000cP.
Sintered or Wire Cut Rotors, what’s the difference?
Stainless steel rotors can be manufactured by two methods:
- Sintering – Sintered rotors are constructed using a metal powder which is molded, compacted and heated to just below its melting point. This results in a complex process of solid state bonding occurs forming a shape that resembles a cast item.
- Wire Cut – Using this method, the rotor is cut from solid stainless steel billet.
Sintering is the process of compacting and forming a solid mass of material by heat and/or pressure without melting it to the point of liquefaction. The atoms in the materials diffuse across the boundaries of the particles, fusing the particles together and creating one solid piece. Because the sintering temperature does not have to reach the melting point of the material, sintering is often chosen as the shaping process for materials with extremely high melting points such as tungsten and molybdenum.
The sintering process is far more cost effective with less waste material and low machining demands than wire cutting. However sintered rotors have a limitation with acidic liquids that 316 Stainless Steel would otherwise normally be suitable for. Due to the chemical process of solid bond formation, there are far more porosities in sintered stainless steel than cast metal. As the sintering process produces weaker bonding than the casting process, the acid has a large surface area in which to attack the weaker intergranular bonds and delaminate or reduce the sintered rotor back to the powder from which it formed. For this reason GPI recommends sintered rotors as suitable only for applications down to approximately pH 2 – this would be similar to vinegar or lemon juice.
Wire cut rotors will have a lower corrosion rate when used in acid service, but are still subject to some limitations based on the actual fluid and concentrations being measured.
When the normal operating viscosity is below 1000cP remember to factor in the minimum operating temperature. For instance, at start up during the winter months, there are many places where minimum temperatures can and do drop well below 0°C, thus increasing the viscosity of the oil or grease significantly to a point well over 1000cP. In these instances, high viscosity rotors are recommended.
Line Pressure – What is Your Maximum Pressure?
Your maximum system pressure must be considered when specifying an oval gear flow meter, or any invasive type metering technology for that matter. The maximum pressure rating is typically available in the product data sheet as well as on the data plate attached to the meter itself. This rating is based on the maximum “non-shock” pressure at the maximum allowable process temperature for any given flow meter.
It’s important to note that oval gear meters are precision instruments and accuracy can be affected by over pressurizing your meter. This is an important piece of information to consider when choosing an appropriate flow meter for any application.
End Connections
Like most flow meters, ovals offer a number of different display/output options. Would you like to read the rate on the meter, or transmit it into a remote unit somewhere else or a PLC? Would you like to record your volume on a mechanical register or electronic? Is the installation in a safe or hazardous area, which may require a flame proof or intrinsically safe instrument? These questions help to determine what instrument you choose to accompany your meter. Two common options for sensors on oval gear meters are reed switches and Hall Effect sensors.
Data collection
Like most flow meters, ovals offer a number of different display/output options. Would you like to read the rate on the meter, or transmit it into a remote unit somewhere else or a PLC? Would you like to record your volume on a mechanical register or electronic? Is the installation in a safe or hazardous area, which may require a flame proof or intrinsically safe instrument? These questions help to determine what instrument you choose to accompany your meter. Two common options for sensors on oval gear meters are reed switches and Hall Effect sensors.
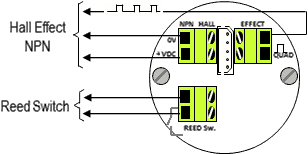
NPN Hall Effect and Reed Switch (contact closure)
Conclusion
If you make your choice using pricing and/or availability as your guide while paying little attention to what’s required for your specific application, you are asking for a shortened meter life and inaccurate readings. Worse yet, you may be creating a safety hazard that could prove to be much more devastating in the long run, than what little you saved in cost and lead-time.
Experience matters! Contact us to discuss your particular application with a Cross instrumentation specialist:
lorem