Proper Hydraulic Hose Routing Simplifies Maintenance and Reduces Failure
When high-pressure hydraulic hoses fail, they can be responsible for lost productivity, equipment failure, and personal injury – all coming at a steep cost to the machine or company owner. In hydraulically controlled equipment, some component locations cannot be changed due to the structure of the equipment, so work should ideally be done upfront by a designer to eliminate as many potential leak points and make maintenance as simple as possible.
When hydraulic hose installation is straight, there must be enough slack in the hose to allow for natural changes in length when pressure is applied and to accommodate for possible component movements and machine vibration. If the hose is too short, it may pull from the hose end fitting or stress the hose fitting connection eventually causing damage. On the other hand, if there is too much slack in the hose, the hose may snag on other pieces of equipment or rub on other components causing premature wear and tear.
Mechanical straining of the hydraulic hose should be avoided, such as not adhering to the minimum bend radius. A tighter bend radius will cause an excessive force to be applied to the inner wall of the hydraulic hose causing a weak point and shortening the hose lifespan. Take a look at our related technical guide: Bend Radius in Hydraulic Hose.
Proper hydraulic hose routing also affects the selection of hose ends as the correct hose end can eliminate unnecessarily strain. For example, if a hydraulic hose must be fitted into a tight space that wouldn’t adhere to the minimum bend radius, using a 90-degree elbow can eliminate unnecessary hose length or awkward positions.
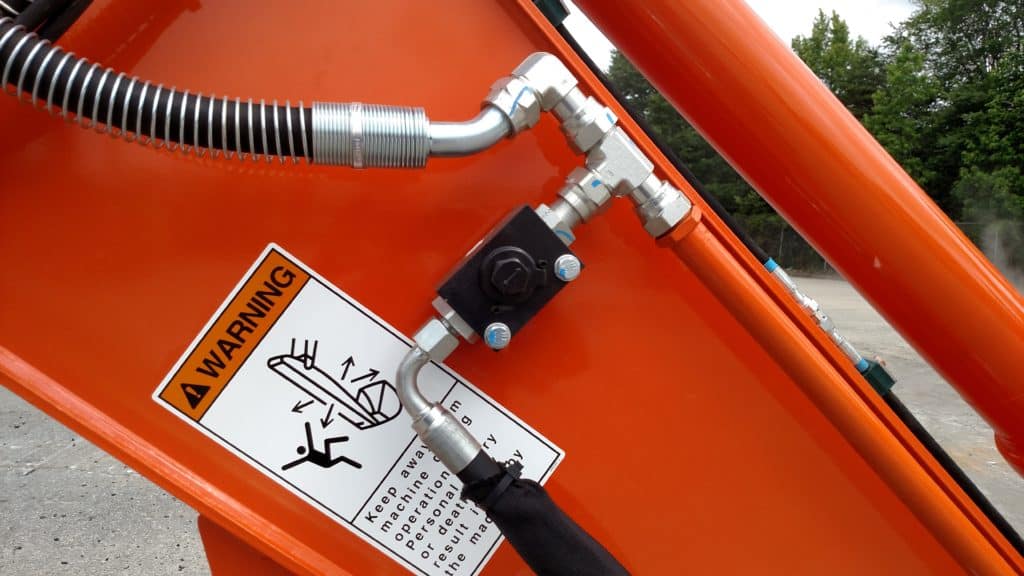
90-Degree Hydraulic Hose Fittings
Like fitting selection, the correct clamping or support system is also very important to securely route the hose. Fastening the hydraulic hose correctly avoids the hose contacting other components or rubbing together. During installation, avoid fastening, crossing, or clamping high and low-pressure hoses together. The changes in length during use could wear on the hose covers causing damage. Take a look at our top 6 quick tips for correct routing of a hose assembly.
Increase Your Hose Assembly Life Service Life by Avoiding Routing Mistakes
1. Avoid Twisting Assemblies
Like fitting selection, the correct clamping or support system is also very important to securely route the hose. Fastening the hydraulic hose correctly avoids the hose contacting other components or rubbing together. During installation, avoid fastening, crossing, or clamping high and low-pressure hoses together. The changes in length during use could wear on the hose covers causing damage.
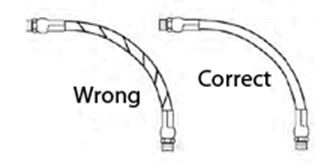
2. Do Not Bend Hoses Tightly
Allow ample bend radius to avoid hose collapse of the line and restriction of flow. Never bend the hose tighter than the minimum bend radius specified by the hose’s manufacturer. Assure that the bend does not start right at the fitting.
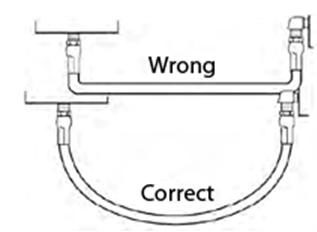
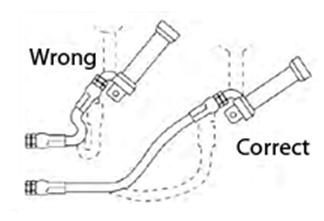
3. Use Elbows or Other Adapters
Use elbows or other adapters to ensure the minimum bend radii are within limits specified by the hose’s manufacturer, to reduce needed hose length and to enable hose assemblies to be routed neater – away from harm’s way.
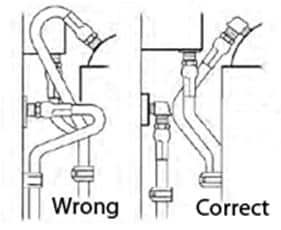
4. Use Hose Clamps
Using clamps is an important aspect of proper routing. Clamps secure the hose in its proper position and help to keep it from being pulled, hit, crushed or rubbing against surrounding moving parts.

5. Prevent Assemblies from Becoming Fully Extended
As hose assemblies get pressurized, their diameter increases and they become slightly shorter. If a hose is permitted to assume a fully extended state, it may be too short when pressurized. The result is the hose being pulled out of the fittings. With repeated cycles, this will decrease the hose’s service life and can lead to a failure. Design at least a slight bend/slack to any hose route to prevent this from happening.
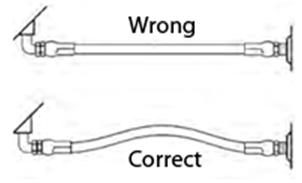
6. Protect Assemblies from Damage
Hydraulic hose manufacturers estimate that 80% of hose failures are attributable to external physical damage through pulling, kinking, crushing or abrasion of the hose. Abrasion caused by hoses rubbing against each other or surrounding surfaces is the most common type of damage.
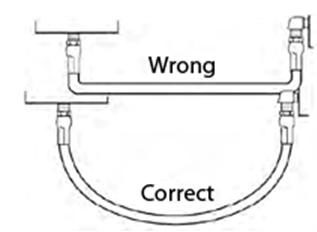
No matter what your industrial application is, Cross hose and fittings specialists can help you determine the right hydraulic hose solution for your operation. Stop by one of our store locations or send us a message to learn more.