“We want Flexible Automation”
This is what I was told when recently visiting one of the largest contract manufacturers in the world.
Their main market is Consumer Electronics, which has a relatively short product run rate of 6-12 months. Despite the high turnover, they would purchase customized automation equipment for each new product and application. For example, they would spend between $20,000 and $40,000 for automated ‘de-stacking / loading’ machines that were specifically designed to load a stack of parts onto a conveyor. After that part’s life-cycle, the automation equipment would typically go sit in storage until someone figured out how they could re-purpose it (which did not happen very often). This approach is described as Fixed (or Hard) Automation, which could be defined as when an automation application is customized around a single product and a specific task.
This is a very common practice in automation. As an engineer, we see an application or challenge and design custom tooling and fixturing to fulfill the job without thinking about future limitations. For each new part or product, you need more custom tools, more floor space, and more changeover time. This requires lots of integration and programming adjustments as well! As more and more manufacturers start to face the challenge of low volume and/or high mix of parts, a more dexterous and flexible solution is required.
Rather than continue down this path of completely overhauling a part assembly line every 6-12 months, this manufacturer wanted to implement a piece of automation that could be easily re-tasked to handle other tasks for future orders. While Fixed Automation may be less expensive for them in the short term, they would be able to save costs on future production lines by using this type of Flexible Automation.
What is Flexible Automation?
Flexible Automation is the ability for a robot or system to be quickly and easily re-tasked to change product design for both low and high mix manufacturing. When properly utilized, a Flexible Automation cell can improve efficiency by evolving with your process and demand, reducing and fixing production costs, improving quality, and eliminating health and safety issues.
A great example of flexible automation is at the state of the art Tesla Motors Factory in Freemont, CA. As Chris Anderson says in his book Makers: The New Industrial Revolution:
“Tesla has built the most modern factory in the world. It happens to build cars, but it could build anything. It is not just automated, it’s a veritable robot army. Hundreds of general-purpose KUKA robot arms do everything from metal-bending to assembly. Flat-topped robot vehicles carry car chassis around, charging themselves on inductive pads as they go. Robot painting arms from Fanuc can open car doors to spray around them, and then close them again when they’re done.”
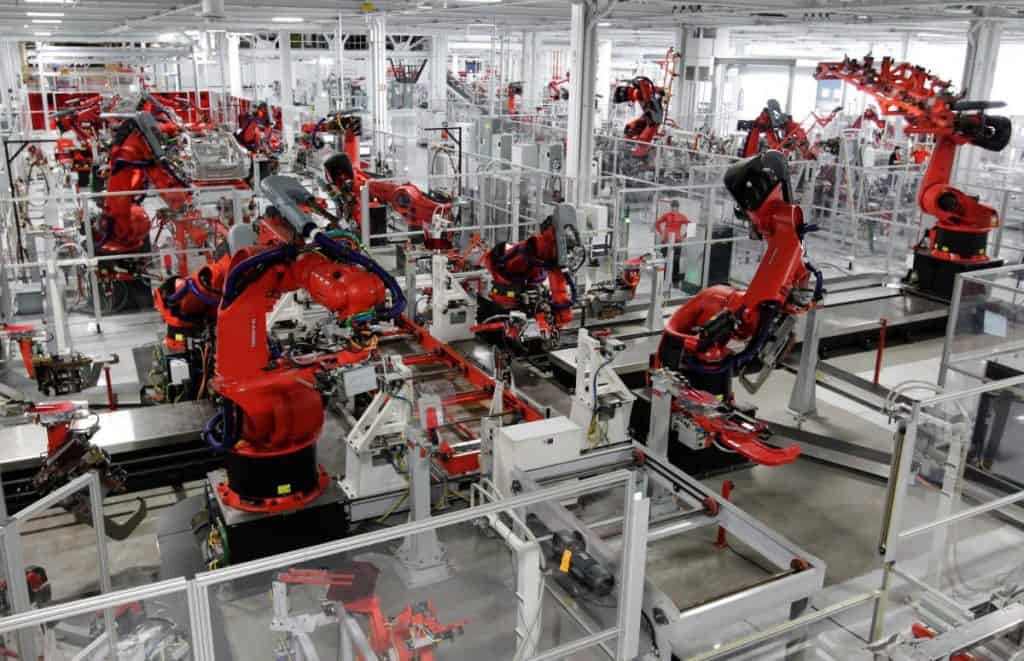
As you can see, Tesla utilizes large 6 axis robotic arms and robotic Automated Guided Vehicle’s to make their assembly process flexible. However, robots themselves typically have no sensing ability and rely solely on their mechanical repeatability to complete a task. Therefore there are many other components that go into this system to provide sensing and smarts to these robots (and NO you don’t have to use an expensive robot to have a flexible solution – really!).
When someone is looking to design and integrate a flexible work cell or assembly line, they should start by making sure their system contains these 3 main components of a Flexible Automation system;
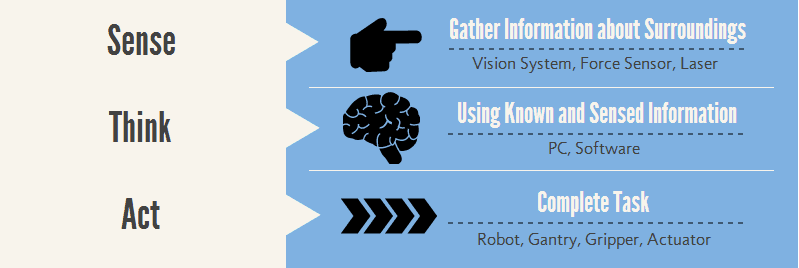
Flexible Automation Example Application
Let’s say that you have a CNC machine that you would like to machine parts on an ‘as needed’ basis to eliminate stocking of components. When a production run starts, the work cell will be told a quantity of a certain part to manufacture. A fixed automation system may include a machine tending 6 axis robot with a tool changer for each type of part, a set rack or jig that will be manually loaded, and safety components. This solution requires significant floor space for tool changing, safety, and rack.
A possible Flexible Automation approach to this cell would include the following components;
- Microscan Vision Hawk Smart Camera
Smart Camera to be used to locate and ID unmachined part by dimensions and/or 1D/2D symbols, (Sense / Think) - SCHUNK SDH Gripper with integrated Force Sensors
3 Finger Servo Gripper will be used to pick ID’d part and place into CNC. The force sensors would be used to confirm picking of part (Sense / Act) - Universal Robot UR10 Collaborative 6 Axis Robotic arm
Move gripper to location provided by Smart Camera, place part into CNC and close CNC door. (Act / Think)
Each of these 3 components work together to meet the Sense, Think, Act criteria of Flexible Automation. This solution has the adroitness and versatility to not just handle a machine tending application, but potentially other sorting or pick and place applications down the road!
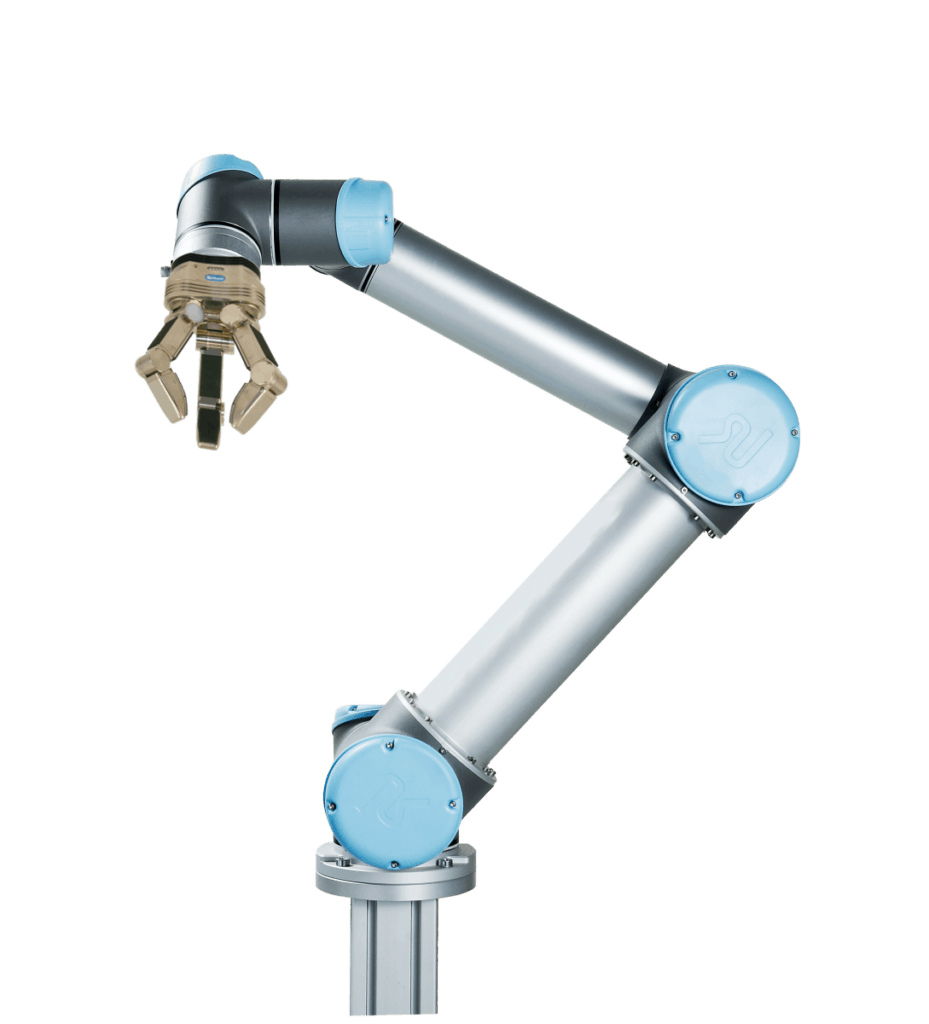
Some benefits of this proposed solution would be;
- Reduce cell size by removing tool changing stations and rack for each part
- Decrease floor space footprint by using a collaborative robot (cobot) and potentially eliminating safety guarding
- Decrease cost of low value-adding labor by being able to ID and locate parts versus being placed in a rack manually
- Robotic cell can evolve with product and can easily be re-tasked to handle future production
- Keeps the production cost flat by eliminating the need for custom tooling and fixturing on future products
This last item is key and truly unique to Flexible Automation. By being able to adapt and re-task on the fly, you can keep production cost fixed whether you are manufacturing a small batch of parts or a large run of parts. This is becoming critically necessary for many US based producers to compete in a low-volume marketplace.
The graph below demonstrates the value that a Flexible solution can bring when compared to Fixed Automation and Manual production. If you look at the Return on Investment for a Fixed solution, it only makes sense for low mix production (i.e. making the same part over and over). Once production goes to medium / high mix, manual labor prevails. This is something that has kept many facilities from automating in the past.
But with Flexible Automation, you can keep your costs in line and have a much quicker ROI:

So what type of solution did we come up with for the Contract Manufacturer mentioned above?
Our system will have to know the status of the conveyor that it is placing a circuit board, so we needed something to sense the encoder signal from the conveyor. Universal Robot recently came out with an update that integrates conveyor tracking into the robotic controller. Therefore we selected a UR5 (UR5 AE3) 6 axis robot arm to think and interpret the conveyor position as well as utilize the built in Stack & Destack Wizard to load the circuit boards to the correct location. To act on these signals by picking a circuit board, we used a strategically designed vacuum gripping head that could be used on any number of board designs. This gripper will be coupled to the UR5 (UR5 AE3) robot to achieve the desired outcome. Once the production run is complete for this board design, this cell can easily be re-tasked versus sitting in a storage closet collecting dust.
So whether it’s a large scale system like Tesla or a single Machine Tending station, when your automation solution is designed to Sense, Think, and Act it will provide you with the flexibility to re-task and handle future production.
No matter what your industrial application is, Cross robotics specialists can help you determine the right robot and accessories to automate it. Contact us today.