Stepper Motors and Drives (Stepper Systems) have always been a low cost alternative to Servo Motors and Drives (Servo Systems), but there are applications where the inherent characteristics of Stepper Systems have advantages other than cost.
There are many Stepper Systems that utilize motor mounted encoders and do some amazing things in a closed loop fashion, such as Stall Prevention, Stall Detection and Torque Control. However, this discussion is based around basic open loop Step Systems where encoder feedback would only be used to detect and or verify actual distances moved.
We are also assuming that the Stepper System has been properly sized to provide both the required speed and or torque for the application.
Some inherent (non-cost) advantages of Stepper Systems are:
- Most Stepper Motors have a natural 200 steps per revolution (steps/rev). Combining this with the fact that most modern Stepper drives can Micro-Step down to 51,200 steps/rev, very smooth very low speed motion (0.1 rpm or lower) can be realized.
- Stepper systems operate at a fixed – but adjustable (open loop) – current level and the motor can be stalled by exceeding the torque being generated. This is unlike a Servo, which will increase current/torque to correct for errors in motor speed. The Stepper Motor will then “Ratchet” as the field continues to rotate, but this causes no inherent damage to the Stepper System. This is advantageous in applications where jams may occur either as a result of process errors or the normal process flow (running to a hard stop). This feature has been utilized in finger safe small conveying, small transfer wheels and screw and nut driving applications.
- Unlike Servo Systems, Step Systems do not dither (oscillate around the set point ) when standing still. This is an advantage for applications where high magnification vision and or high precision sensing is being used.
- Stepper Systems require no tuning for proper motor to command position maintenance and thus are an easy to apply choice for Multi-Axis (XY, XYZ) applications such as CNC and 3D/2D printing. Servos work here as well, but require tuning and ideally zero or matched following errors in order to faithfully reproduce interpolated paths.
- Due to fact that tuning (loop gains) is required in Servo Systems, they may not respond well or at all to very small changes in commanded position. This is not the case with Stepper Systems as they will output even 1 Micro-Step as required.
To be fair, there are situations in which Stepper Systems may not be the best solution. Consider the following:
- Stepper Motors will get hot during normal use because they are always running at full current. This may need to be considered on an application by application basis.
- Stepper Systems move the motor by inputting pulses/steps of torque, so there may be speeds that will excite resonances in a mechanism. These can usually be dealt with by either avoiding these speeds or adjusting the steps/rev setting. Some systems have settings/filters to aid in this.
- As opposed to Servo Systems, which typically have an almost flat torque vs speed curve, Stepper Systems will lose torque as the speed increases, so not all applications can be solved but many are overlooked and never taken advantage of.
Typical Stepper (L) and Servo (R) Torque/Speed Curves
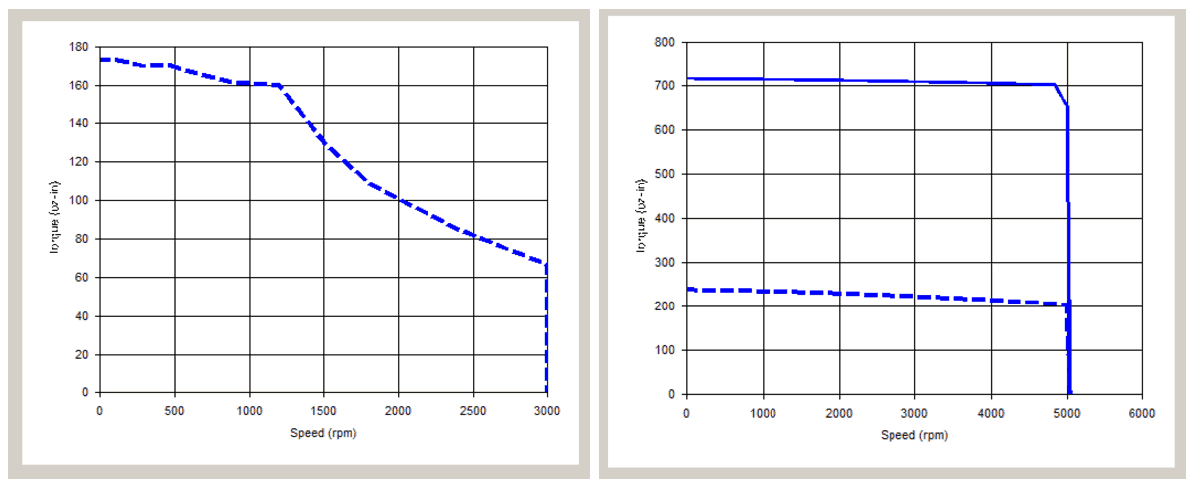
It can be seen that Stepper Systems, while probably less expensive than Servo Systems, also have inherent features that make them a prime candidate in many industrial motion control applications. If you have any comments or questions about either System, contact the experts at Cross today!