Application Note: Optimizing Machine Tending With Robots
For years, suppliers to the automotive and truck transportation manufacturing markets have seen demands for additional processing and finishing to make their components ready for the assembly line. Additional machining and assembly processes are now being required in the contracts of Tier I and Tier II suppliers. This pushes many manufacturers to expand their operations beyond their core competencies to meet added processing requirements while continuing to meet volume demand.
As an example, Cross Company worked with a foundry that is now required to add machining operations after casting a custom part to fulfill their contract with a large assembly plant. The part is one of the highest volume castings for the foundry and it occupies a lot of their time and effort. The malleable iron castings required milling, drilling a blind hole, and tapping operations to be completed in a CNC mill.
For the short term, production management retained the services of several outside machine shops to complete the machine work, however, this has proved too slow and costly to fulfill the contract requirements. Manual part loading and clamping into the CNC mill cost valuable production time and presented a bottleneck to meeting customer demand.
The factory purchased four CNC mills to add in-house machining capabilities. Two robots were acquired for machine loading, however, part presentation to the robot and CNC loading and clamping proved to be major obstacles to a successful implementation.
Specifically, the castings had surface variations that only allowed for rough points as initial reference for milling. Drilling and tapping would be referenced to the first milled surface so the clamping process was critical. Accurate three point clamping was an awkward and time consuming manual process inside the mill that was not easily automated, so a different approach was needed.
As a solution, parts were preloaded onto pallets and fed into the robot cells by two conveyors. The pallets were equipped with location pins on the bottom and a special pin in a housing to mate up with SCHUNK NSR tooling on the robot. This enabled the robot to capture the pallet and place it in the CNC mill with a high degree of repeatability while requiring minimal envelope size.
SCHUNK VERO-S pneumatic clamps matched to the location pins maintained the orientation of the pallet and pulled it down while locking it in place for machining. A manual clamping station outside the robot cells at the infeed conveyors was used to preload the castings and present the pallet to the robot for loading into the CNC clamping stations. Each robot serviced two CNC mills.
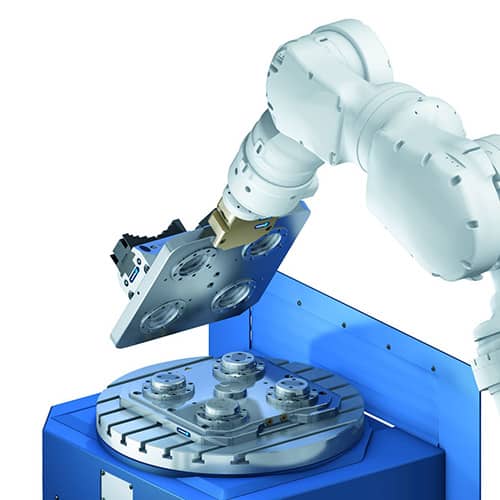
Robot Pallet Loading
The SCHUNK VERO-S clamping system provided sufficient clamping force and repeatability for the machining processes. The SCHUNK NSR robot tooling provided the orientation control and repeatability to provide precise placement of the pallets in the CNC mills. Cross Company assisted with the development of an automated machine tending solution, which resulted in a considerable reduction in labor cost and processing time. Process improvements enabled production to meet the volume demand of the assembly plant contract.
The foundry avoided financial penalties within their production contract and are able to reduce the manpower dedicated purely to loading the CNCs by 75%. The industry standard is clearly evolving to expect part manufacturers to produce a more complete, ready-to-use part. If your CNC stations are not optimized, you could soon feel the squeeze. Work with a Cross automation expert to see how implementing a solution can increase efficiency, improve quality, and reduce risk. Learn more about the ROI for your process.