Case Study: Old Dominion Brush
Cross Mobile Systems Integration Helps Old Dominion Brush Improve Serviceability and Reduce Cost
Old Dominion Brush, or ODB, is a manufacturer of debris collectors, leaf vacuum trucks and trailers. ODB initially worked with Cross Mobile Systems Integration (MSI) on a leaf-vac truck project involving a complete hydraulic system and control system redesign. They were very happy with this initial system as it solved a lot of system challenges, and helped simplify manufacturing. However, ODB works in a highly competitive market. ODB wanted to increase the performance and serviceability of the unit without increasing the cost. The team at Cross MSI and ODB were in constant discussions about how to bring more value to their customers. By utilizing a new controls system approach with an ifm display along with two Enovation Controls power distribution modules, Cross was able to propose a new, simplified solution. This new solution developed by the Cross engineering team reduced the number of components required which helped to improve serviceability, reduce the risk of failure, and lower the cost of components per machine by about 30%. This cost savings allowed ODB to both add features to their subsystem and offset some of the rising costs of raw materials, thus helping to mitigate the rising cost of their entire machine.
System Redesign
The original system designed by Cross for ODB included:
- Seven-inch programmable display for operator interface
- Body mounted control panel that included a mobile rated plc, H-bridge module, Master Control Relay (MCR), Relay and fuse panel, and all of the associated wiring
The new redesigned system includes:
- Seven-inch programmable display
– Operates as the system controller and operator interface, consolidating the system to a single programmable component and eliminating the need for multiple applications - Two Enovation Controls’ Intelligent Expansion Power Distribution Modules
– Includes CAN communication as well as input and output communication
– Eliminates the need for a body mounted controller by being able to provide H-bridge function, high current outputs replacing the MCR, eliminated the need for a relay and fuse panel, and greatly simplified the wiring
Benefits
The redesign reduced the total number of components in the system. This had a number of benefits including faster assembly time, easier serviceability, and less points of potential failure. As part of the upgrade, mechanical relays and fuses were replaced with solid state electronics that can be monitored and reset remotely without the need to troubleshoot blown fuses, relays, etc.
The Cross team was also able to fit the controls and hydraulics into a more compact package which allowed it to be installed on the machine in a significantly more user-friendly location, further aiding in serviceability. The new system has backwards compatibility, so ODB’s older machines can be retrofitted with the new technology. Finally, the price for controls per machine was reduced for ODB by around 30%.
When Britt Calloway, Product and Engineering Manager at ODB, was asked about the benefits of the redesign he said, “We are always looking for ways to increase the value of our brand. Cross understood our needs for the newer panel in this system. The new system is simpler to manufacture, install, and service. They were able to remove components by updating to better components. The new system offers the ability to configure the power distribution through the software. The elimination of relays is beneficial because not only do relays require more service, but they are prone to failure when exposed to harsh environments. Every contact or component is a potential failure point. This redesign takes the complexity out.”
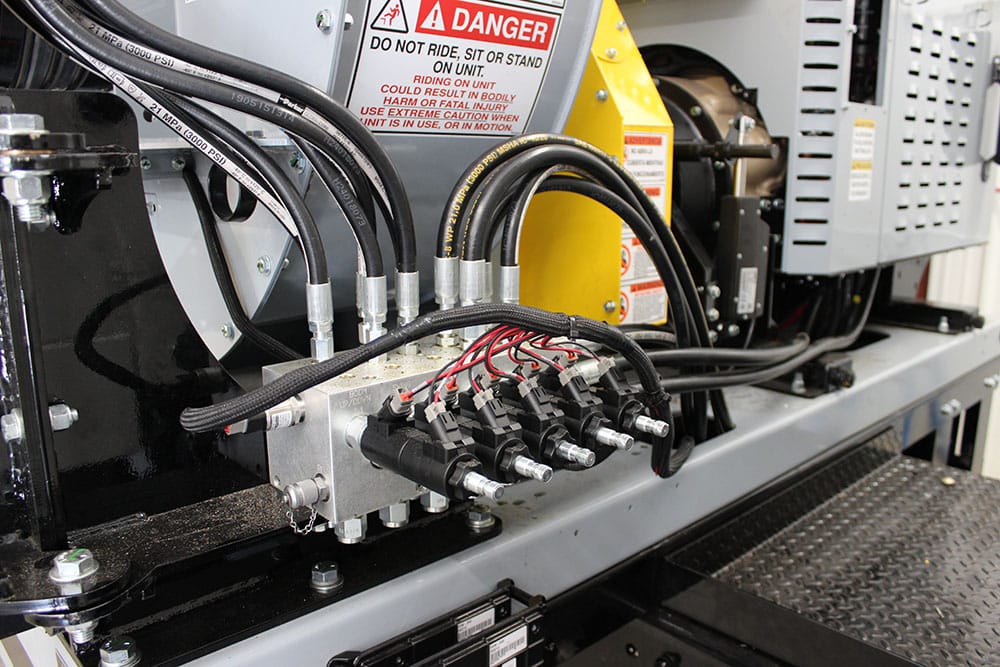
Calloway went on to say, “The Cross team is very responsive. They do a good job of following up on any issues. During this project, we made various programming changes. Sometimes when you take out one piece and replace it with another you think it is isolated, but sometimes it is connected to other things. Cross helps to work through those issues. Their engineers are always an open ear for out-of-the-box ideas we want to try. They come back with practical solutions. We have a small engineering team and Cross provides extra support. Our teams really work together well.”
Cross Mobile Systems Integration went above and beyond to create tangible value for ODB. Even after the original system was built, the Cross team never stopped looking for ways to improve the machine for their customer. By focusing on the customer’s needs, they were able to develop a solution that helped the customer to improve efficiency by making the vehicle easier to assemble and service, reduce risk by removing potential points of failure, and to reduce the cost of their control system by close to 30%. By reducing the cost of the control components, ODB could add features to other subsystems and partially offset the rising cost of raw materials in their redesigned truck. This helped them to mitigate the rising cost of the complete system for their customers.
Download this case study! Cross Company Case Study: Old Dominion Brush
Are you Interested in discussing your project? Contact a Cross team member to learn more about how we can implement a solution like this for your operation!
A member of the Alamo Group, Old Dominion Brush is building on their 110 year tradition of producing high quality, cost-effective street sweeper brooms, debris collectors and replacement parts. For more information, please visit www.odbco.com