Application Note: Improved Efficiency for Filling Station
Cross Company Helps Safety Equipment Manufacturer Double Efficiency in Filling Application
A safety equipment manufacturer needed help making a container filling station more efficient. Cross Automation and J.A. King, which specializes in weight-based filling applications, were able to design a new system that cut the manual labor in half and reduced wasted product.
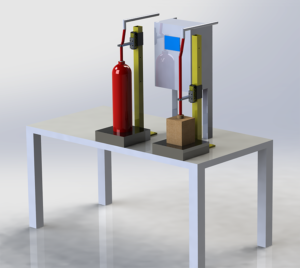
The Application
The customer had a station set up with two scales and an indicator that was used for filling one of three different sized containers. The operator would place the container on the scale and insert the nozzle to manually fill each container to the correct weight. This setup presented several issues.
- It was not possible for one operator to fill two containers at once, so either two people had to be at the station or one scale base sat unused.
- Because they had to manually watch the scale as they filled to ensure the correct amount of product was in each container, there were often over or underfills.
- In the worst cases, the operator would forget to watch the container while it was being filled and it would overflow wasting product–not to mention making a mess.
The customer was looking for a solution that would help automate the process to improve efficiency and remove the opportunity for human error.
The Solution
Cross Automation and J.A. King worked together to create a solution that made the process efficient, simple, and fool-proof. The system consisted of a panel mount indicator with two separate scale bases for monitoring weight as containers are filled.
The team built two custom fixtures that hold the hose over the container for filling. The stands holding the hose have three setting levels for each of the container sizes, as well as a small actuator for the fine movement of the nozzle into the open container. The hoses themselves were equipped with a valve to control the flow of product into the container.
There is also intelligence built in that weighs the empty container and won’t allow a filling recipe to be started for a container of the wrong size. Lastly, an auto adjusting “preact” is used to account for the valve closing time and free fall of material from the valve head to the container
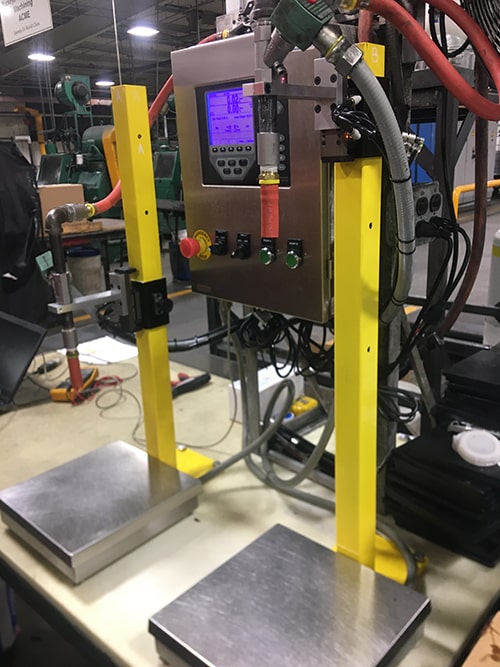
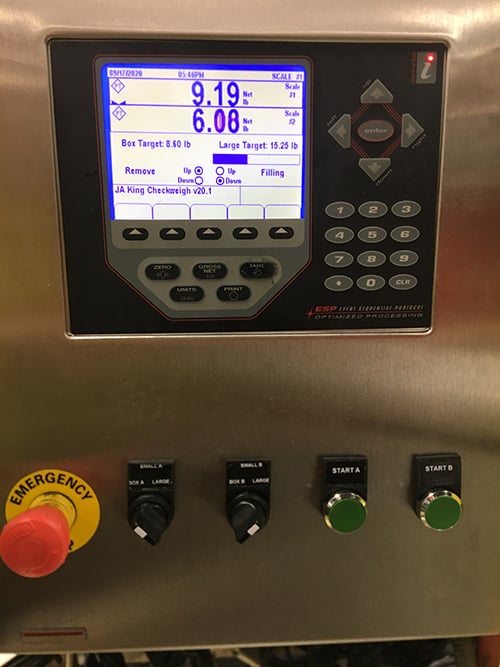
This addresses the following customer challenges:
- The automated filling of the container allows for both scales to be used at the same time while being operated by one person. This cuts the manual labor in half and allows both scales to always be used.
- The intelligence built into the system addresses the customers need to consistently fill at the appropriate weight and prevents wasted product from overflows.
Customer ROI
For this operation, the customer was running 2 shifts a day, 7 days a week. Cutting the manual labor in half saved the customer over $100,000/year in labor. This led to a payback period of less than 2 months for this solution. The savings provided to the customer doesn’t take into consideration the money saved by preventing spills and increasing output by always having two scales operational.
Why Choose Cross
This customer decided to work with Cross Automation on this project for several reasons:
- Cross was able to develop a creative technical solution that the customer could not achieve on their own.
- Cross has the inhouse expertise on automation and measurement allowing them to deliver a solution that other companies couldn’t.
- Cross was able to provide this as a turnkey solution thus taking the development and implementation burden off of the customer. This greatly reduces their risk as Cross Automation becomes responsible for the implementation and success of the system.
- Cross was able to work with the customer to uncover the business challenges and developed a solution that fit inside the payback and budgeting constraints. This created immediate value and a very quick ROI for the customer
Are you interested in learning more about how automating manual processes in your facility can improve efficiency while saving you money on labor costs? Contact us today to speak with one of our automation experts to learn more.