Case Study: Anderson UnderBridge
Cross helps Anderson UnderBridge improve functionality, safety, and efficiency of their equipment
Anderson UnderBridge, located in York, SC, is an Original Equipment Manufacturer (OEM) of equipment used to access the underside of bridges for inspection, repair, and construction. They have partnered with Cross Mobile System Integration on hydraulic and control projects for nearly 15 years. In that time, their control system did not change dramatically. However, when new ANSI A92 standards required that the platform have loadsensing technology, Anderson UnderBridge used it as an opportunity to redesign and improve the entire machine.
Latest Videos
Loadsensing Technology
The primary challenge for the design team was to find a way to accurately measure the weight on the platform without making any major structural changes to the already developed equipment. For this project, Cross brought in the engineering team from J.A. King, another division of Cross Company. “Our engineering team works every day to create custom solutions for complex measurement challenges, so this project was a perfect fit,” said Kevin Hatch, Director of Engineering at J.A. King.
The project required that they measure the distributed weight of the platform to monitor for and prevent an overload which would pose a safety risk. Kevin and his team developed a straightforward yet elegant solution to sense the load. “We went through other solutions before, but the idea that Kevin came up with was simpler, lower cost and more accurate,” said Ben Smith, Director of Engineering at Anderson UnderBridge.
Aside from being simple and low cost, this loadsensing solution design is one that could easily be retrofitted into older units if a customer desired to add this safety feature.
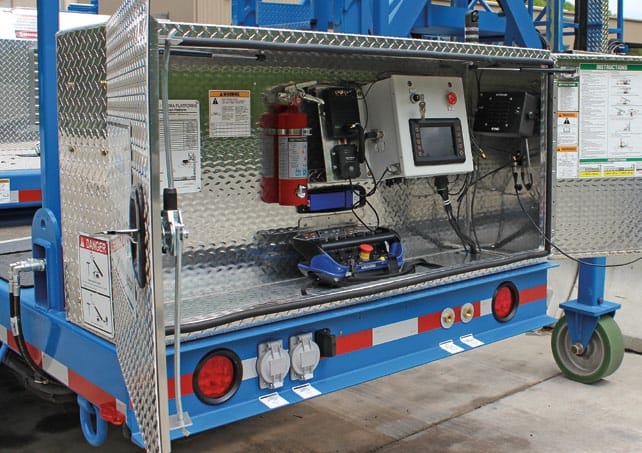
Control System Improvements
In order to support the new loadsensing technology, the entire control system had to be updated. “Through the new software and PLC, the Cross team was able to do more with the controls. The sky is the limit,” remarked Smith. The Cross team moved from the analog switches to an HMI screen that can provide significant feedback to the operator. Smith went on to say that “The user interface is much improved. A seven-inch display graphically identifies system messages and function errors.”
Included in the new system were a range of diagnostics with remote monitoring capabilities for troubleshooting. This is a significant benefit to the service team at Anderson, as it allows them to remotely troubleshoot issues with the machine as well as get alerts when the equipment is due for service. For customers with a rental fleet of these vehicles, it will allow them to better monitor use and maintenance of their equipment.
Added sensors and controllers allowed the Cross team to automate some functions such as auto-stops at set tower positions, and automated outriggers. “The outriggers are standard and intuitive in how they work which eliminates some opportunities for human error,” said Smith of the automated additions.
As an added safety feature, the new control system gives the option to have a platform camera that can be monitored on the HMI by the operator. This gives them visual contact with the person under the bridge in case they experience an emergency but aren’t able to communicate verbally.
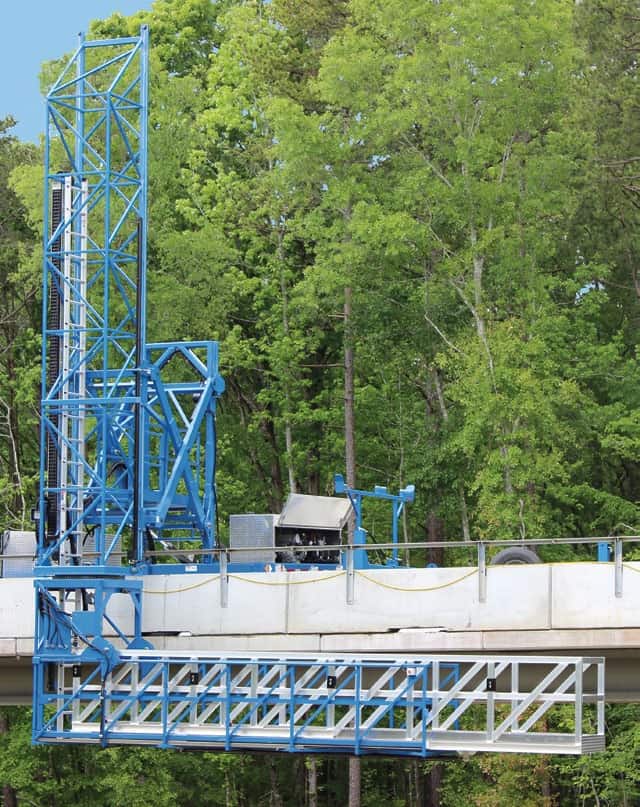
Improved Hydraulic Control
Another major improvement made by the Cross Mobile Systems Integration team on this project was the move to proportional hydraulic valves. Of the update, Chris Vrettacos, lead project engineer at Cross, said that it “gives the user better control over all functions, and allows you to feather critical functions such as easing up next to a pillar.” Being able to better control movements on these crucial and sometimes tricky maneuvers can help operators to place the tower and platform exactly where they need to be without bouncing around which could potentially cause damage to the equipment or the bridge.
From improved control systems and hydraulic control to added loadsensing capabilities and onboard diagnostics, Cross Company partnered with Anderson UnderBridge to develop a better vehicle for their customers. When asked about his experience overall Ben said “the process was seamless from development through testing. Our companies have a really good relationship, and the overall support from Cross has been a huge factor in our longtime partnership.”