Application Note: Actuator for Lifting Heavy Loads in Food Packaging
Cross Automation Helps Food Packaging Customer Find Right Actuator for Lifting Heavy Loads
Occasionally, customers need to lift something heavy and hydraulics or pneumatics are – for one reason or another – not the answer. In these applications, the answer is high force, high thrust electric actuators. Sometimes referred to as electric cylinders, they can replace a traditional hydraulic or pneumatic cylinder. These electric actuators use a servo motor in junction with either ball screw or roller screw drive technology to achieve high thrust forces while maintaining the ability to produce repeatable, programmable motion.
The Application
A great example of such an application is a solution Cross Automation implemented for a food packaging company. The application consisted of multi-axis motion where the electric actuators performed the functions of gates, feeders, and elevators.
Since this machine was in a food packaging plant, electric actuators proved to be a better solution than hydraulic cylinders as they are cleaner and eliminated the risk of hydraulic fluid contamination. Additionally, electric cylinders proved to be a better solution than pneumatic cylinders as they could provide precise motion control at higher forces. Ball screw driven electric actuators can provide over 10,000N of force ( about 2,250lbf ).
In the past, the customer had tried a solution from a manufacturer that produces an electric cylinder where the ball screw system, servo motor, and electric brake are integrated into the same body. This solution, while being compact, proved difficult to implement because the feedback from the integrated servo motor did not match the servo motor feedback used on the rest of the machine. In this case, the customer had to get the manufacturer to assist with the programming of the servo drive and it never quite functioned properly.
Additionally, the integration of the electric brake into the same body caused premature failures of the electric actuator. Over time, when the electric brake was engaged, dust from the brake covered the encoder causing the system to fail. Since this package was integrated, the entire actuator needed to be removed, replaced, and sent back to the factory to be rebuilt.
The Solution
In order to solve the issues the customer was experiencing, Cross utilized Parker Hannifin’s ETH Cylinder, a High Force Electric Actuator. This was the best solution for several reasons:
- This ball screw driven electric actuator from Parker Hannifin has a parallel wrap configuration. It was able to achieve the same high thrust force requirements and fit in the same workspace on the machine. No mechanical machine modifications were necessary.
- While Parker Hannifin manufactures and supplies servo motors, the electric actuators that they manufacture can be configured with motor mounts for servo motors from any manufacturer. So the customer was able to use the exact servo motors being used on the rest of the machine and the feedback communication problem was solved!
- The electric brake failure issue was eliminated by removing the brake from the integrated package. The servo motors with electric brakes were not experiencing any failures on the rest of the machine. If the issue did repeat, the simple solution was to change the servo motor, which is a much easier and less expensive field repair than replacing the entire electric actuator.
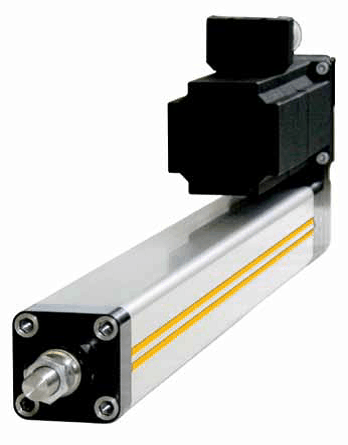
Parker ETH Cylinder
In the end, electric actuators proved to be the right solution for this customer. However, choosing the right actuator can be tough. Don’t struggle with the decision on your own, contact us today. Our automation experts are here to help with your questions.