So, you need to order a new rupture disc? As long as you tell the sales rep what pressure the tag states, the disc size, and the materials of construction, you’ll get an identical disc…right? Unfortunately, it is not quite that easy. Disc manufacturers do a few calculations that are not reflected on the disc’s tag. If you use the pressure data stamped on the tag to reorder, your new disc may not burst as expected. The problem is more pronounced when the disc is reordered multiple times using the pressure data stamped on subsequent discs.
Let’s look at an example:
You tell your sales rep you have an older standard\composite\tension type disc that needs to burst at 100 psig and 72° F . Since it is a standard disc the manufacturer must add a manufacturing range. At 100 psig, the manufacturing range is (-4) to +10 psig and the calculations are: 100(.96) to 100(1.1) equaling a range of 96 to 110 psig. Not knowing where the rated burst pressure may occur, we use the worst-case scenario to be safe. In this case, we will use the stamped burst pressure at 96 psig. However, this type disc is allowed an operating to burst ratio of 80% and 96 psig (.8) equals 76.8 psig. This gets further derated as the disc is allowed a burst tolerance of +/-5% so 76.8 psig (.95) equals 72.9 psig.
You started with a disc that was stamped to burst at 100 psig but discs don’t get stamped until after they are made. Remember in our example, this new one will be stamped at 96 psig. With all the required deratings you end up with a disc that could burst at 72.9 psig.
It gets even worse because the disc is reordered using the stamped pressure from the previous order. This is one reason we often hear customers say, “Our process has not changed but these darn new discs are bursting all the time!”
So how do you avoid this problem?
Instead of giving your sales rep just the stamped pressure on the tag, give him the original manufacturing number that was stamped on the disc. This number (mfg. number, lot number) allows the manufacturer to go back to the original design as a starting point, thus ensuring a duplicate disc from the original order.
Another solution: Reverse Acting Discs
You could also look at a reverse acting disc which allows you to have a zero manufacturing range and then you will avoid the described derating factor. True, a reverse acting disc is more expensive (and a reverse acting holder will have to be purchased) but this disc will allow you to operate at higher pressures closer to the disc’s burst pressure.
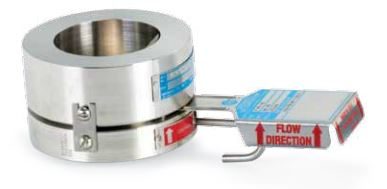
Result: Lower purchasing and maintenance costs which will pay for the increased costs.
Continental Disc offers a comprehensive selection of rupture discs for the chemical, food and beverage, pulp and paper, and power industries. Continental Disc Corporation is a valued supplier-partner with Cross Company’s Instrumentation Group.
Need to order rupture discs? Contact our experts today, we can help you determine the right equipment for your specific application.