The Case for Lubricating a Planetary Gearbox
Using a planetary gear box is pretty common in the hydraulics industry. Several manufacturers of primarily mobile-type equipment use them for applications such as swing drives, drill heads, and drive systems to name just a few. One common way of lubricating a planetary gearbox is to use a “bearingless” hydraulic motor and use the case flow through it to lubricate the internal gears in the planetary gearbox.
We’ll discuss the pros and cons of doing this and give a recommendation of the best way to lubricate a planetary gearbox. In this specific case, we’ll assume our customer is applying a “bearingless” motor and using the case drain off the motor to lubricate a planetary gearbox. The customer is now in the process of switching to a Danfoss/Eaton VIS40 motor with internal case drain and Auburn Gear model 8 planetary gearbox due to excessive gearbox deterioration, wear, and ultimately premature gearbox failure.
Why People Lubricate Planetary Gearboxes Using a Hydraulic Motor Case Drain
It Reduces the System’s Overall Package Size
Due to the “bearingless” design, the motor can come in a much shorter package, enabling the user to utilize it in an area where there are size constraints. This is beneficial in many applications, specifically wheeled / track drives where you don’t have much room for the drive system and / or you are trying to reduce the overall weight of a machine.
Cost
Using the bearingless hydraulic motor design is typically less expensive. Reducing the cost of the motor helps reduce the overall cost of the motor / planetary package.
You Won't Need Two Types of Oil
Gear oil and hydraulic oil are two different types of oil. They have different viscosities and behave differently with temperature fluctuation. Running a “bearingless” design motor eliminates the need of using two different fluids because it allows the planetary to run on the same fluid as the hydraulic system. This can be advantageous during equipment servicing.
Flushing: Why This is Beneficial
Due to the hydraulic motor case always filling the gearbox, and the gearbox always flowing back to tank, the system gets a good flush which allows the gearbox to receive new oil frequently. This is beneficial to the life of the planetary because it removes metal shavings, dirt, and contaminants that can make it deteriorate faster. Flushing should allow the life of the planetary to be longer. Unfortunately, flushing the planetary this way can cause some unforeseen problems.
Why You Should NOT Lubricate Planetary Gearboxes Using a Hydraulic Motor Case Drain
As mentioned above, running the case drain through the planetary gearbox flushes the system, but what a lot of people fail to realize is that the flushed oil can be dirty oil.
The case drain of a hydraulic motor is not only designed to protect the shaft seal from high pressure, but it is also designed to flush dirt and contamination out of the motor. Flushing this oil into the planetary gearbox can cause deterioration of the internal gears. The oil is now filled with contamination, plus the contamination caused from the physical wear and tear of the internal gears that builds up over time, can greatly reduce the life of the gearbox.
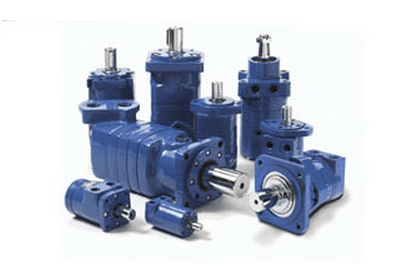
Lastly, it can reduce the overall system plumbing / hosing. If running a “bearingless” motor into a planetary gearbox, you will need a case drain line back to the reservoir / tank from the planetary to allow excess fluid to leave the gearbox. However, running an internally drained hydraulic motor can eliminate the need for a tank line from the motor. The planetary, once filled with gear oil, will be plugged which eliminates the need for a drain line back to tank. This reduces your plumbing / hosing and saves money on manufacturing.
Short Cuts Have Long Term Costs
There are many pros and cons to designing a system where the case flow lubricates the planetary gearbox. Here, the cons far exceed the pros, especially when you are talking about a ~$1500 planetary gearbox. In situations such as this, our team typically designs a system using a standard hydraulic motor. This will require an external case drain hose back to tank or a internally drained motor that doesn’t require an external case drain hose. The benefit from this is having hydraulic oil in the hydraulic motor and gear oil in the planetary gearbox.
This will also allow the planetary to run cooler and reduce gear deterioration because it has the correct oil viscosity. It’s a win-win and will allow each system to run as they are designed, reducing wear and saving the customer time and money on expensive repairs. We’ll acknowledge that there are some negatives to running this method:
- Slight increase in size and plumbing complexity
- Slight increase in initial cost
- Requires proper service (routine maintenance) – which the manufacturer of the gearbox will specify
Using a case drain from a hydraulic motor to lubricate a gearbox is common and in many situations will work fine. However, there are many factors that can affect this including things like duty cycles, operational speeds, oil cleanliness (filtration) and temperatures. It’s important to take all of these factors into consideration and be aware of the consequences before designing a system this way.
Cross mobile systems integration experts have experience working with planetary gearbox setups of all types and in a range of applications so our team can bring that experience to the table to help you determine what might be best for your situation.