In Motion Control, there are many examples of vertical applications, and the examples can vary widely. Whether it’s a packaging gantry or a robot end effector, linear actuators commonly are used to lift loads against gravity. However not all actuators have a brake integrated into the vertical actuation. This may lead some to question when a brake would be required. The answer is not always black and white, but a few common sense rules can help one decide on whether one is needed or not.
Let’s start with a list of the different types of actuator drive types that we see in an average industrial environment. The actuator types are listed in order from the safest option against a falling load to the more risky options, which almost always require brakes regardless of the safety concerns.
Types of Veritcal Load Actuators
Leadscrew Actuators
- Safest
- Brake can be applied to the motor or drive shaft
- Efficiency ~ 50 %
- Short leads
- Backdrive ability low
- NO FREEFALL
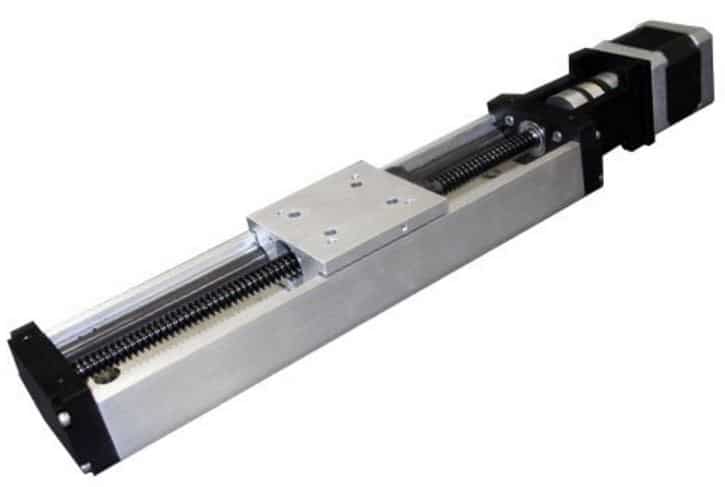
Bishop Wisecarver LeadScrew Actuator
Ballscrew Actuators
- Safe
- Brake can be applied to the motor or drive shaft
- Efficiency ~ 90 %
- Short pitched help with a falling load
- Backdrive ability much higher
- NO FREEFALL
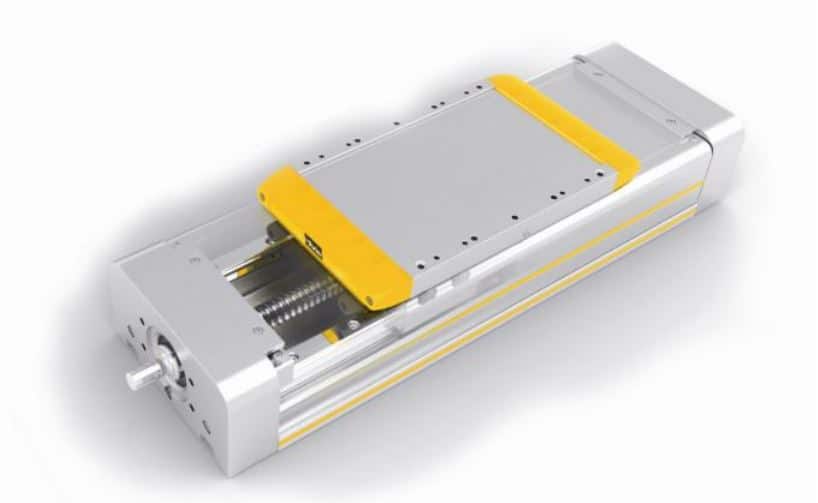
Parker Ballscrew Actuator
Belt Drive Actuators
- Least Safe
- Brake can be applied to the motor
- Efficiency ~ 95 %
- Potential for Belt Breakage
- Potential for freefall with servo power
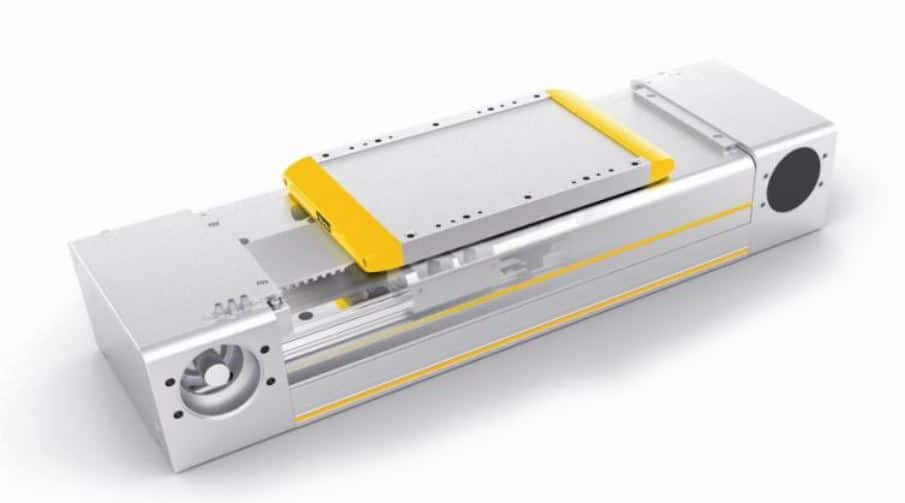
Parker Belt Drive Actuator
Cross offers a range of linear actuators
Where To Apply A Brake To A Vertical Load
A brake can be applied in three primary locations of a linear positioner in the overwhelming majority of applications:
- It can be directly applied onto the linear drive unit – i.e. the ballscrew or the belt drive pulley shaft, which would be the optimal location as far as fail safe operation. This eliminates a crucial mechanical failure point: the coupling between the drive unit and the servo motor shaft.
- Brakes can be applied onto the linear bearing, such as a linear square rail. This would be the second safest option for applying the brake and can actually prohibit a belt drive from freefalling. This is achieved because the square rails bearing blocks are rigidly fixed to the carriage of the linear actuator.
- The least safe place to attach the brake would be on the servo shaft itself. This option does not prevent load freefall due to the chance of coupling failure. Just because this is the least safe option does not mean that it is not safe. It ensures better protection against load freefall than nothing at all!
Vertical Load Brakes
Power-On Brakes
These brakes energize the armature of the brake allowing it to clamp the friction material onto the moving shaft once it receives power from its power supply, which would be independent from the servo motor power bus. This brake control design would not be properly used in an application to prevent a load from falling since its power supply would have to rely on a separate control signal in an emergency servo power loss situation. More than likely this brake would be used for an application specific process during the normal application cycle.
Power-Off Brakes
The inherent design of this brake is to actuate once the power has been removed. This can usually be tied into the same power bus as the servo drive power bus and therefore it will lose power at the same time that the drive loses power. This brake usually has a spring assist which forces the armature of the brake to press against the shaft causing it slow to a stop when power is removed from the brake. However when power is applied, the electromagnetic field pulls the armature off of the shaft causing it to spin freely. This design makes the brake failsafe in an emergency servo drive power loss situation.
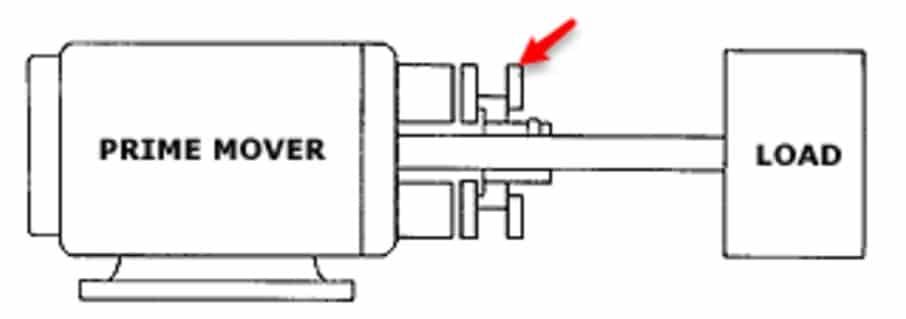
Example of flange mounted power-off brake directly attached to the load shaft. This represents the safest application of a brake in a vertical situation.
There are many applications which require brakes. However, it is not always easy to decide which brake or which drive technology to use in a vertical application. There are exceptions to every rule due to a variety of factors, such as environmental concerns or the physics of the movement of the application, which could require a less safe drive technology to be used.
The actual sizing of a mechanical brake is another discussion that needs to be considered to ensure that the brake applied has enough torque and power to stop the dynamics of a particular load. It is important to consult an expert in the motion control field to assist with weighing the options and the risks encountered in each application. Our team can help you decide when to use a brake and where to apply them on the mechanical system. We have experience working with linear actuators in a range of application and can help your team ensure safe and efficient operation.