The following is an excerpt from a full white paper by Paul Carter, “Building and Operating Smarter Machines Using Automation Technologies” which can be downloaded here or at the bottom of the page.
Introduction and Objectives
What is a Smart Machine?
It is most likely the goal of every company to have Smarter Machines. But what is a “Smart Machine?” Ask 100 people that question and you will probably get 100 different answers. In my opinion the definition of a Smart Machine is pretty simple – a machine that can:
- Provide information about how well it is performing.
- Offer diagnostic information about its operational status.
- Provide operators with instructions for maintenance and operations.
Why do we care about Smart Machines?
This is a little different than “Smart Manufacturing” or “Smart Processes,” where the machines can provide information centered on the output or production performance of the machines. (Concepts such as OEE, or Overall Equipment Effectiveness, have been around for decades and these capabilities continue to improve with solutions enhanced with new capabilities and solutions.)
However, a big part of creating Smarter Manufacturing processes is gaining insights into how the machines themselves are performing and what can be done to improve their productivity, availability, and efficiency within the manufacturing process. Smart Machines can provide this insight.
This document is a broad overview of how you can implement and create Smarter Machines. This is by no means an all-inclusive guide, as it should be expected that many new solutions for implementing Smart Machines have yet to be introduced and many solutions are available that space is too short to include in this webpage.
The Role of Data in Smart Machines
Smart Machines require information and information comes from data. The data is available in all of the devices located throughout the machine or from operating parameters that could possibly be measured but are often omitted from the original design of the machine. Examples include:
- Current consumption from servo and inverter type drives.
- Electrical energy consumption and compressed air usage from the machine.
- Actuator response times.
- Encoder feedback from various motion positions within the machine, etc.
With data, we will usually find that data needs to be stored or logged. Building Smarter Machines can often require that historical information about the manner in which a machine operated in the past (for example, when it was initially commissioned) compared to how it is currently operating. This can often be the key to determine if a machine is performing in an optimal or Smart manner. In the building automation industry, the practice of continually monitoring machine operation is called continuous commissioning, and leads to significant improvement in the operational efficiency of a building and allowing building maintenance teams to work in a much more efficient manner.
Data can be recorded from almost any type of machine. The two most common locations to record data are Microsoft SQL, which is a database application (for many applications these are free, such as Microsoft SQL Express), or a class of software products called an Industrial Historian. An Industrial Historian is a software application designed specifically to log or record data for industrial and building applications. Many of the most prominent industrial software vendors will have an industrial historian product available to meet these needs. One area where industrial historians really shine is with the logging of what is termed
timed-series data. For example, a motor current or temperature that is logged every five minutes, with the associated time stamp of the data sample, is referred to as timed-series data.
IoT and Smart Machines
If your company desires to utilize an IoT approach to creating Smarter Machines, then the data will be logged (collected) using a 3rd party IT provider (cloud service) such as Amazon Web Services, Microsoft Azure, or IBM. Some of the industrial software vendors mentioned above will have recommendations forusing their products within a cloud-based environment and will often install their products in the cloud, so using a cloud service is essentially no different than an on-premise IT installation other than who provides
the IT services.
Listed further on are a number of ideas and areas for certain aspects of a machine that can be monitored. Some of the areas that can be monitored are relatively high speed and will have fast changing data. Any data point needing to be monitored in less that ~1-second time increments will need to be initially collected in the machine’s Programmable Logic Controller (PLC). Most software-based data collection systems and/or SCADA (Supervisory Control and Data Acquisition) systems will not reliably capture data that is changing in less than 1-second increments. A PLC can capture and perform basic calculations in very short time increments and can easily capture time increments as fast as 1 milliseconds (1/1000 of a second).
You have data. What does it say?
Once you begin to log various data, something has to be done with the data. The simplest next step is to present time-series data to key personnel in the form of trend graphs. The trend graph will show changes in values over time and is an easily understood visual that allow key personnel to see changes in performance. When this type of data is stored for extended periods of time, it is also very easy to begin to understand when a piece of equipment is no longer operating within expectations or when a piece of
equipment has changed from its original design or installed performance.
The image below is representative of how trend graphs can display operation over time and they can easily display how various equipment performs in comparison to each other.
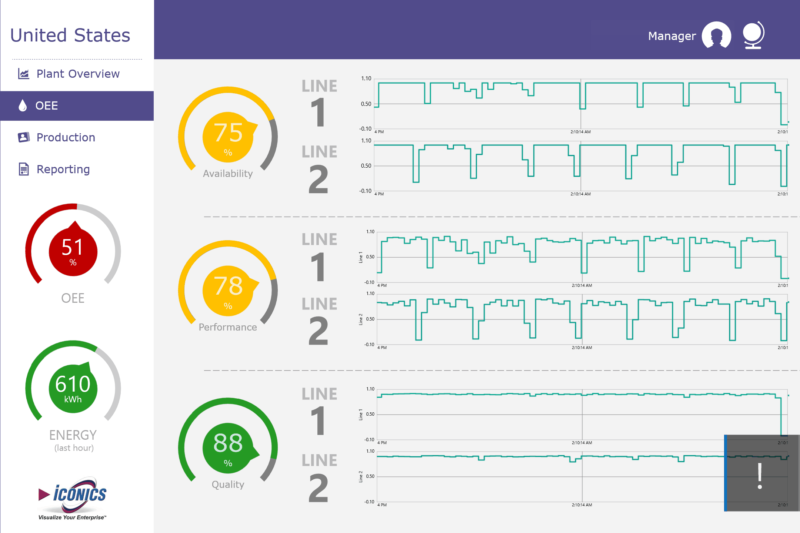
Next, add additional context and/or decision making to the values of data being collected. This can be done using several well-understood methods:
- Create something called an Alarm that will provide an indication when something has changed beyond a predetermined limit.
- Consider Statistical Process Control (SPC).
- Apply Fault Detection & Diagnostics (FDD).
- Utilize Machine Learning.
Regardless of where the data is stored, a key and essential element of any Smarter Machine initiative is to consider who the consumers of the information will be and how will they get the information.
You have data. How is it presented?
Once data is collected and initial analytics (alarming, SPC, FDD, etc.) are performed, this information needs to be delivered to the personnel best able to act on the information. The information also needs to be delivered in the most effective fashion for your facility. In today’s manufacturing environment, information might be delivered to computer screens, large format displays hanging on the factory floor, to tablets, to smart phones, to wearable devices (smart watches, hands-free tablets, headsets, etc.), or information might be delivered in the form of reports.
Do not underestimate the power of Microsoft Excel. Excel is an immensely powerful tool for processing, calculating, contextualizing, and presenting information. However, I will make note that any use of Excel should be automated. Reports should be automatically populated with data, reports should be run automatically, and should be distributed automatically (email, printed, stored on a server, etc.) Reports that take significant manual intervention to complete will ultimately lose value – automate the reporting functions!
Ideas for Creating Smarter Machines
Below is a list of ideas which can help you create smarter machines for your organization. For a full description of each, please download the entire whitepaper here.
- Utilize embedded web pages from smart components: Leverage the capability already existing in the components installed on the machine, especially with new machines.
- Monitor and historize process sensor data: Monitor process sensors (flow, temperature, pressure, etc.) for change over a period of time.
- Monitor pneumatic actuators for proper operation: Monitoring cycle time can identify immediate performance issues and by
tracking this value over time can reveal a slowly degrading performance.
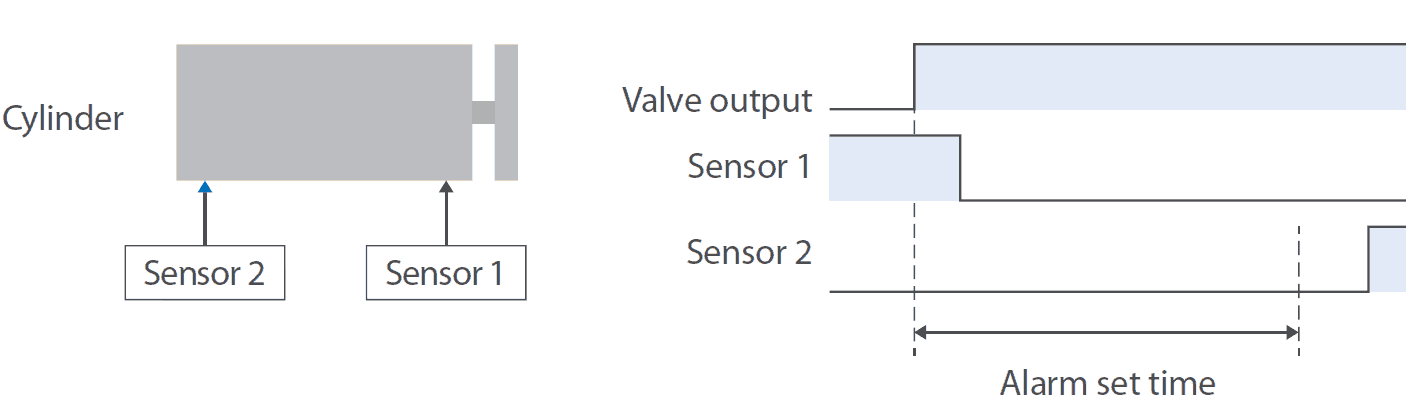
- Monitor electrical actuators & mechanical actuators in a similar fashion as pneumatic actuators: Electrical actuators provide similar functions as pneumatic actuators but will have a stepper motor or servo motor attached to provide the energy source vs. the compressed air used for pneumatic actuators.
Monitor the torque output for servo motors: Monitoring torque output can help to identify when conditions surrounding the load being driven by the servo motor has deteriorated from the original design performance.
- You can similarly monitor robots: A robot can also be looked at as a six-axis motion control system. Each robot axis has a servo motor and usually some type of a gearbox.
- Monitor all electro-mechanical electrical components for total operations count: Once an electro-mechanical component exceeds it rated number of operations, the likelihood of a potential mechanical failure increases.
- Monitor 3-phase induction motors: Measure each of the phase currents being consumed by the motor and apply conditioning monitoring sensors to measure vibration, temperature, and current.
- Monitor the energy consumption for the machine, both electrical and compressed air: Monitoring the use of these energy sources helps build a Smarter Machine because changes in the use of these energy sources can be an early indicator that the machine is not operating at peak levels of performance.
- Utilize the protocol of IT (SNMP): Most of this equipment has a communications protocol included with the product that can be leveraged to understand the performance of this networked equipment.
- Implement sensors that have diagnostic functions: Smart Proximity sensors can detect differences in the position of the object being sensed. Photoelectric (optical) sensors can also be deployed to provide feedback about the operational status.
- Monitor circuit protective devices for operation
- Monitor power supplies
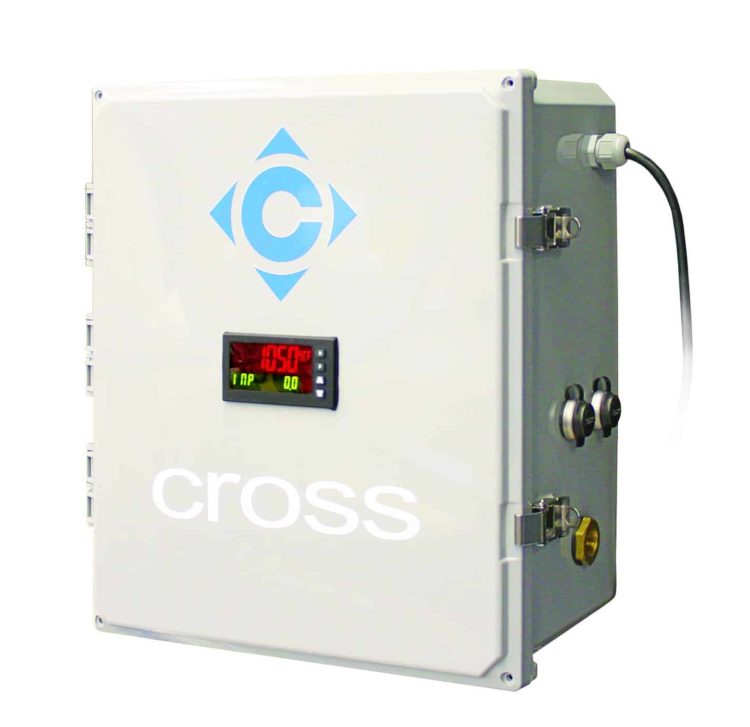
Cross’s compressed air flow monitor can help establish a baseline for compressed air consumption
How to get started
The majority of this document has been about ideas for monitoring various sub-components within a machine, but the question you may have is what steps to take to implement an IoT approach to create Smarter Machines. Below is a series of steps to take for moving forward:
- Assemble the key personnel on your team and determine if creating a Smarter Machine approach for your facility makes sense. Determine who will lead the effort.
- Take an inventory of your machines and take note of what available communications interface may be available on the current machine controller. Most machines utilize a controller called a Programmable Logic controller or a CNC (Computer Numerical Control) controller.
- Engage with the maintenance team to gather information about repairs and work orders for each of the identified machines. This information can be the basis for beginning to build smarter machines so the previous failures can be predicted and either eliminated or corrected before a downtime event occurs.
- If your machines are commercially built by a machine builder, contact that machine builder to see what ideas and/or assistance they may be able to offer on your journey to Smarter Machines. If your machines are custom to your facility, then it will dependent on your team to identify areas that can be monitored to create a Smarter Machine approach.
- Schedule meetings with potential suppliers of industrial software products to provide the data logging, analytical functions, and information delivery to key users within your company. The industrial software market is very broad and has many potential suppliers, some of which might have some very good ideas for how they can be of assistance.
- Get started. Understand that creating Smarter Machines is a process and the sooner you get started, the quicker the potential benefits.
As mentioned earlier, the building automation industry has adopted some of the techniques outlined and the results are truly impressive. Many large building owners, such as universities, are completely revolutionizing how they maintain the mechanical equipment in the building and are seeing dramatically lower operating costs as a result of applying some the approaches discussed here. If you would like to increase efficiency and dramatically reduce your operating costs, click below and start a conversation with Cross today!