Are You Replacing Valves Too Often?
Are your valves lasting a year or less in your application?
If the answer to this question is “yes”, then you may have the wrong valve for your application. There are several critical factors to consider when selecting a valve. Selecting the right valve for your application conditions can help you to reduce your risk of downtime which will save you both time and money in the long run. These are some of the top factors to consider. If you can provide your valve supplier with this information they will be better equipped to find the right valve for your application.
Temperature
Knowing the temperatures that your valve will experience is important for seat selection and body material selection. For our purposes, anything above 450° F is considered high temperature and would require a metal seat. For low temperature applications (below 450° F) you can use a soft seat material such as a teflon (PTFE) or a reinforced teflon (RTFE). We do however have some manufacturers who can solve some high temperature applications (425°-525°F) with a soft seated teflon copolymer derivative material. This is helpful, as soft seated valves tend to be less expensive than their metal counterparts. If your process runs at very cold temperatures (down to -320° F) you will also need special valves. Cross has valves capable of handling these extreme temperatures for cryogenic service.
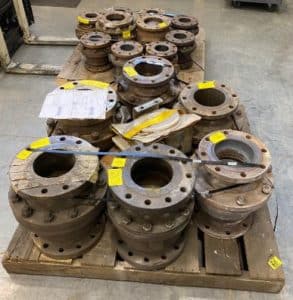
An important thing to remember is that there can be significant temperature swings within your process that can impact the performance of your valve. For instance, if your normal process temperature is 200° F it could fluctuate from 150°-300° F within a short period of time. This is why you need a valve with good seating technology. This is also true for applications where the process lines need to be cleaned between runs. If you are using steam to clean the lines, the high temperature steam could melt your valve components.
Another temperature related consideration is whether or not your material could solidify if the temperature drops. If this happens the material can build up around the ball and seat causing damage. Examples of materials that could do this include monomers, butadiene, and styrene. In these cases, you may need a steam jacket or heat tracing on the piping around the valve to ensure the media continues flowing at a steady rate.
Pressure
Knowing what is happening before and after the valve in your process is critical. When specifying a valve, it’s important to have both the upstream and downstream pressure. This information will give you the pressure differential going through the valve. Not taking this data into consideration can be a significant opportunity for failure. If there is too much of a pressure drop within the valve it will speed up the flow and cause serious damage to your equipment. It’s very much like putting your thumb over the end of a garden hose. When you increase the outlet pressure with your thumb, the velocity of the water coming out is increased.
Line pressure is also an important factor to consider if you are automating the valve. Knowing this information will help in sizing the valve and actuator. The higher the pressure is, the more torque you will need to turn the valve.
Media
As you might imagine, the media that will be flowing through your valve can have a significant impact on the material selection for your valve. You want to make sure that what is flowing through your valve is compatible with the valve materials.
For instance, will the media cause cavitation? Cavitation is what happens when air bubbles pop within the media, causing tiny explosions that can eat away at the valve over time. This is caused when the pressure and temperature of the process drop below the vapor pressure of the liquid. Examples of a cavitating material would be water near the outlet of an improperly sized rotary pump or if there is too much differential pressure across a control valve. When there is a risk for cavitation you can add valve anti-cavitation trim or a diffuser plate to help protect the process from too much pressure drop.
Erosion may be an issue. For instance a sand and water slurry or any process that is “gritty” may eat away at the valve and pipe components. Rubber lined or Teflon Lined valves and piping may solve your erosion issues.
Certain chemicals can also cause corrosion and damage to the valve if the materials are not compatible. For instance, chlorine could require a valve made of an exotic alloy like Monel or Hastelloy depending on how high the water to chlorine ratio is in your media. If the valve will encounter a material like hydrogen peroxide you will want to passivate the valve to avoid stress cracks. By passivating the metal, you improve the tensile strength of the material by filling in imperfections which could allow hydrogen peroxide to seep into the metal.
Submersion / Buried Service
Finally, you need to know if your valve can / will be submerged under water or buried in the ground. If so, you will want to make sure you use the proper actuator or add a stem extension to ensure the actuator will stay above the water line / ground level. If your valve is going to be buried underground you will need to decide if it’s ok to bury the actuator with the valve or if you need to have regular access to it. If you bury the actuator, will you need a special permit for a person to go into the pit to work on the actuator as needed? If underwater, will it be temporary or continuously submerged?
Takeaways
As you can see there are a number of considerations to take into account when choosing the right valve for your application. Don’t forget that if your application conditions change after your valve is installed, you may need to change your valve type as the new conditions may not work with the valve you have in place. At Cross Process Solutions, we have a team of experienced valve experts who are available to help you analyze and review your process conditions in order to find a suitable valve.
Our team can also help with start up and installation to make sure that you have proper gasketing and fastener links so your valve works as intended. In addition, we offer special cleaning services that ensure your valve is oil and grease free for applications such as oxygen service.
Having the right valve in place can reduce your risk of downtime. Contact us today to talk about your specific needs and find the perfect valve for your application so you can avoid replacing equipment more often than necessary.