Supplier Resource
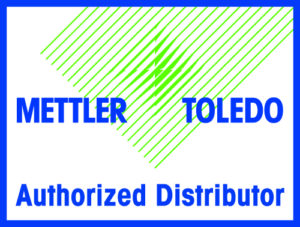
This is an extract from a white paper from Cross Company supplier, Mettler Toledo, which discusses hazardous area regulations. Here, it is focused on the North American market.
This document is not an installation guide and should not be used as a reference for installation instructions and control drawings.
Safety Competence: Hazardous Area Regulations and Standards
Weighing equipment and control terminals intended for use in explosive atmospheres must comply with extensive regulations, standards and directives before they can be traded and operated worldwide.
Safety is crucial for industries that operate in potentially explosive environments. Standards and regulations play an important role in these hazardous manufacturing venues by specifying the framework of conditions which guide both equipment manufacturers and operators to help ensure safety in manufacturing.
This paper provides insights into safety regulations and standards for hazardous area use. It explains their relevance for the processing industries and also highlights how they can be applied when choosing weighing equipment that will be used in hazardous locations.
1. Why Regulate Hazardous Areas?
Globally harmonized standards and mandatory safety regulations would help facilitate the free movement of goods by identifying a uniformly recognized framework. However, no truly globally recognized schema yet exists.
Increasing numbers of accidents in processing industries globally are highlighting the importance for comprehensive, harmonized safety regulations and guidelines.
Safety problems related to the design and use of electrical equipment in hazardous areas have led authorities to impose strict rules. It has also elicited awareness of safe-equipment design.
Equipment design is regulated by regional notified bodies. National differences in technical requirements and approvals for explosion-protected equipment make significant demands – primarily on global companies. They require considerable transparency in development and testing.
Standards and regulations governing equipment used where there is explosion risk cover everything from risk assessment and classification up to the product certification and employee protection requirements.
Recognized authorities work to develop uniform standards on both a national and international scale. However, historical and country-specific developments have meant that many safety concepts – including explosion protection – do not yet have a corresponding global standard in place.
Whether looking country-by-country or seeking to understand international standards, manufacturers of equipment applied in hazardous areas are responsible for designing and producing equipment in accordance with the appropriate standards. The equipment must be certified and comply with regional or country specific regulations where products are to be shipped. These companies are confronted with different protective measures and operator obligations in each case, and it is important that they understand and operate in compliance with relevant rules.
In addition, equipment purchaser is responsible for the safety and protection of their workers. Therefore, those companies must ensure that the equipment they select is designed in accordance with the appropriate safety regulations and standards. They are also responsible for training of their employees to safely operate equipment installed in hazardous areas.
2. Global Regulations for Electrical Equipment
There are two major global organizations that set hazardous-area standards globally.
One is the International Electro-Technical Commission (IEC). This is the premier international standardization organization for electric, electronic and related technologies. The aim of the IEC is to harmonize the many different standards and regulations throughout the world and to remove trade barriers for related products. For example, the IEC 60079 standards are related to the general requirements for hazardous areas. The IEC system is followed in Europe, Asia, Australia, Africa and some other regions.
The second system is the North American system with the National Electrical Code (NEC) Guidelines, which are published by the National Fire Protection Association (NFPA).
The requirements for hazardous areas and safety in the workplace are defined in ATEX directives in the European Union and in NEC articles in the USA. To promote the harmonization of standards, many local regulatory bodies worldwide have totally or partly adopted to the IEC standards. Even the NEC and the Canadian Electrical Code (CEC) are now partly recognizing the IEC/CENELEC hazardous-areas certification system (Figure 2).
3. USA and Canada Regulations and Standards
Despite the fact that basic explosion-protection principles are similar all over the world, there are some differences in the techniques and systems which have been developed in North America. The main differences from the European IEC system are that they include classification of hazardous areas and equipment design and installation requirement for electrical equipment in potentially explosive atmospheres (Figure 7).
Classification of Hazardous Areas – NEC System
In the USA, all regulations related to manufacturing facilities at risk are found in the National Electrical Code (NEC) Handbook. The articles 500, 501, 502, 503 define the requirements for classification of hazardous locations into Classes, Groups and Divisions.
In the 1990s, the National Electrical Code has developed the article NEC 505 which classifies hazardous locations of Class I Division 1 and 2 in three Zones (Zone 0, 1 and 2). This classification is based on the IEC/ CENELEC Zone classification system and is developed as an alternative classification to the Division classification system of NEC 500.
According to NEC 500 hazardous locations are divided into Substance Classes I, II, and III depending on the type of material present. Table 5 shows the classification of the hazardous locations according to NEC 500 – 505 articles.
- Class I locations are those in which flammable gases or vapors are present in the air in quantities sufficient to produce explosive or ignitable mixtures (NEC 501).
- Class II locations are those that the dust is present in quantities sufficient for a fire or explosion hazards to exist. To be considered a “dust” the combustible material must exist as finely divided solid particles of 420 microns (0.017 In) or less (NEC 502).
- Class III locations are those are hazardous because of the presence of easily ignitable fibers or flying’s (NEC 503).
Article NEC 500 is used the classification of Class I and II in two Divisions – Division 1 and Division II. The classification depends on the likelihood of the flammable or combustible material being present in ignitable concentrations.
Each Class is also divided into the material Groups A, B, C, D, E, F and G. Article 500-3 defines the classification of the of Substance classes into Substance groups according to their properties. Table 6 presents this classification.
Article NEC 506 is an alternative classification system to Class II and Class III that is based on the Zones of the International Electrotechnical Commission (IEC). Zones 20, 21 and 22 apply to combustible dusts or ignitable fibers or flyings. Combustible metallic dusts are not covered by NEC article 506.
In Canada, the Canadian Electrical Code (CEC) defines related regulations. Section 18 of CEC and Annex J defines the requirements for hazardous-area classification. The CEC system accepts the IEC/CENELEC Zone classification system and maintains Class and Division standards in a separate Appendix.
The CEC includes the following rules:
- Rule 18-000 – General Class I, Zone and Class II and III, Division requirements
- Rule 18-090 – Specific Class I, Zone 0 requirements
- Rule 18-100 – Specific Class I, Zone 1 and 2 requirements
- Rule 18-200 – Specific Class II, Division requirements
- Rule 18-300 – Specific Class III, Division requirements
- Appendix J – General and Specific Class I, Division requirements
The NEC and CEC for Canada can be viewed as starting point from which all subsequent aspects of North American hazardous Installation Code (Haz Loc) are derived. The NEC codes include all details on equipment construction, performance and installation requirements as well.
Equipment Construction and Installation Requirements
NEC articles 500 to 504 require equipment construction and installation that ensure safe performance under conditions of proper use and maintenance. Different standards and regulations apply to the construction and testing of explosion protected electrical equipment.
The standards regulating electrical equipment design and construction are developed by Underwriters Laboratories Inc. (UL), Factory Mutual (FM) and International Society for Measurement and Control (ISA). In Canada the construction designed is regulated by the Canadian Standards Association (CSA).
NEC Marking
Similar to European ATEX Guidelines/NEC System, these Systems require marking of electrical equipment to show the environment for which it has been evaluated. The marking includes the information specified in the NEC 500.8 (C1-5) (Figure 8).
Example of the equipment marking according to NEC 505 is shown in Figure 9.
4. IECEx Standardization Scheme
IECEx is a single global certification framework based on IEC international standards, and it is fast becoming the preferred route for international safe certification of products for use in hazardous areas. It caters to countries whose national standards are either identical to those of the IEC or else very close to IEC standards. IECEx certification is a global concept, which reduces trade barriers caused by different conformity assessment criteria in various countries and opens up new markets with a worldwide certificate.
The scope of IECEx is defined by the standards issued by IEC Standards Committee TC 31. The general requirements for electrical equipment are covered by the IEC 60079-0 which defines a precise process for testing and certifying new products and appoints authorized bodies to carry out these tasks. The certification system is extended to cover maintenance and repairs for explosion-protected equipment.
A third aspect of the IECEx concept defines the expertise required by specialists working in areas at risk of explosion.
5. Bringing IECEx, ATEX and FM Together
A common route to compliance is to use pre-approved products in the specified manner. “Notified Bodies” such as Baseefa, Sira, TUV, Dekra Exam provide a conformity assessment to gain additional certification. Unfortunately for global export this is not always sufficient.
Global export requires an international solution that ensures equipment designs are acceptable in any part of the world without significant modification. The approach would use recognized practices to achieve a common acceptable level of safety with the goal of facilitating free trade across all major world markets.
Table 7 highlights the similarities and the differences among the three major global standards.
6. Weighing Equipment Safety Requirements
Intrinsically safe weighing systems for hazardous area use consist of several components such as weighing platforms, control terminals, power supply interfaces, communication modules, safety barriers and usually a wide range of peripheral equipment such as PCs, printers or even data communication systems. Depending on weighing system requirements, the system must comply with not only the legal directives but also provide an appropriate safety concept that fulfills the requirements of numerous standards and regulations.
Choosing the right equipment depends upon application requirements as well as hazardous area classification. It is crucial to be aware of the possible risks and safety concepts. The figure and table below show the different weighing system components and related risks, and highlights the corresponding safety design concept (Figure 10, Table 8).
METTLER TOLEDO designs and develops the weighing solutions for hazardous areas according to the global standards and regulations in mind. All components of the weighing system follow the general requirements concept of IEC EN 60079-0 / FM 3600, UL 60079-0 and CSA 60079 certificates as well as the other certificates to ignition protection design and to the mechanical concepts. Testing and certification is done by certified notified bodies such as Dekra in Europe and FM in USA. All components of the system, therefore, comply with ATEX, IECEx and FM certificates (Figure 11).
7. Responsibilities of Involved Parties
Everyone involved in construction, installation, operation and maintenance of electrical equipment for hazardous areas must work together to ensure safety in areas at risk of explosion.
User
The user of the weighing system is responsible for the safety of their equipment and must comply with the relevant national laws and standards. Their primary duty is to assess the explosion risk in the facility and specify hazardous areas. These form the basis for the protective measures to be taken and for selecting appropriate equipment. The manufacturer must also ensure that all employees comply with protective measures and, if necessary, provide appropriate training. Additionally, the employing manufacturer is responsible for correct installation and commissioning. Regular maintenance and testing must be carried out to ensure safe operation of the weighing equipment. In the case of an equipment move, the new location must also be checked to ensure if it is appropriate for the equipment.
Manufacturer
The equipment manufacturer is responsible for ensuring the weighing system is eligible for trade as intended. The duty of the manufacturer is to comply with the laws and directives of the country in question and carry out the appropriate testing and assessment procedures, ensuring that the relevant equipment markings and documentation are in line with the appropriate standards and regulations. In Europe, for example, equipment must have the CE and Ex markings as well as installation and operation instructions. An appropriate quality assurance system must be in place to ensure that every piece of equipment is produced using tested construction methods.
Notified body
Notified bodies are the neutral and independent organizations whose main task is to carry out conformity assessments on products intended for free-trade movement.
8. Summary
Many standards that are applied worldwide are based on other standards. While standards are similar throughout the world, there is still no uniform global standard. Therefore, products sold in different countries also have different certifications for different explosion-risk environments. Furthermore, symbols on the respective labels differ. Many countries in Southeast Asia and Latin America have no local standards of their own and accept international and national IECEx, ATEX and FM approval; however, locations such as China, Korea and Russia do have local certification requirements that must be adhered to, although primary certification schemes may be accepted for most purposes, depending on nation.
METTLER TOLEDO develops weighing equipment for hazardous areas and obtains approvals on the global level, e.g. IECEx, ATEX, and FM, which are accepted in most countries.
Learn more about hazardous area regulations, standards and how to apply them to choose the right weighing equipment: www.mt.com/haz-safety
© 2013 Mettler-Toledo AG
Want to share or download for later reading? Here’s a downloadable PDF copy: Safety Competence: Hazardous Area Regulations and Standards
Cross is an authorized Mettler Toledo distributor in certain territories. In all of its areas, the scale experts at Cross work with our customers to ensure they have the correct equipment for their particular hazardous area application. Contact us today to discuss your requirements.