Rock Able | November 18th, 2016
As an original equipment manufacturer (OEM), you take pride in turning out a quality piece of equipment and your customer expects quality and trouble-free operation. Many problems associated with new equipment are a result of hydraulic system contamination, but it doesn’t have to be that way. Here is how you can turn out better-functioning and more reliable hydraulically actuated equipment.
It’s no secret that over the years mobile hydraulic systems have become much more complex. In the old days, when you used a gear pump and a manual directional valve to control actuators, systems were much more tolerant of contaminants and the risk of catastrophic failure was much less. Today’s mobile systems are much more complex, the components have tighter tolerances, they must operate with less stiction in order to perform properly, and are much more susceptible to catastrophic failure in contaminated systems. In other words, having clean hydraulic fluid is imperative and it starts at the OEM.
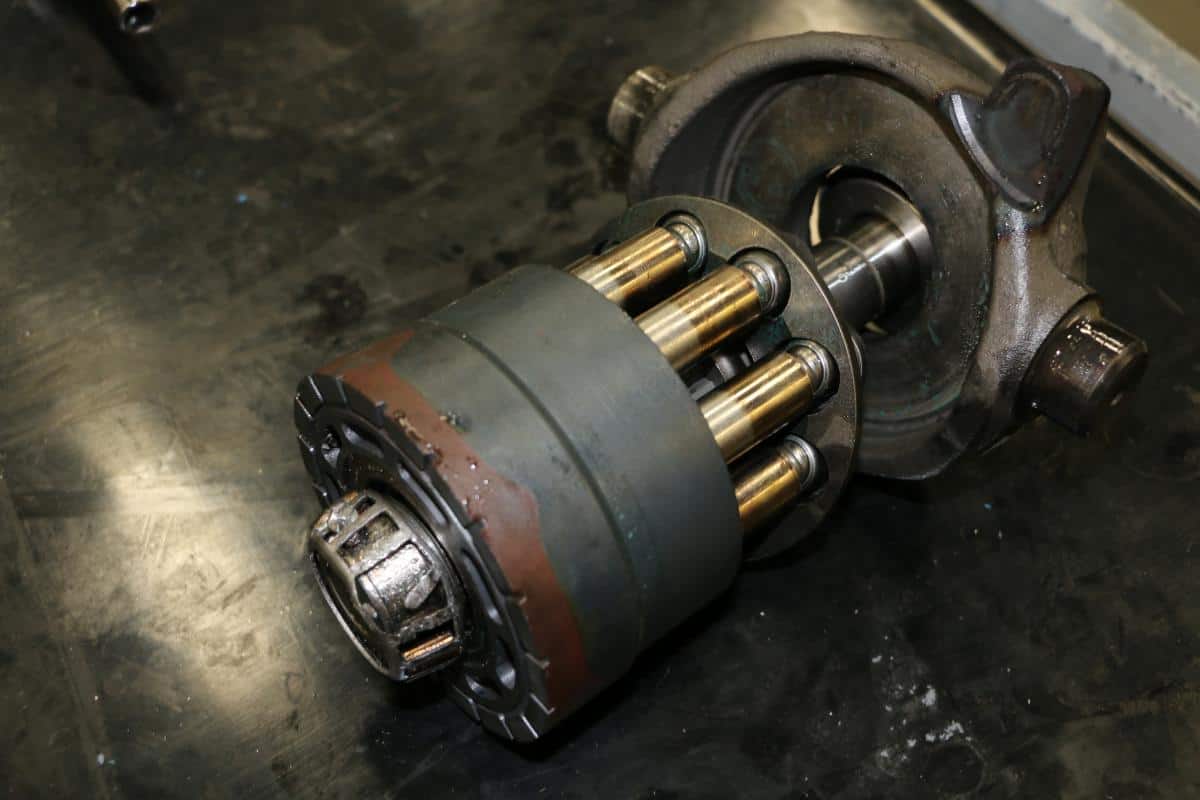
There are three basic sources of contamination in hydraulic systems.
- Built-in contamination includes the metal particles from grinding, drilling and cutting, welding slag, cleaning rag fibers, particles inside tubing and hose from the cutting process, general shop dust, and more.
- Generated contamination is made up of particles caused by wear of the hydraulic components. This can be caused by built-in contamination, corrosion, oxidation, or improper fluid conditions. This can be greatly reduced by eliminating the built-in contamination and employing proper filtration, cooling, and system design.
- Ingested contamination is made up of particles that enter the system through breathers, openings, worn cylinder wipers, improperly sealed covers, etc. This contamination enters the system as it is being operated in the field. This can be greatly reduced by proper system design and maintenance practices and is the responsibility of the owner and operator.
As an OEM, you can greatly improve your machine’s performance and reliability by addressing the issue of built-in contamination and proper filtration/system design. In the short run, this will cost you a little extra money, but in the long run, it will pay big dividends in reduced warranty and repair costs and improved machine performance and customer satisfaction.
Cleaning Your Hydraulic Components
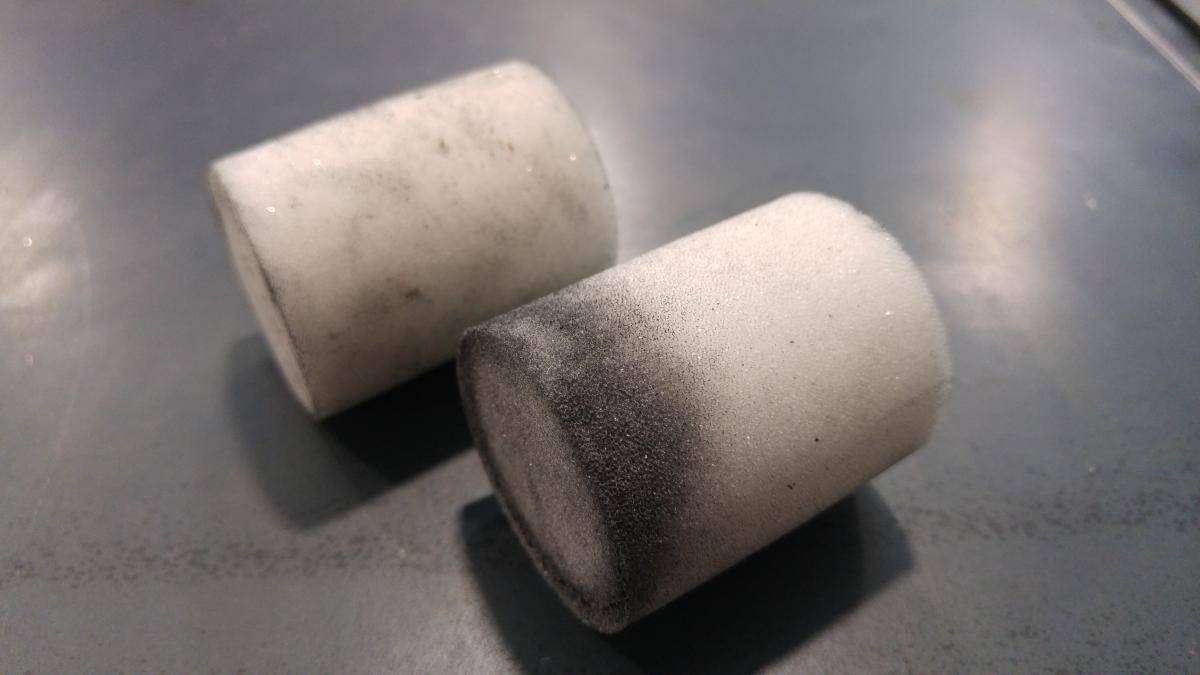
To start with, hydraulic system assembly should be performed in a clean workspace. If there are other fabricators grinding metal in the immediate assembly area, it will be impossible to keep those contaminants out. Next, the reservoir must be completely cleaned after all welding, drilling, grinding etc. is performed. A steam cleaner or high-pressure washer works well to dislodge trapped contaminants and wash them away. When you’re finished, you should wipe the interior down with lint-free material and blow it out with compressed air to get it completely dry. You may choose to also spray a rust inhibitor on the interior, which I highly recommend.
Next, and most overlooked, is cleaning the inside of each tubing, pipe, and hose assembly. You cannot clean the inside of these by merely blowing compressed air through them.
In order to get them clean, you either have to pump a clean solvent through them at a high enough flow rate to create turbulent flow or you have to use compressed air to drive a cleaning pellet through the conductor (hose assemblies, tubing, etc.). The cleaning pellet method is by far easier and has proven to be very effective method. This system works very well and can be done quickly.
Adding Clean Hydraulic Fluid
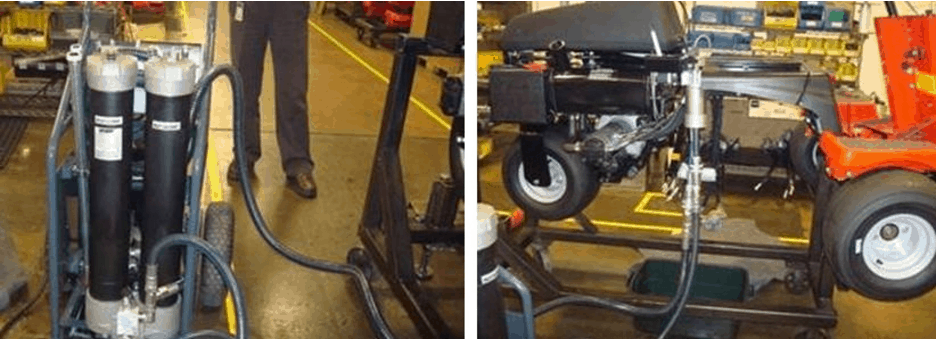
If you start with a clean reservoir and clean conductors, you’re already miles ahead of most people. The next step is adding clean fluid to the system and ensuring that the entire system meets the ISO cleanliness specification. One way of achieving this is through the use of a Schroeder Industries Filtration Station. The Filtration Station not only filters new oil coming into the hydraulic system but it is also capable of providing “kidney loop” filtration to put a final “polish” on the system fluid during startup. Depending on the type of unit you choose, you can monitor ISO cleanliness levels and water contamination levels real time and then document machine roll off cleanliness for future reference.
The inlet hose is attached to the fluid source (barrel, reservoir, etc) and the outlet hose is attached to the machine’s reservoir. Simply turn on the pump and pump fluid through the filter to ensure that clean oil is going into the system. By the way, new oil is not usually clean oil. New oil should always be filtered before putting it into a system.
Testing Hydraulic Equipment
Once the reservoir is topped off, start the machine and make sure that the pump picks up oil quickly. You may have to crack an outlet line in order to help it prime. After the pump picks up, let the engine run at low-to-moderate RPM and slowly cycle all functions on the machine multiple times. You may have to add additional fluid if the system contains cylinders.
This cycling will drive any contaminants present in the components or conductors back to the return line filter where they will be captured. Once you have thoroughly cycled the machine, you should remove the filter element and replace it with a new one. For most people, this process represents a vast improvement over what they presently do and could be considered “good to go”.
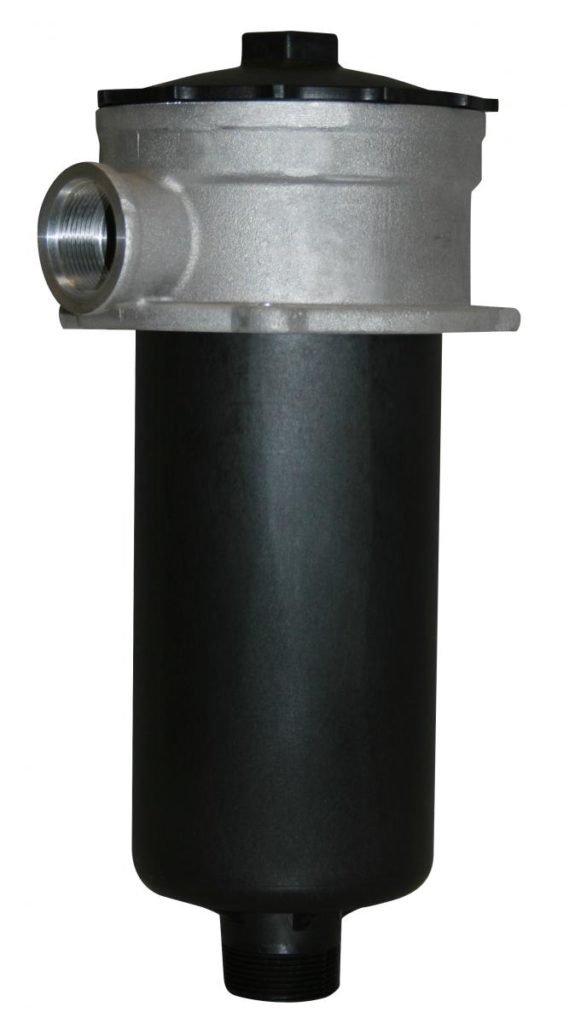
ISO-Certified Cleanliness
If you are operating under ISO processes, you will want to certify the level of cleanliness of the fluid as it left your factory. In this case, you would also need a particle counter to sample the fluid and give you an ISO cleanliness code that you would add to your documentation of that particular machine. This way, you can prove the machine left with a clean system and if a failure occurs, a sample from the failed machine can perhaps show why the system failed at a later date. A good hydraulic fluid analysis can identify the type of contaminants present, not just the size of the particles.
If we have selected the proper filtration that will maintain recommended cleanliness level for the components in your system, and if that system is well sealed and ingested contamination is kept to a minimum, your customer will enjoy a top performing, trouble-free hydraulic system as long as regular maintenance is performed.
For help in designing your roll-off cleanliness process and a filtration system that will operate in a trouble-free manner, contact the specialists at Cross Mobile Hydraulics group for assistance.