Evaluating a Systems Integrator for upcoming projects is an important part of the project process and the decision typically affects more than one project. This will end up being a relationship that lasts over a number of projects and multiple years.
Documentation
A well-established documentation system is a key to any project’s success. Any Systems Integrator should be able to describe their documentation system to you. A Systems Integrator should also have a team of well trained and versatile engineers that can support your system. A Systems Integrator can provide their engineering team’s resumes giving the customer a deeper understanding of their experience and expertise.
Previous Experience
Examining a Systems Integrator’s previous projects will be useful. Ideally, you would like to have these projects fall within the same industry as yours but it is not necessarily a requirement. There are only two types of processes: Continuous and Batch. In the case of Batch operations, they are similar in many ways so programming is straight-forward. The differences comes down to features and what special functions that can range for simple to complex and fully customization. Focusing on these key points are essentially for determining a Systems Integrator for your next project.
How Early Should You Bring in a Systems Integrator?
In any project, it is best to get all parties involved as early as possible. That being said, a systems integrator does not need to be a part of building design. Once the discussion of Piping and Instrument Diagram (P&ID) has begun, it would be a good time to get the systems integrator involved. This will give the systems integrator the ability to review the P&ID’s, estimate an I/O list, and gain an understanding of your process. Another key point here is reviewing the tag-names of the devices. this may sound insignificant but experience has shown that naming conventions, even if already established, tend to have deviations.
Benefits of a Systems Integrator
A good systems integrator will be able to:
- Help you design your control system from the ground up.
- Design and build panels.
- Provide guidance on a control system platform.
- Create and review P&ID’s.
- Provide onsite support or mobilize an engineering services group that can provide help with systems.
- Provide a knowledgeable sales staff.
- And an emergency service, available in the event of worst case scenarios.
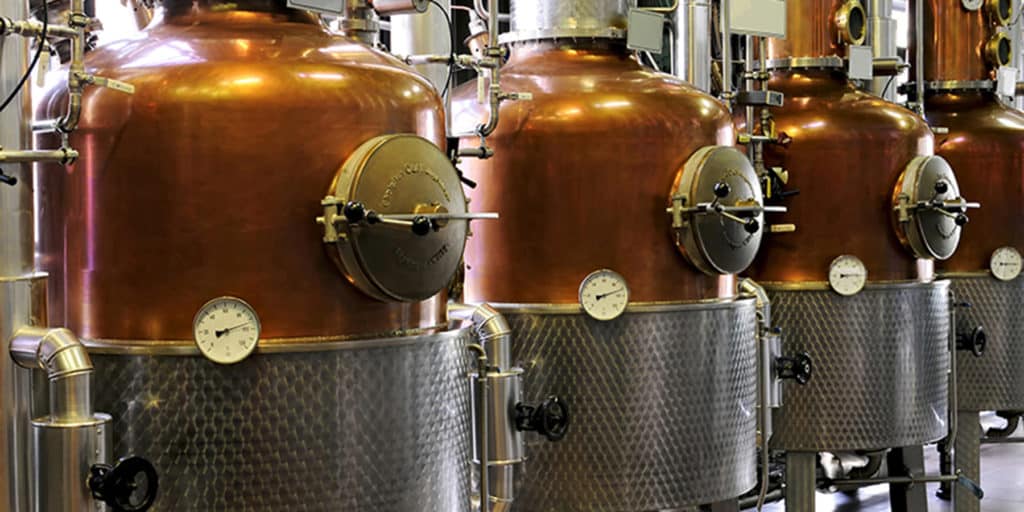
The Cost of a Systems Integrator
Hiring a systems integrator may cost more up front compared to vendor services or in-house personnel but the benefit to a systems integrator is that you get access to a much larger knowledge base that can resolve the majority of control system problems. Most systems integrators also have support contracts with their major suppliers that allow them to have priority over many others calling in for support. With access to a systems integrator and their team, you will have an easier time maintaining a schedule and sticking to deadlines.
Typically when using vendor services or in-house personnel, documentation is often overlooked. One of the major benefits of using a Systems Integrator is that you are forced to document the facility’s process and control system. These documents are given to the end user at the end of commissioning. Using a Systems Integrator allows for your in-house personnel to stay focused on their day to day and other tasks within the project.
How to Evaluate Different Control Systems
Evaluating different control systems is a difficult task that requires extensive knowledge of your process and operations. It is recommended to get some feedback from your operations department and operators that work the day to day.
The majority of control systems provide the same basic functions but differ in their special features and complicated task functions. Questions to consider:
- Am I running a continuous or batch operation?
- How much interfacing do I or my employees want to have with the programming after the conclusion of the project?
- Do I need redundancy?
- What communication do I need?
- Do I have any customization in my current control system? Do I want/need customization?
- What historical data do I want to retain and for how long?
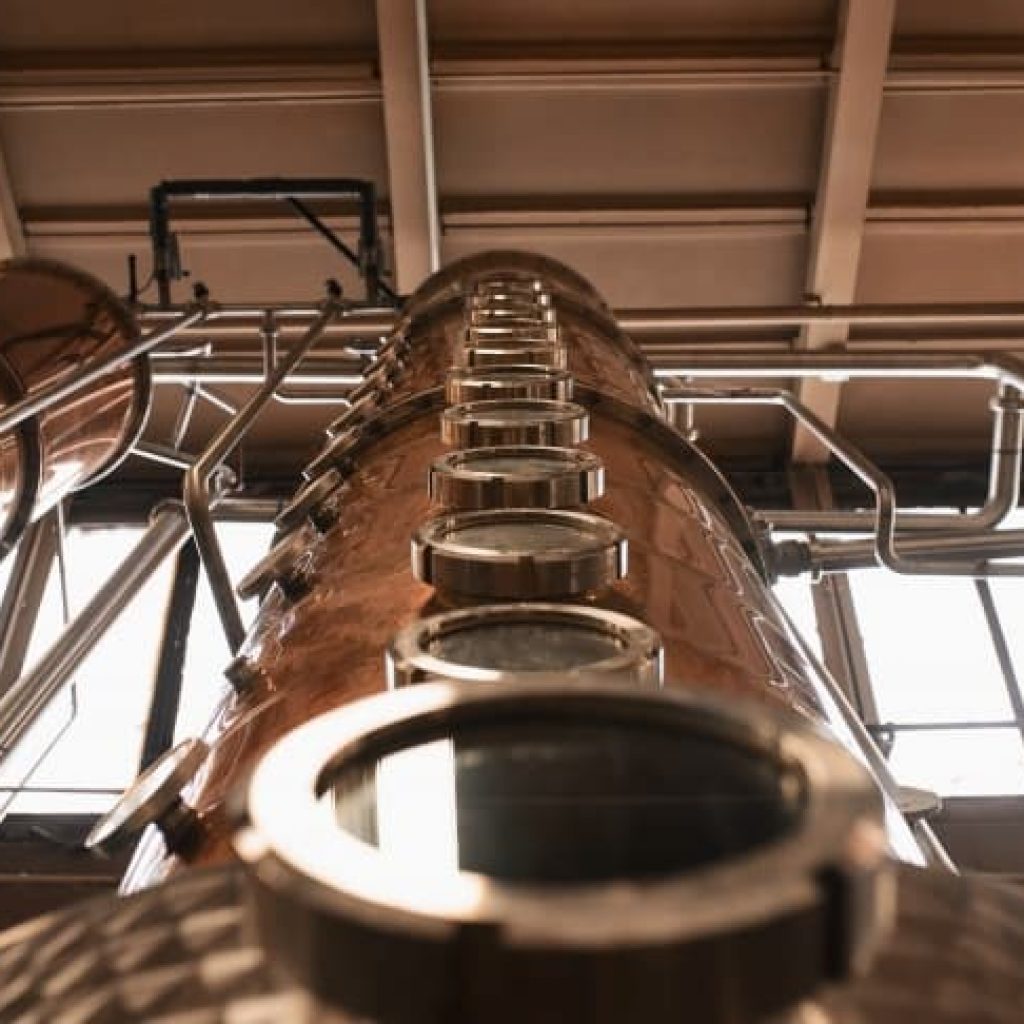
Another determining point is the existing control system:
- Is this a legacy system and – if so – does the company still exist? Is there current support for the system?
- Do you want to upgrade the control system? Is there an upgrade path for this system?
- Is starting with a completely different system the only option if no upgrade path is available? What features do I want to retain from my existing control system?
- Is my current system redundant?
These are just several questions to begin your focus on when evaluating different control systems.
Systems Integrators Are Cost-Effective vs Vendor Services
Having a local systems integrator is a luxury that most facilities do not have, so if you are fortunate to have one nearby it is strongly recommended that you use them. When planning any expansion or new facility in a different city, it would be wise to locate the nearest systems integrator.
Being able to have such expertise within such a close range can lower the obvious cost on travel time, hotel, food etc., but more importantly in emergency services. If critical issues arise that need to be addressed a systems integrator within a close proximity, can drastically reduce the amount of downtime and lost production. With the increasing threat of cyber attacks and increased security, it has become more and more cumbersome to gain remote access. There are even limitations to remote access and having a systems integrator onsite same day is a big benefit.
The down side to vendor services compared to a systems integrator is the breadth of knowledge across multiple platforms. For example, if you have a complicated system that is communicating from a Siemens PLC to a third party Allen Bradley PLC with an Iconics HMI and Pi historian, typically a systems integrator can handle all of those different platforms whereas a vendor from each would have to be contacted to troubleshoot their equipment resulting in a lot of lost time.
Interested in learning more about how we can help improve the operation of your facility? Reach out to us today! Speaking with our experts can help you both make your operation more efficient and reduce the risk of downtime. We are available to walk through your facility and help you develop a plan for upgrading your existing system and devices.