Palletizing Robot
Automated Palletizing Solutions
Cross palletizing robots offer a flexible solution to eliminate repetitive, manual stacking and unstacking tasks. The small footprint makes them ideal for tight manufacturing lines and allows them to adapt to different tasks as needed. Automatic palletizer models are available for different payloads, cycle times and column heights. They can be compact or custom-sized (based on the needs of your operation). These collaborative robots can increase worker safety, overall production, and, through a positive ROI, your bottom line.
Our Palletizers aim to:
Reduce or even eliminate employee workplace injuries from bending and lifting tasks
Allocate human staff to higher value decision-based work that is less mundane
Eliminate the need for complex robotic programming with pallet configuration software
Manage multiple production lines or package sizes with quick redeployment
Realize a valuable ROI by reducing production costs
Current Cross customers report that the payback of their system is less than two years. For multi-shift operations, the payback can be much sooner, as you can see in the ROI example below. The flexible Cross palletizing system will reduce your production costs, ergonomic-related injuries, and any quality issues. Cobots like automated palletizers are designed to integrate easily into your existing system. Creating solutions designed for your process.
Cross Company Palletizing Solutions
Cross Company palletizers offer a range of benefits that can significantly enhance industrial operations. Our advanced technology and precise automation capabilities ensure increased efficiency and productivity. And by leveraging high-speed performance and accurate stacking, Cross palletizers streamline the palletizing process, minimizing downtime and maximizing output. This leads to improved throughput and reduced labor costs, as fewer workers are needed to perform manual palletizing tasks.
By leveraging our cutting-edge technology and automation capabilities, operations can achieve higher productivity, reduce labor costs, and create a safer working environment. With our commitment to excellence and customer support, investing in a Cross palletizing solution can significantly improve the efficiency and effectiveness of your industrial operations.
These robots are designed to work alongside humans in a shared workspace, assisting in the palletizing process. Cobots prioritize safety, offer intuitive programming interfaces, and provide flexibility to handle various product types and pallet configurations, making them ideal for collaborative palletizing applications.
Industrial robot palletizers are advanced automation systems designed to handle the stacking and arrangement of products onto pallets in industrial settings. These robots offer high-speed performance, precise stacking, and versatility to accommodate various product types and pallet configurations.
Benefits of Automated Palletizing Systems
A highly performing cobot or palletizing solution translates to both increased profitability and higher safety. Robotic palletizers are now able to solve issues that their older counterparts simply couldn’t. The efficiency of a robotic palletizing machine almost lets products palletize themselves. And while the robot is doing the work, employees are able to focus on more important tasks that directly add value to the manufacturing process. Or they’re removed from potentially dangerous situations all together.
Some immediate advantages to automating the palletizing process include increases in safety, accuracy, and your bottom line.
Increased Safety
Strains and sprains are the most common workplace injury in the United States. And a leading cause of these types of injuries is over-straining from long hours of repetitive work. Introducing a palletizer onto the manufacturing line is a proven way to mitigate workplace injuries from repetitive over-exertion.
Improved Accuracy
When performing the same task over and over for long stretches of time, small errors and mistakes start to pile up. While a human operator may begin to lose focus, a palletizing robot will not. Palletizing machines are more accurate and precise and will not begin to make small mistakes after long hours of the same task.
Better Bottom Line
When it comes to manufacturing, shorter cycle times and increased throughput are crucial to your bottom line. Substantially increasing that bottom line requires a versatile, powerful automated system. With the direction many industries are moving, automated robotic solutions are increasingly becoming less and less optional.
Eliminate Staffing Problems With Automation
If you’re struggling to keep workers in positions that involve dull, dirty, or dangerous tasks, the solution may not be to keep hiring. It might be time to consider automation.
At Cross Company, we specialize in automating these hard-to-fill roles with collaborative and industrial robotic solutions. Automating these tasks not only enhances safety and well-being for your workforce but also boosts overall efficiency and productivity.
Whether you need to integrate robotics into existing processes or design a new automation system, Cross has the expertise to help. We work closely with you to develop tailored automation strategies that transform staffing challenges into opportunities for innovation and growth.
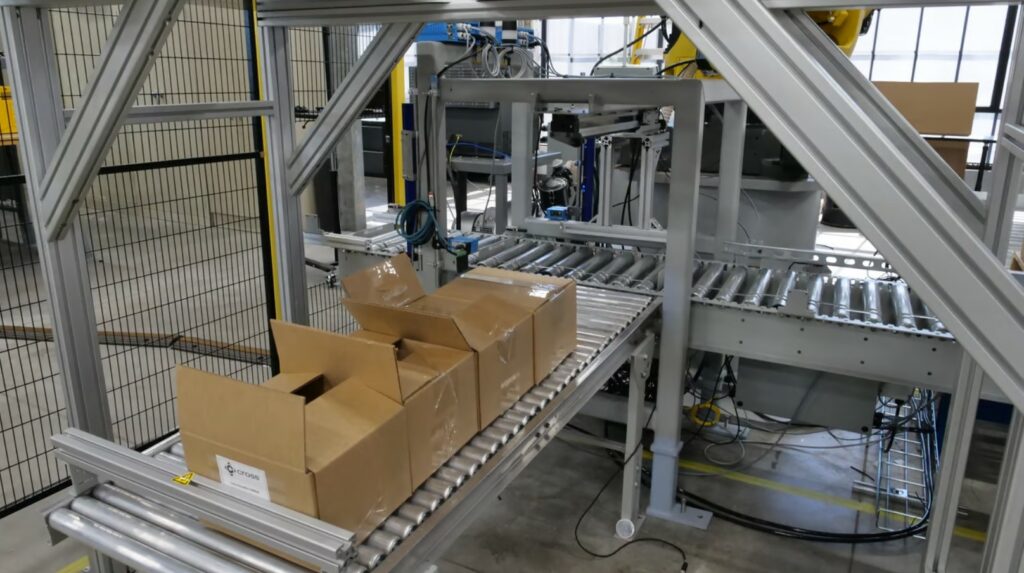
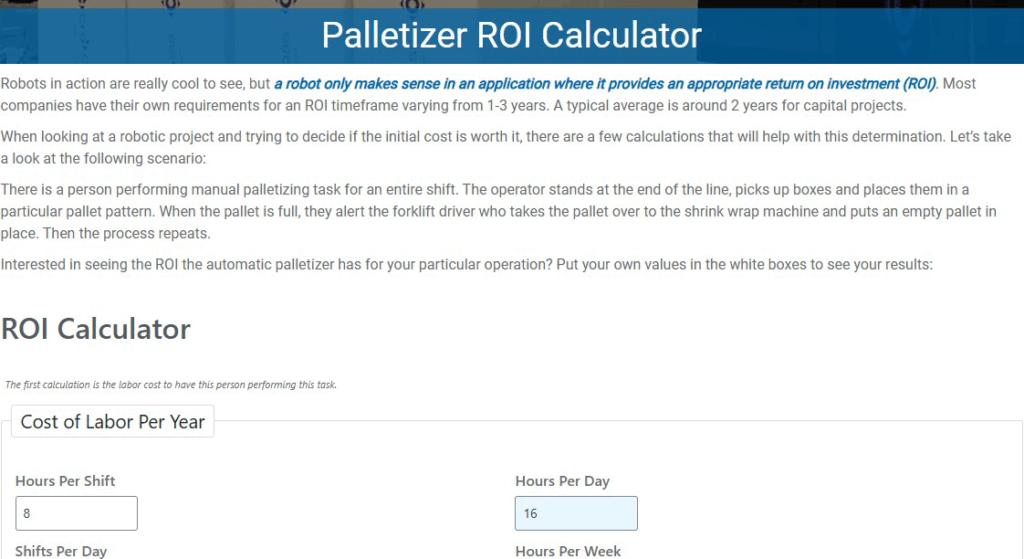
Calculate Your ROI
Robots only make sense in an application that provides a return on investment. See how much a robotic palletizing application can save your operation over time with our ROI calculator.
Custom Conveyors and Reject Stations for Your Palletizer
When it comes to your palletizing process, ensuring a seamless and efficient operation is vital. Upstream issues like improperly sealed boxes, unlabeled items, or other defects can disrupt the workflow. A highly effective solution to tackle these challenges is to implement a reject station just before your palletizer. At Cross, our dedicated team specializes in tailoring custom conveyors with integrated reject stations that align perfectly with your specific requirements.
These reject stations are equipped with advanced features such as barcode scanners and laser systems, enabling precise box measurements to verify their suitability for palletization. What sets our solutions apart is the fact that we design and build the entire system in-house. This means we can fully adapt to your configuration and dimension needs, ensuring a truly tailored and efficient solution for your palletizing process. Don’t let upstream issues disrupt your operations – let Cross create a custom reject station to enhance the quality and efficiency of your palletizer system.
FAQs About Palletizers
Implementing a robotic palletizer can have many benefits in terms of damage prevention and on-time production. When it comes to repetitive task automation, a robot will always out-perform a person. The robot moves the exact same way every single time in exactly the way they were programmed to. This effectively eliminates potential unnecessary damage to products (such as dropping or incorrect stacking). With end of arm tools (EOATs), many robots are able to utilize adaptive gripping technologies, which can prevent unwanted tearing or bending.
Several factors must be considered when deciding on the right palletizing robot for your workflow. The first step is understanding your range of products and packaging types, and determining the needs of both. Next, it’s important to consider the speed the production line needs to move. Is your potential robotic solution able to keep up? Finally, is the robotic palletizer you’re considering able to adapt to future changes in the production and manufacturing process? With these questions in mind, you should be able to determine the right palletizer for your process and needs.
A major vote of confidence from our customers is our ROI. Cross robotic palletizer customers report that their new automated system has begun paying for itself in less than two years (with some reporting even faster returns). We design and engineer robotic systems to optimize your production processes and maximize your bottom line. It’s as simple as that.
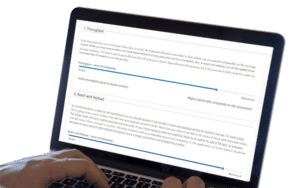
Collaborative Robot Application Complexity Calculator
How complex is your process? If you aren’t sure whether or not your team is equipped to deploy a cobot on your own, our complexity calculator will help you determine how difficult it may be.
How Can Cross Company Help You?
As modern markets become more and more competitive, the need to optimize your manufacturing process is only becoming more urgent. Industrial and commercial operations are rapidly adopting automation solutions like palletizing robots to improve throughput, safety, and quality assurance.
At Cross, we want to help make your production process as efficient as possible through strategic automation. And that efficiency also translates to a higher-quality product, a more competitive process, and a better bottom line. In today’s market, those factors may be what sets your operation apart from your competitors.
When you partner with Cross for automation solutions, you’re getting more than just a palletizing robot. You’re also benefitting from our brand partnerships, industry-leading technical knowledge, and world-class customer service. That’s not something you can get from just any palletizing automation company. See why so many operations choose Cross Automation again and again.
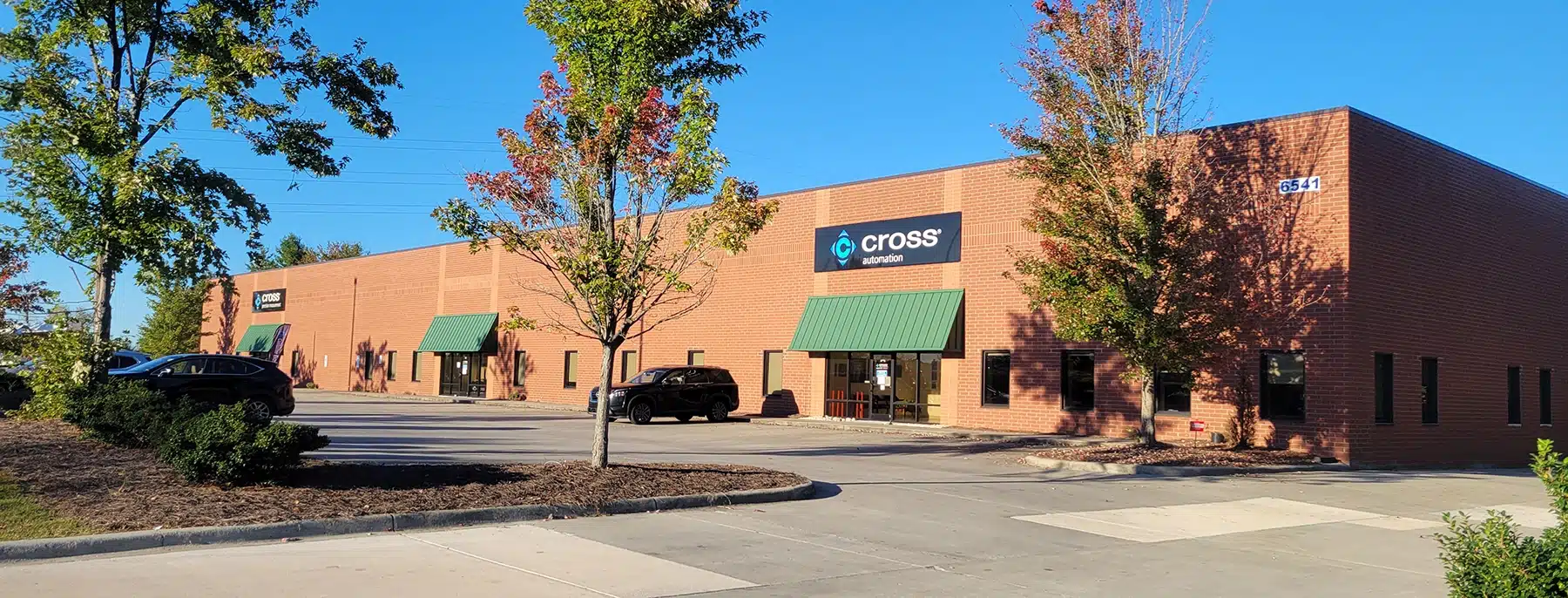