Tank Optimization
Cross Company Tank Optimization Program
The Cross Company Tank Optimization Program is an in-depth review of all tank accessories on your site by a highly qualified Cross technical expert.
We look at all aspects of your tank assembly, providing a comprehensive deep dive into the safety, maintenance, and operation of all your tank accessories.
When we’re done, you’ll receive a physical report of our findings detailing which tanks are operating as intended and which are damaged, obsolete, or in need of work. This report will provide you with actionable steps to fix any potential problems and get all your tanks to top quality.
Why Tank Optimization Benefits You
If a component of your production process was performing suboptimally, wouldn’t you want to know about it? Providing the data to ensure that every tank involved in your particular process is just what our Tank Optimization Program does. Besides the benefit of more efficient production, the T.O.P. also gives peace of mind and actionable data.
Our technical expert will examine and record all aspects of your tanks. Not only will they note locations and specifications, but they will also record any hazards or potential hazards they come across. This allows you to address issues before they become critical – or worse – deadly.
The tank optimization program gives you a wealth of data about your facility. Use it to check against inventories, develop preventative maintenance (PM) programs, consolidate vendors, showcase your batching capability and capacity, or create a timeline for replacement parts.
Peace of mind
Actionable data
Preventative maintenance
Lower downtime
Protected personnel
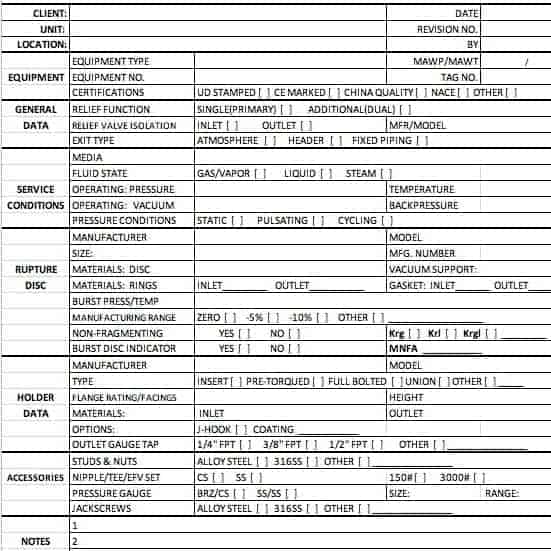
How We Optimize Tanks
Our expert will spend multiple days on your site while staying out of the way of day-to-day operations.
All of our experts have been through health and safety training for industrial manufacturing sites and will have the correct PPE, as well as an awareness of the hazards that exist.
Expect them to get dirty, however, crawling under tanks or climbing to the top of assemblies in order to gather the data they need. An escort by one of your employees will be helpful to guide them around the facility and speed your review.
Tank Optimization Program Deliverables
In its simplest form, you’ll get a consolidated, hard copy report with a summary, recommendations and your tank data. All of the information about your facility’s tanks will be at your fingertips.
This powerful data can be used for many things, including
Vendor Consolidation
Ensuring Your Records Match Your Operating Equipment
Creating A PM Plan With Priorities
Creating A Timeline And Budget For Proactive Part Replacement
Ensuring You're Ready For The Next EPA Or Safety Audit
Tank Optimization Case 1
Our customer is an international chemical manufacturer with 950 staff, on-site engineering and multiple manufacturing locations. Cross Company spent two days reviewing the accessories on their 71 tanks. We found only 13.5% of their tanks were physically in compliance with current safety standards and none of them met current EPA standards for pressure and vacuum protection data.
T.O.P. Observations
A collapsed tank
Wrong rupture disc installed or no disc at all
Improper wiring in Class I, Div I hazardous area
Misaligned flanges
Corrosion
T.O.P. Benefits
Increase safety
Decrease plant operations costs
Improve production
Decrease batch rate
Increase plant readiness for EPA inspections
Secure reduced risk position for employees liability insurance
The Results
This customer acted on their T.O.P. data and plans to have their remaining 94 tanks reviewed. In addition to addressing the missing or damaged tank protection, they are also reviewing all pressure and vacuum protections for vendor consolidation. Overall, the customer found that joining the program helped them increase safety, decrease cost, increase up time, decrease batch rate, increase EPA inspection readiness and improve their insurance position.
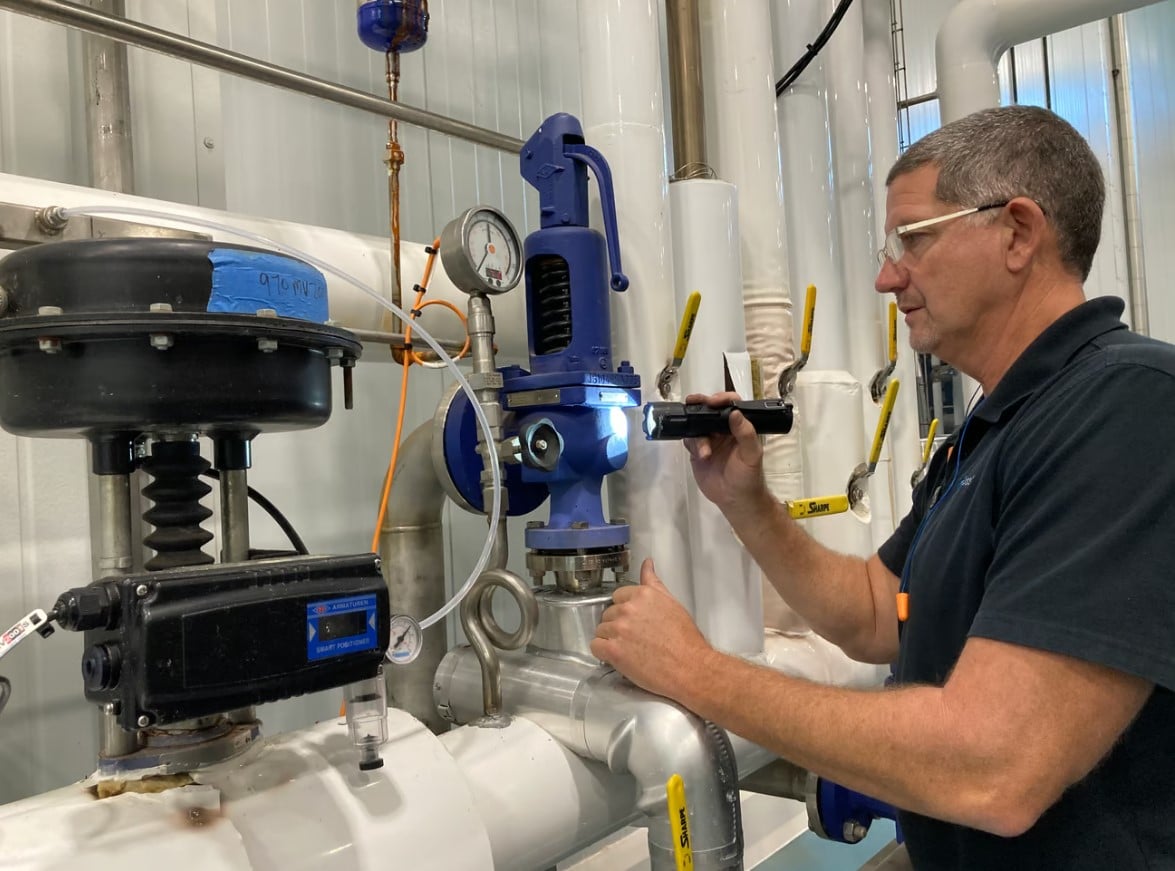
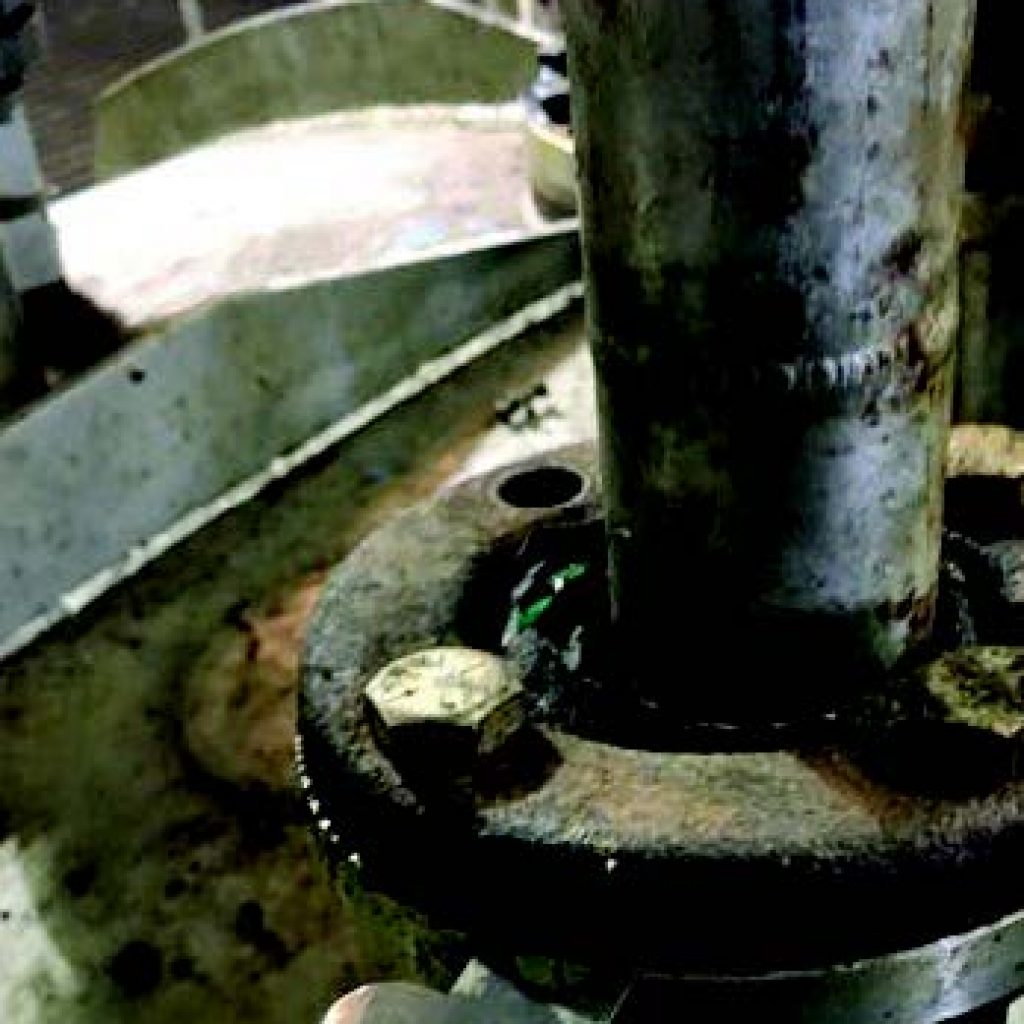
Tank Optimization Case 2
Another customer is a small batch chemical production facility with limited engineering and a staff of 42. After a four day review of the equipment on their 59 tanks we found that only 10% of their tanks were physically in compliance with current safety standards.
T.O.P. Observations
Two collapsed tanks
No PM plan or safety stock for pressure relief valves, PSV’s, or rupture discs
Improper installation of rupture discs and holders
Open outlet gauge taps
T.O.P. Benefits
Increase safety
Decrease plant operations costs
Improve production
Decrease batch rate
Increase plant readiness for EPA inspections
Secure reduced risk position for employees liability insurance
The Results
The customer purchased new protections for prioritized or dangerous tanks. Their safety manager required staff to review all of the T.O.P data and to bring their tank equipment into compliance. By doing so, they have increased the safety of their site, increased their EPA inspection readiness, increased machine up time and decreased the number of lost batches.
Why Cross Tank Optimization?
In the world of process facilities and process control applications, safety is a critical consideration. Operations of this nature come with inherent risks and ensuring the well-being of personnel, protection of assets, and ensuring compliance with standards are of utmost importance.
Cross Company Process Solutions is a reliable partner for many operations seeking comprehensive and effective industrial safety solutions. Through strategic partnerships with industry-leading manufacturers, Cross Company provides access to cutting-edge safety technologies that align with the evolving demands of modern industrial operations.
Our combination of industry-leading safety products, exceptional customer service, and technical expertise positions Cross Company as a trusted partner of industrial safety. By working with Cross, you can work to prioritize safety, promote compliance, and provide tangible value to your operation.
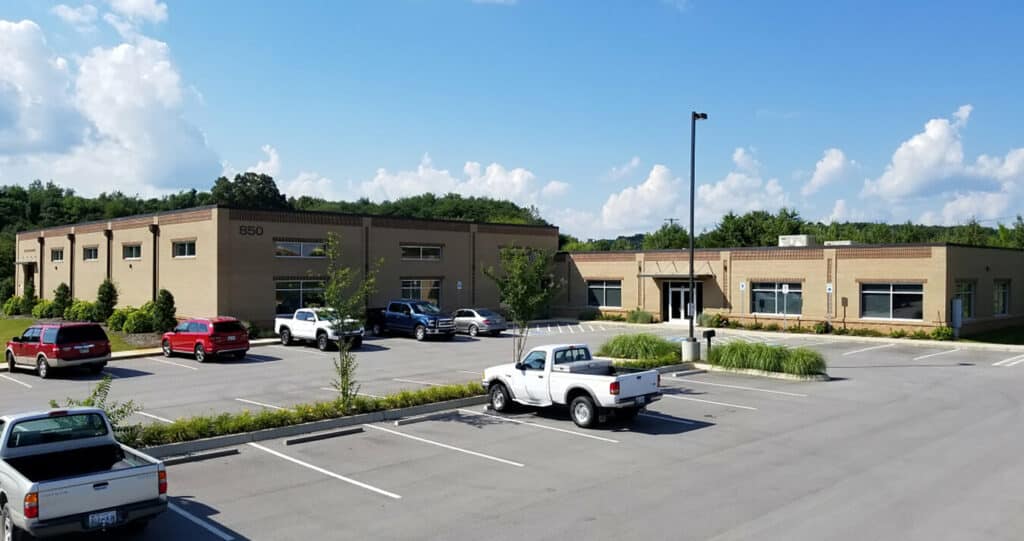
Cross Tank Optimization Brochure
Optimize your process performance. With an industry leading selection of providers, Cross experts can help your team find exactly what tank solutions your operation needs. Take a look at our latest tank optimization brochure and contact a Cross expert today!
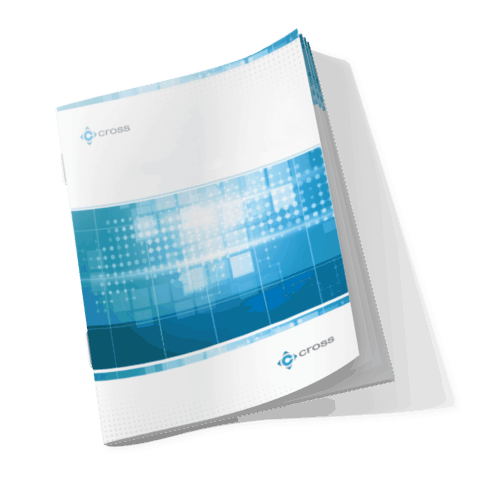
Related Pressure Management Equipment
At Cross, we offer much more than just tank optimization. We can also provide the solutions our process manufacturing partners need to succeed.
Check out our other process solutions equipment and see for yourself.