Parker Resource
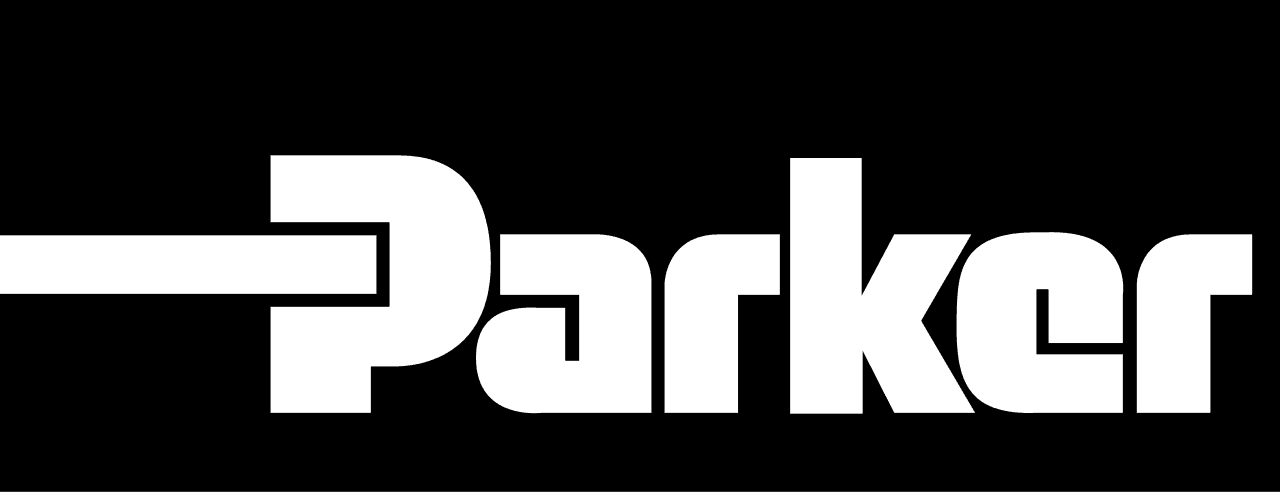
Quick connections for high-pressure, hydraulic applications have evolved significantly in response to new processes and operational needs. As industries advance their capabilities, the demand grows for coupler capabilities.
Today, couplers must ensure fluid handling applications meet both safety and regulatory standards while delivering optimized containment of a wide range of fluids that can have different operational conditions.
Operators have continually depended on reliable connections for a “non-spill” experience under the most extreme conditions, such as extreme temperature or high pressure. Manufacturers saw this as an opportunity to introduce new and enhanced couplers to the market.
Advancements have included the evolution of non-spill couplings. Also known as dry break, flat face or flush face couplings, there are reasons to evaluate these couplings for inclusion in your hydraulic applications.
1. Delivers near-zero spillage
Three Reasons to Switch to Non-Spill Couplings Graphic Quick Coupling DivisionNon-spill couplings are engineered to combat hydraulic leaks and spills with a unified design incorporating sophisticated components. For reference, the term “non-spill” regarding a coupling means a specific type of connector can reduce fluid spillage to near-zero whenever a coupling is connected and disconnected.
Designed initially as heavy-duty metal couplings for high-pressure, industrial applications, non-spill couplings have evolved into a variety of materials to complement a wide range of applications requiring minimal spillage and air inclusion.
The flush face design became a significant advancement in quick coupling architecture. A “no-drip” valve means no more than a coating of liquid will appear on the valves’ surface, establishing repeated dripless connections and disconnections for a cleaner, safer work environment.
2. Reduces air inclusion and system contamination
Hydraulic equipment relies on fluid system integrity to effectively transmit power for an instant, accurate response and reliable performance. Contamination and the loss of performance transpire when debris and air work their way into the hydraulic fluid. It’s common for this to occur when dirt accumulates on the exposed surface of a traditional poppet valve tip when disconnected. Then, when the quick coupling is reconnected, air and contamination are pushed into the system fluid as the poppet valves open. The air and contamination can cause a loss of horsepower, temperate performance abnormalities and various detrimental effects.
The flush face valves of non-spill quick couplings do not provide surfaces or areas for dirt to accumulate and collect. In environments where dirt is present, the smooth flat surface of the coupling end can be easily and quickly wiped clean. Additionally, non-spill valves keep air inclusion to a minimum because the flat-faced surface does not trap air pockets as fluid lines are reconnected.
3. Better for the environment
Fluid leaks and spills have the potential to cause significant environmental issues. If contamination were to occur, organizations would be responsible for damage to ecosystems and wildlife, resulting in high cleanup costs and federal penalties. All industries from agricultural food production to manufacturing and service operations are affected by environmental protection regulations.
Even what looks like a small leakage can sometimes leave lasting effects on our precious planet. Non-spill quick disconnects keep fluids contained and their environmental impact to a minimum. The flush face valve quickly shuts off flow when fluid lines are disconnected and is engineered to eliminate spillage and fluid loss.
Read the original article at Parker which features some of their non-spill quick couplings. To learn more about non-spill couplings or hose and fittings in general, reach out to our experts today or stop by one of our hose stores. We are here to help you find the perfect parts for your specific application needs!