Parker
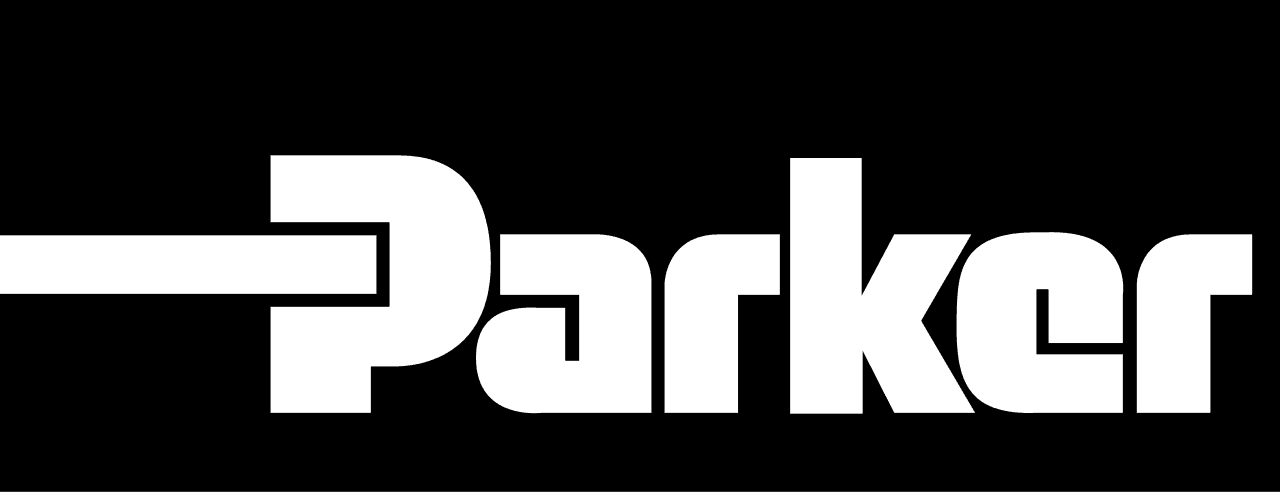
Overview
Parker Hannifin is a Fortune 250 global leader in motion and control technologies. For 100 years the company has engineered the success of its customers in a wide range of diversified industrial and aerospace markets. Parker’s engineering expertise and broad range of core technologies uniquely positions the company to help solve the world’s greatest engineering challenges.
With a background specializing in hose and fittings, automation, and mobile hydraulic and control systems, Cross Company is an ideal distributor for Parker products throughout our territory in the Southeast United States. Our hose and fittings group operates multiple Parker Hose Stores throughout North Carolina, our automation group utilizes Parker Automation products within our automation offering, and our mobile hydraulics group incorporates high quality Parker products into large scale projects for OEMs.
For more information about Parker Hannifin products and solutions, contact a Cross team member to discuss your project or application. Our experts in their respective fields can help you determine the best option for your operation, with the quality of a Parker Hannifin solution.
Featured Products
At Cross, our team works with a number of providers such as Parker to offer an industry-leading variety of products and solutions. This ensures you have the options you need working with one vendor, Cross. Keep your project simplified, yet find the best solutions from the best providers. Take a look at the featured products we have available and contact a Cross team member to learn about the full availability of products with Cross.
Available In The Following Areas
Find Parker Near Me
Resources
Videos
More information From Parker
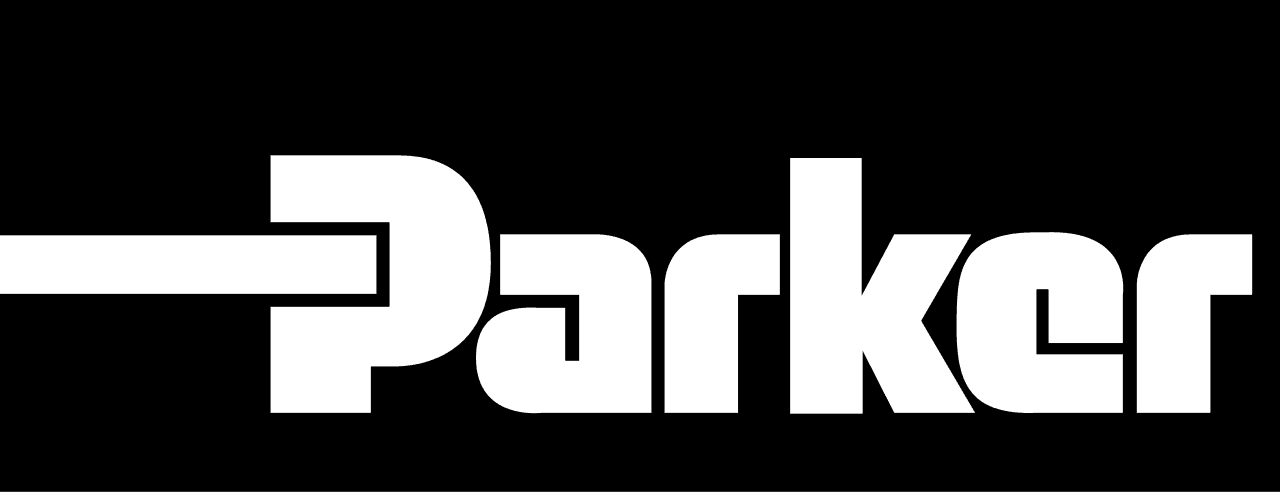
Interested in learning more? Contact a Cross team member today to discuss your application and see how we can help your operation!
Latest Parker Resources, News, and Events
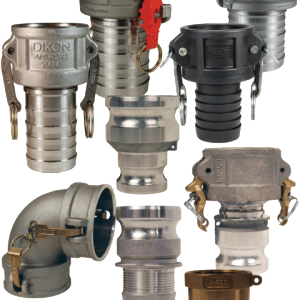
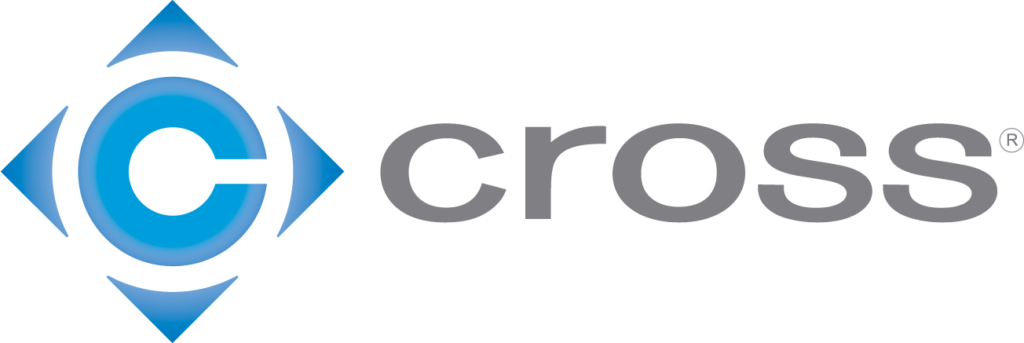
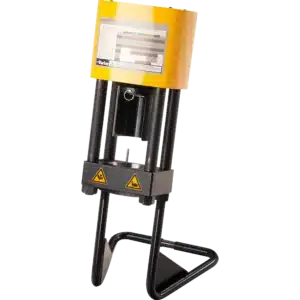
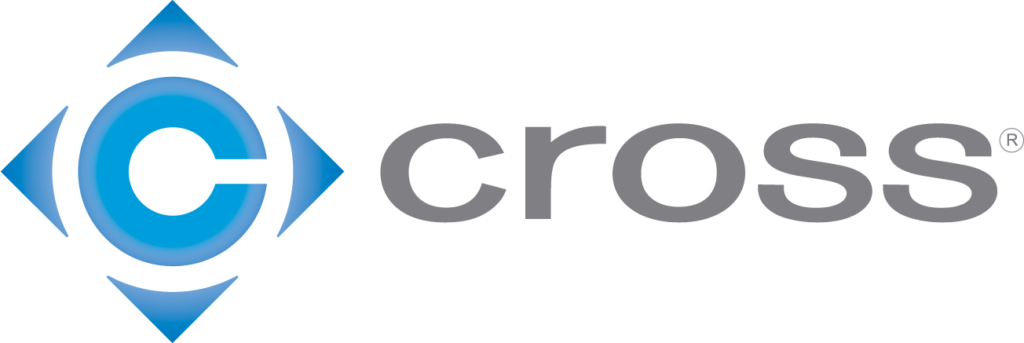
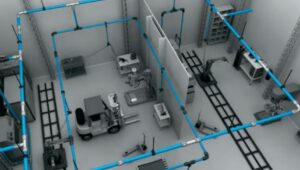
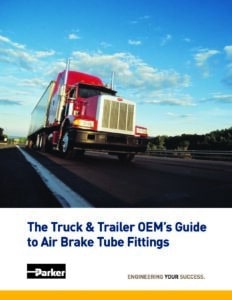