Numatics Resource

Numatics Inc. is a leading manufacturer of pneumatics and motion control products. As one of the largest supplier-partners in the US, Cross Company’s Automation Group works with customers to apply these products to create unique solutions. The this article addresses the role of pneumatics in machine safety, and a unique solution that Numatics has created to offer machine builders and end users the most flexibility in order to meet the latest safety standards.
Our automation team has expertise in applying pneumatic solutions to improve machine and manufacturing process performance. Please contact us to discuss your unique challenges so that we can share our expertise with you.
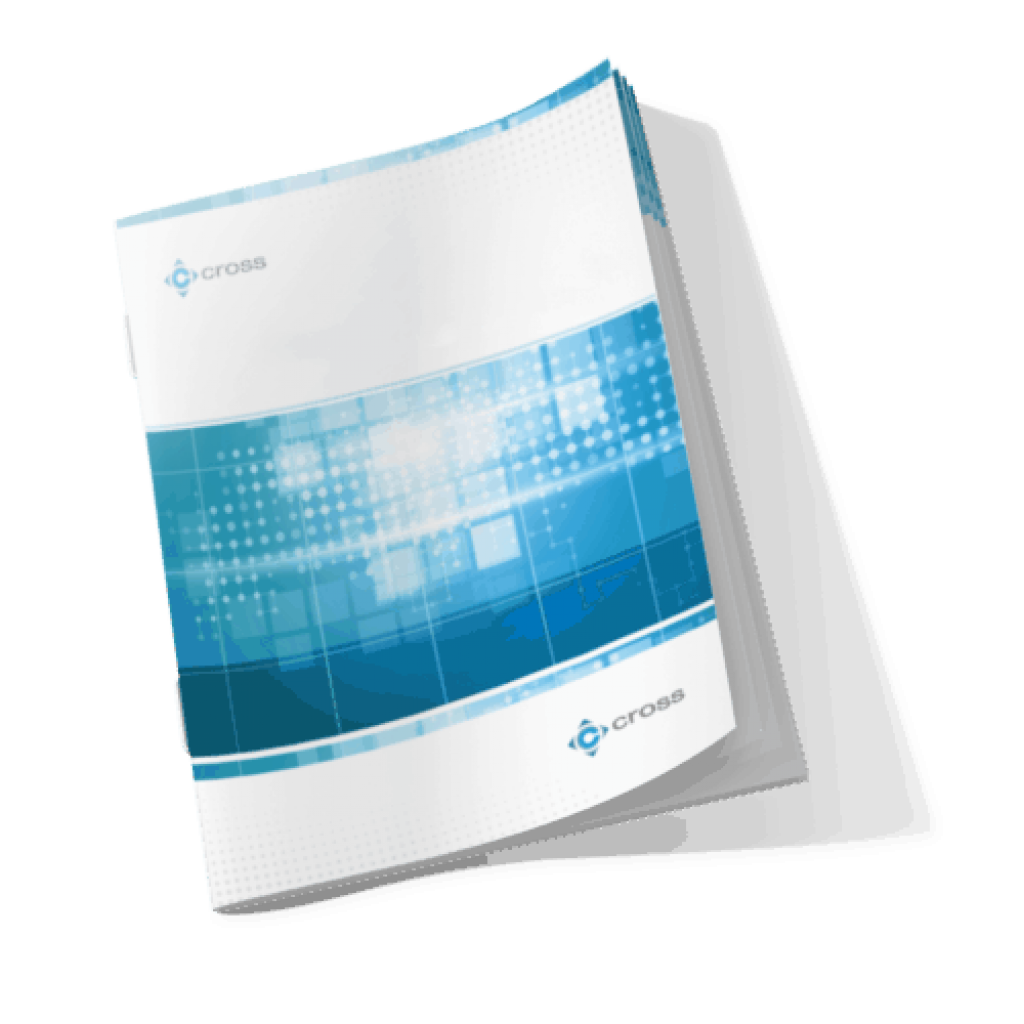
Are you interested in a Numatics product? Fill out our contact form with some details about your application and we’ll have a specialist get in touch! Also, learn more about Numatics as a products and solutions provider for Cross.