Since Siemens acquired Moore Products in 2000, they have dutifully supplied the hardware for the very popular APACS Control System. However, APACS was announced “mature” in 2010 with planned support running through September 2020. The support will not abruptly end on October 1, 2020, but it will not be guaranteed past that date.
If you have an APACS system, more than likely you have considered options for what you will use next or how you will migrate your system. Although there are many valid actions including full rip and replace and migration options (even from other vendors) this technical guide will discuss phased migration options from APACS to PCS 7. For more information about legacy control system migration, take a look at our article: 6 Immediate Action Items for Aging Control Systems.
HMI Upgrade
The first part of APACS that was declared mature was the ProcessSuite HMI. ProcessSuite runs on Windows 2000 and while we’ve seen customers upgrade it to XP, that OS was not supported and in some cases caused serious issues. There are still quite a few systems running on ProcessSuite and the customers running it are very familiar with finding parts online. The PCs are the most difficult components to find as you cannot buy a new PC that will run the legacy OS, nor can you buy a new copy of Windows 2000.
Migrating your ProcessSuite to APACS OS is a great first step to get your HMI on supportable PC Hardware, Microsoft Windows operating systems, and Siemens software. For this migration, you can make the new system look exactly like the old with the same functionality. However, if you are making the change, this is a good time to take advantage of some of the functionality of the newer PCS 7/APACS OS.
Conventional or Virtual
When you do move to APACS OS, you can use either a conventional client server architecture or a virtualized architecture. Several years ago, proposing a virtualized system was considered risky as we were used to redundant servers and multiple clients for redundancy. As true server class machines have migrated into process control systems, they have RAID technology, or redundancy built into them, and are much more reliable than the standard server PCs of the past.
When you go to a virtualized architecture, the high-powered server can withstand multiple failures within the server and continue to run. If a hard drive goes bad, you can hot swap to a new one. Gone are the days of having to upgrade all of your client boxes and reloading software on each client, which can take hours to load!
If you have a thin client failure, you can simply plug a new one in, give it some address information, and it will run the software from the server within a few minutes. This also makes upgrades much easier. Everything is upgraded on the servers. There is nothing to upgrade on the clients. Another advantage of the thin clients is that instead of costing several thousand dollars they are several hundred dollars.
Controller and I/O Migration
Once you have migrated the HMI, you can then focus on migrating the Controller and I/O. One of the big advantages of having the PCS 7/APACS OS is that you can have a mix of APACS and PCS 7 hardware working in one HMI. This is sometimes referred to as a dual leg system and it allows you to change out the APACS in phases.
For many years Siemens offered a controller-only solution which would allow you to replace the APACS controller with a DP IOBUS module to communicate from a PCS 7 controller to the APACS I/O. There were only a few customers that took advantage of that module, rather opting to replace the controller and I/O at the same time, so the DP IOBUS module is no longer promoted. The PCS 7 controllers are much larger than APACS controllers, so you will likely be able to get by with far fewer PCS 7 controllers than ACMs in you APACS system. A typical APACS system can fit into a single PCS 7 controller.
You can replace the entire system at once, but many times customers need to maintain the uptime of their system or simply do not have the budget for a full rip and replace of the entire system. If you need to maintain uptime and rarely have long outages, then a phased migration of the hardware may be the better approach. You can change out your system one APACS rack at a time until you have migrated the entire system.
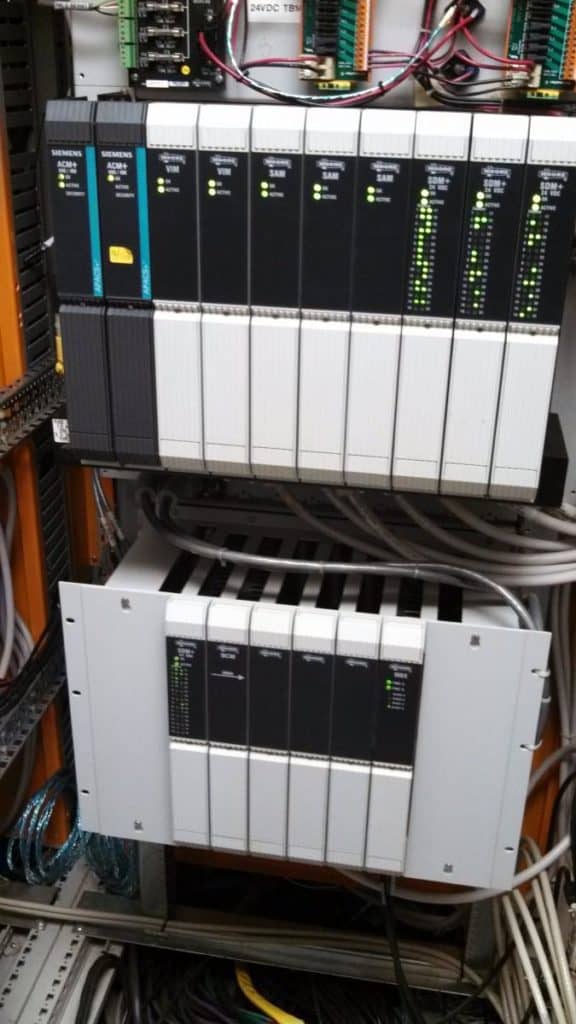
Another advantage of this phased approach is that with each APACS rack you decommission, you have created additional spares to keep your system running through the rest of your migration. A multiphase migration, like we have performed several times, enables a customer to take short outages and upgrade different units of the plant over several years. This helps with the downtime and budget constraints typical in many facilities. For more information, read our article: 5 Ways to Minimize Risk When Migrating Your Control System.
I/O Cable Solution
Siemens has recently released a cabling solution for the APACS Marshalled Termination Assemblies (or MTAs). If your system used MTAs, then you can replace the APACS I/O modules with PCS 7 I/O modules and use the cabling solution to plug into the existing MTAs. You will have to design the wiring on the new I/O side of the cable, but the MTA cable connector will simply plug into the MTA and you are ready to run. This means you will not have to change your field wiring terminations. This is a huge time and cost savings, especially if you have a large system. If you have to re-land all of your field wires, you will add significantly to your turnaround time.
If you used MTAs in your system, then you have a potential to engineer, build, and Factory Acceptance Test (FAT) your system ahead of time. When the new cabinets or backplanes arrive onsite, you simply have to remove the APACS hardware, replace it with the PCS 7 hardware, and connect the new cables to the existing MTAs. You could be testing I/O within minutes of placing the new hardware, as there will be no rewiring of field devices required.
What is in the Future?
PCS 7 Version 9, plans for full support for redundant Profinet. This is the biggest advantage that we see coming in the next version. Currently, the controller to I/O communication is by Profibus DP. By adding the option of Profinet, which is an Ethernet-based communication protocol, there will be several advantages. The ability to use Ethernet switches will provide you with more bandwidth and higher speeds of communications, thus providing more throughput, at a lower cost.
Contact Cross
For more information, contact a Cross team member and our experts can help ensure your process is up to date and running as efficiently as possible.