During the initial design phase of your mobile vehicle, one question that needs to be addressed is “Do you want to utilize a centralized control system or a distributed control system?”
In other words, do you want a stand alone PLC (centralized control system) with discrete wires running to each component on your machine, or do you want to distribute some of the control functions to components on your machine (distributed control system). Both designs have their pros and cons, and a lot depends on your vehicle’s complexity.
Centralized Control System
Machines with centralized control systems have relatively few work functions where a lower number of controller inputs and outputs are needed. Hard wiring is done between components on the machine, except for a display, if needed.
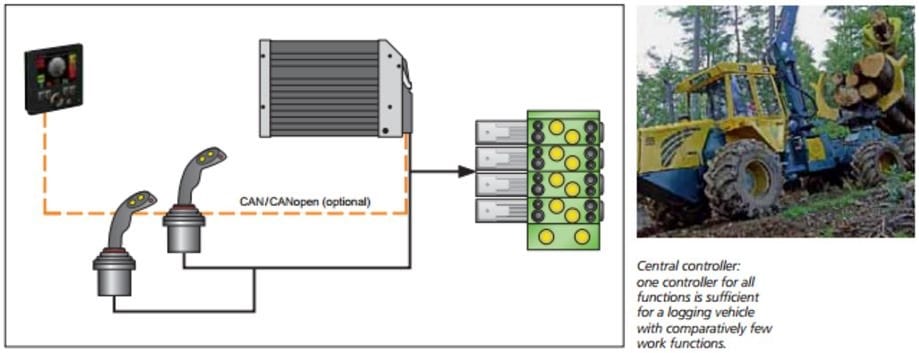
Typical applications would be:
- Trailer mounted systems
- Access platforms
- Compact construction machines
- Simple ground support equipment
With a centralized system, you are increasing the size and cost of your PLC because it requires more inputs and outputs. You also have more wires to run throughout your machine, which increases your chance of a wiring issue in the field. This, in turn, increases the cost of wiring, and also the overall weight of your vehicle, reducing efficiencies.
One of the biggest challenges we see when troubleshooting vehicle issues is wiring errors, mislabeled wires, and loose connections. This also limits the amount of troubleshooting you can do with the components on your vehicle. Sure, you can tell when something is turned on or off, but that is about the limit of what can be provided to an operator or to service personnel.
Distributed Control System
Machines with distributed control systems have a larger number of work functions and this design reduces wiring complexity. Input and Output modules, joysticks, and CAN switches are connected via CAN to the centralized controller, and is this minimizes wiring.
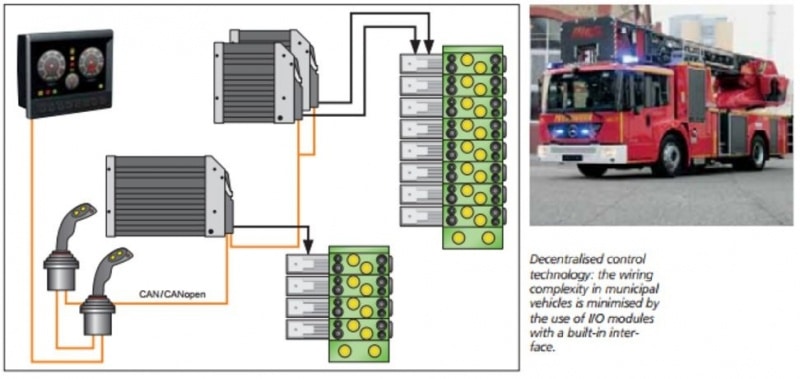
Typical applications would be:
- Complex construction machines
- Large drilling platforms
- Municipal vehicles
- Mining equipment
With a distributed control system, you have components on your vehicle that are CAN enabled, reducing the total number of wires. Your main PLC will have fewer inputs and outputs, as these signals are being transmitted via CAN communication, so typically it will be less expensive and have a smaller physical footprint. CAN components are more expensive than traditional discrete components, but can provide additional diagnostics, and reduced wiring.
One challenge with a distributed control system is that you can have long CAN lines running throughout a vehicle. These can be difficult to troubleshoot when you have communication issues. CAN lines have a limited effective length and you have to be mindful of the amount of communication traffic on those lines. If not, you can slow your vehicle down, or even lose data packets, causing vehicle faults.
To get around this, you can utilize controllers that have multiple CAN lines to distribute the communication traffic, but that increases the complexity of your electronic controls design.
Which Is Right For You?
Here at Cross Company, we have found that from a cost and troubleshooting perspective, a mixed system usually works the best. Sixty percent of your wiring is usually found in the cab or control area of your vehicle. To reduce this wiring, we utilize CAN based components such as the CAN rocker switches, CAN keypads, CAN enabled power distribution modules for controlling high current devices, as well as other CAN components, such as joysticks and displays.
All of these components can be located in a centralized area for short CAN line runs, and this dramatically reduces the overall wiring on a vehicle, increasing the amount of diagnostics that is available to an operator, and can be very cost effective. This allows us to use a smaller, lower cost PLC which can be important on vehicles that have limited space.
This type of solution gives our customers a vehicle that is easy to troubleshoot, is easier to wire, and allows them the flexibility to add additional components in their cabs, should the market require that. Here at Cross Company, our goal is to be an extension of your engineering group. Work with our team of engineers to determine the best control system for your project.