The following feature originated in a whitepaper from Metso Automation – a valued partner with Cross Company
Consider Long-Term Impacts of Purchasing One Valve Option or Valve Supplier Over Another – Cost Differences Can be Dramatic When All Cost Factors are Considered
Total cost of ownership certainly isn’t a new concept, but it is a valuable tool today with process industry buyers and purchase influencers in making informed purchasing decisions. Look at the complete cost of a product over its entire life cycle, not just the purchase price, but service and spare parts as well. Consider these factors below when deciding on a smart valve purchase for your process.
1. Specify the right valve for the application
Specifying the right valve is simply a function of understanding your process parameters and then applying knowledge of valve characteristics. Misapplying a valve in one way or another can effect the cost dramatically. For example in this real instance, Metso installed a valve controller on a customer’s existing control valve and discovered thru diagnostics that the valve was consistently 5-10% from full opening. This meant that the specified accuracy of the control valve had been compromised. This led to the recommendation of installing a smaller, more precise control valve that ultimately helped the customer avoid wasting .43 tons of chemicals per day.
Specifying a high-performance butterfly valve instead of a gate valve? Historically gate valves have been the popular choice but almost always cost much more over time than high-performance butterfly valves which offer lower installation costs, lower maintenance costs, more uptime and lower costs of automation. Talk about a dramatic difference.
Bottom line, its to your advantage to partner with a local valve expert when it comes to experience, valve sizing and selection software. Take the uncertainty out of your selection process and make a wise valve decision.
2. Select the best seats, seals coating materials and trim
Seats
Seats have an important bearing on shut-off performance and longevity of your valve. For example, Metso’s Xtreme® technolgy provides tight shut-off in higher temperature environments than filled PTFE and does not increase valve torque requirements. For one customer, switching from PEEK to Xtreme seats allowed for the specification of more economical high=performance butterfly valves and ball valves in a wider range of applications. This permitted the use of smaller, less costly actuators and allowed the customer to consolidate and reduce valve seat inventories.
Coatings
For metal-seated ball valves, properly selected coatings reduce the friction between the ball and seats, allowing for smooth sliding operation over numerous cycles, minimizing damage and wear due to galling, abrasion , erosion, particle impact, cavitation and thermal swings. Reducing friction in the trim lowers the valve’s operating torques, which has several advantages. Lower valve torque allows a smaller actuator to be used – which is more economical, results in smaller envelope dimensions of the assembly, improves signal response in control service and simplifies selection of accessories to meet cycle speed targets and other special requirements.
Trim
In certain applications, high media velocity and large pressure drops across the valve make the generation of noise, vibration and/or cavitation inevitable. Metso’s unique Q-Trim® technologies employ several approaches within the valve itself to dramatically reduce these effects.
Q-Trim® has been the industry benchmark for rotary noise attenuation solutions in challenging applications. Metso adds a new level of performance with Neles Q2-Trim™ which solves aerodynamic noise problems and reduces noise up to 30 decibels compared to a typical control valve.
3. Investigate the Real Quality of the Valves You’re Buying
Living in a world of global sourcing where valves are often manufactured in faraway places has resulted in questionable integrity of raw materials and castings. What you should know is that just because a manufacturer claims conformance to standards certificates doesn’t prove they have an adequate solution for you. The problem with the standards is that they only outline minimum requirements. Tighter limits and more stringent quality controls are required in order to optimize performance and keep your costs low. Even simple things such as material chemistry, or how valve bodies are loaded in heat treatment furnaces during the manufacturing process, can impact valve casting quality and ultimately your results.
For example, valves with porosity problems can often escape detection. But porosity is a problem that can be prevented through the implementation of specific, strict QC and manufacturing practices. Lack of such procedures can lead to valves that theoretically meet standards but cause significant problems later in your process. To protect yourself, ask your valve supplier to detail the steps they take to eliminate casting quality issues.
4. Consider a Single Resource for Your Valve Package Purchases
You may have already limited your valve purchasing to a small number of vendors, but are they providing you with fully-integrated package solutions? Consider Metso valves and Cross Company’s Instrumentation Group for a reliable, trustworthy and cost savings solution for your valve requirements. The team at Cross can suggest the correct Metso solution and will provide you with the best customer service in the industry today.
Metso’s valve packages often perform more reliably because their components are designed and engineered to work together. Parts and material have also been manufactured to the same stringent quality standards using best practices and the latest technologies. This can help mitigate your risk and cut down significantly on your initial investment, which is one of the keys to minimizing total cost of ownership and maximizing ROI.
5. Keep Up With Required Maintenance
You may have already limited your valve purchasing to a small number of vendors, but are they providing you with fully-integrated package solutions? Consider Metso valves and Cross Company’s Instrumentation Group for a reliable, trustworthy and cost savings solution for your valve requirements. The team at Cross can suggest the correct Metso solution and will provide you with the best customer service in the industry today.
Metso’s valve packages often perform more reliably because their components are designed and engineered to work together. Parts and material have also been manufactured to the same stringent quality standards using best practices and the latest technologies. This can help mitigate your risk and cut down significantly on your initial investment, which is one of the keys to minimizing total cost of ownership and maximizing ROI.
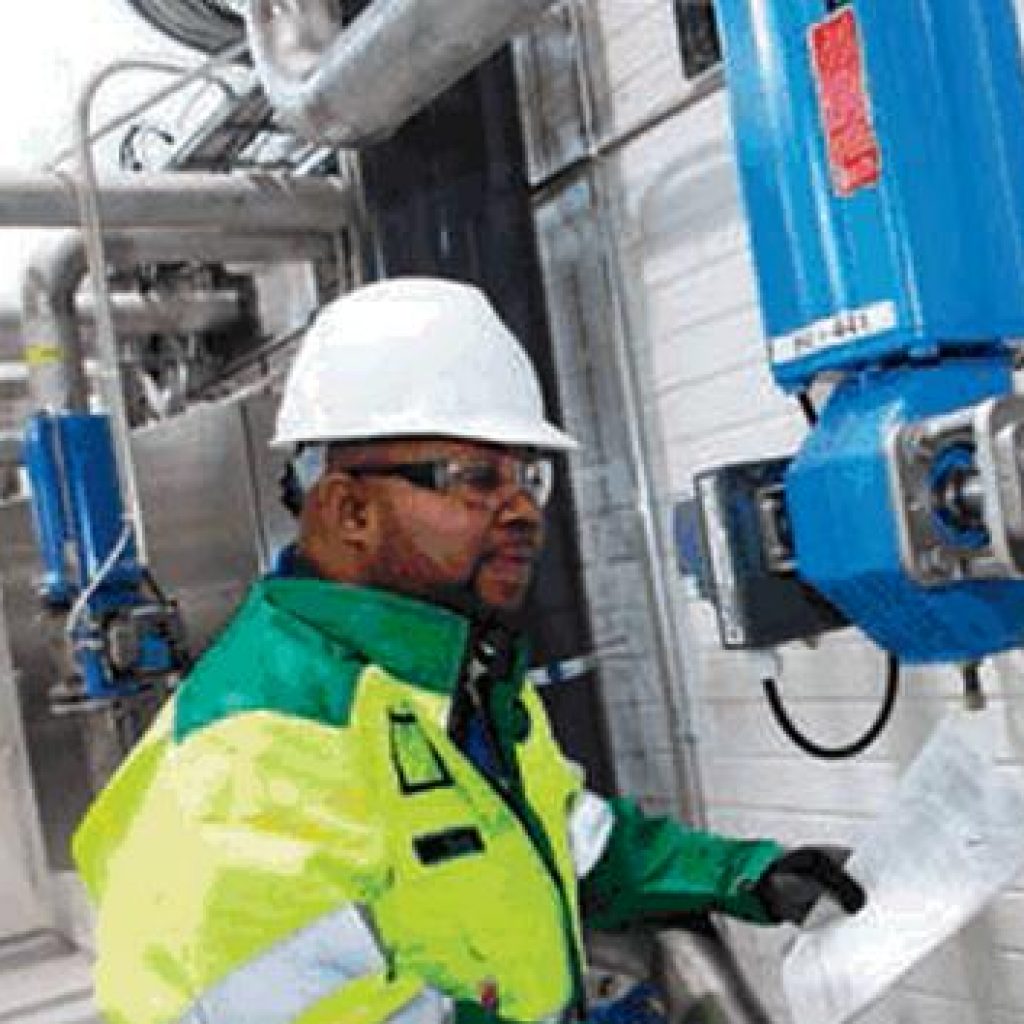
6. Optimize Spare Part Inventories
Check with Cross Company’s Instrumentation Group to help you perform an analysis of your Metso valve inventories. Based on equipment ratings, we can help you develop an inventory strategy aimed at reducing redundant or unnecessary inventories while optimizing the impact of the remaining stock. This will ensure that the most critical components are readily available when you need them.
7. Pick the Right Partner
Cross Company is a proud distributor for Metso products throughout several of our territories in the United States. Our technical expertise and relationship with Metso, providing brands such as Jamesbury, Neles, and StoneL, make us the ideal partner for valve solutions. Contact one of our team members today to discuss which Metso products are right for your operation.
Interested in sharing or reading the original material? Download the whitepaper from Metso: 7 Ways to Lower Your Total Cost of Valve Ownership