Paul Badowski | April 27th, 2016
Many of our OEM’s are going through the process of changing to Tier 4 diesel engines and controls. In smaller horsepower designs, this may be the first time they are dealing with electronic engine controls and the J1939 control networks. Prototyping and testing with these new engines and controls could not be more critical. The emissions reduction has added heat load to the engine. Cooling systems must be resized and tested.
J1939 is the SAE specification which designates specifics of a series of networks. Controller Area Network (CAN), is one of those networks. Tier 4 emissions have monitoring requirements which are handled through the network. This network broadcasts engine parameters and readings. By tapping into this network, you have a powerful resource for monitoring and controlling diesel engines.
By adapting hydraulic controls to operate within the J1939/CAN networks, we can team the hydraulics with the diesel engine. These functions can be useful to maximize system performance. We can sense when the engine is loading up and ramp down the hydraulics so we don’t stall. We can turn off machine functions if the engine gets too hot. One network controls many functions.
Two wires are all that is required to access this powerful tool, CAN + and CAN -. Each individual device needs its own power source, so there are normally 4 wires, 2 CAN and 2 Power.
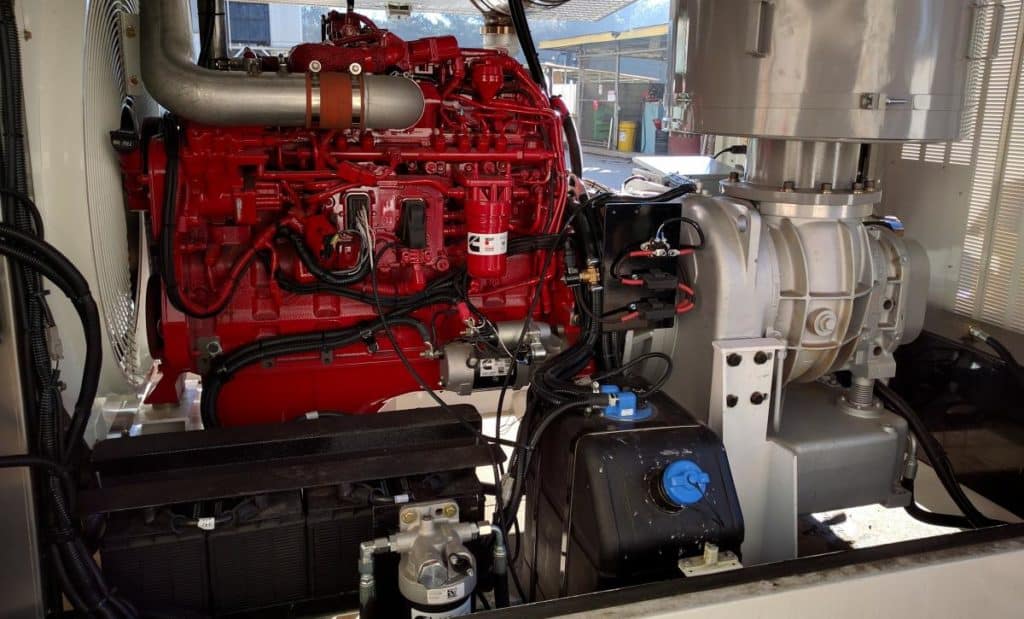
These Tier 4 engines require additional cooling compared with their previous similar HP counterparts. Be prepared to increase the radiator and oil cooler size. The engine manufacturer will provide specifications for the radiator which will include an overflow tank (and tank sizing). There will also be a Charge Air Cooler (CAC), requirement which can be mounted as part of the radiator package. The CAC maintains the temperature of the air exiting the engine’s turbo. This cooler air entering the engine improves the volumetric efficiency of the engine.
After the system is installed and operational, the diesel engine manufacturer will perform a test to certify the application of the engine and engine systems. This is an important step as there will be no warranty on an engine without the diesel OEM’s certification. The stringent government requirements on diesel engines and emissions will also require written documentation. Your diesel supplier will help with you with these government requirements.
To go along with the added electronic controls of the engine, the OEM will be required to design a wiring harness which will connect the various components of the engine. The engine OEM will supply the Electronic Control Unit (ECU), but it is up to the OEM to make all the connections between the ECU, the after-treatment system, and a control package. Ignition, Diesel Emissions Fluid (DEF) system, tachometer, speedometer, engine temperature will need to be controlled by a Tier 4 controller. This controller has built in functionality to monitor the DEF system and cycle it, as required, to control the engine’s emissions.
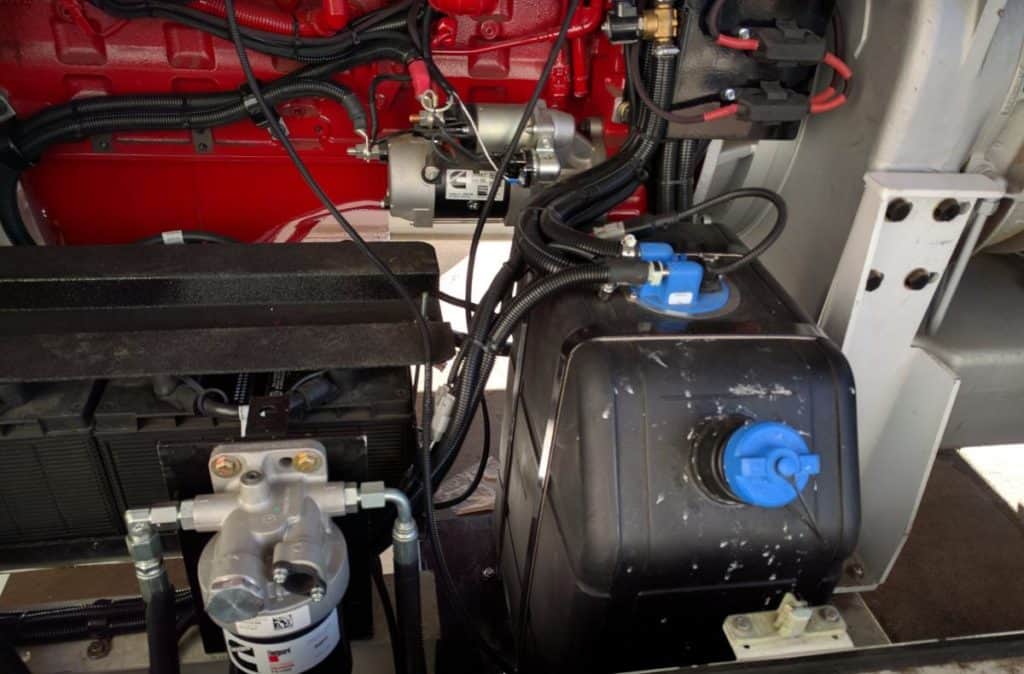
In the case of Cummins, you must stay up to date with Cummins Engineering Bulletins (CEB’s). This is the new name for their Application Engineering Bulletins (AEB’s). These contain the most up to date information and corrections which have been made as they learn more about each Tier 4 engine. (You will find documents with either title until the transition is complete.)
Other engine manufacturers will have similar documents with different names but the bottom line is there are important “running changes” being made with these engines, so make sure you have the latest information from which to work.
Whether developing a completely new machine design or just changing part of a machine, completely prototype testing a Tier 4 engine application is absolutely necessary and required. Although many times we are pushed by customer demands, we need to allow extra time for this important process. If you think you need 40 hours, plan on 80 hours; as Forrest Gump told us, “Stuff Happens”.